CLOSING the GAP
The bad news is there is no magic potion or miracle equipment that catapults a manufacturer to the productivity peak.The good news - on the heels of the widely followed independent audit of progress known as the Harbour Report - is that anyone can get there.For the first time in the history of the Harbour report, a car plant run by a Detroit automaker - Ford Motor Co.'s Taurus/Sable assembly plant
August 1, 2000
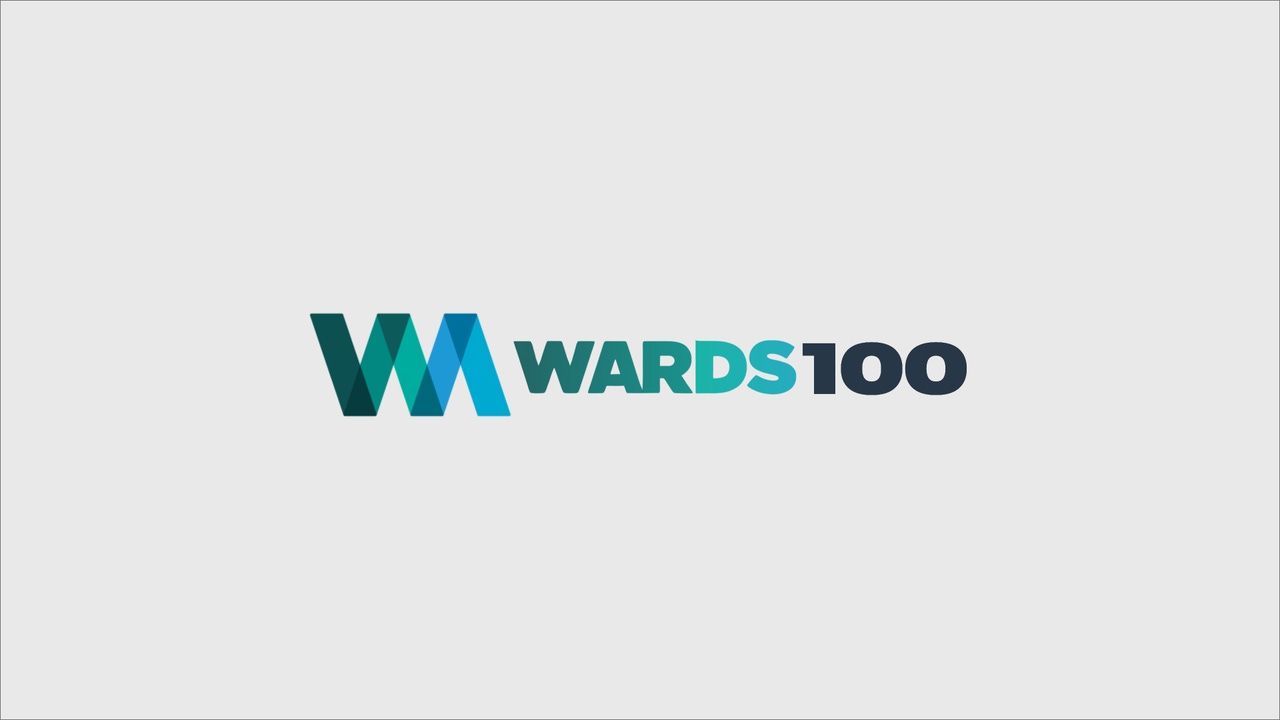
The bad news is there is no magic potion or miracle equipment that catapults a manufacturer to the productivity peak.
The good news - on the heels of the widely followed independent audit of progress known as the Harbour Report - is that anyone can get there.
For the first time in the history of the Harbour report, a car plant run by a Detroit automaker - Ford Motor Co.'s Taurus/Sable assembly plant in Atlanta, GA - was ranked as the most efficient in North America in labor productivity.
The secret to this extraordinary success? There is none. It just takes an easy-to-assemble vehicle, a thoughtfully laid out plant and an educated, motivated workforce. After that, the age of the factory, whether or not it is unionized, its location, or the degree of automation, become secondary.
It sounds simple, but it's a lesson it took Detroit over a decade to learn.
Ford Atlanta beat - albeit by a small margin - the best North American plants run by Toyota Motor Mfg., North America, Inc., Nissan Motor Mfg. Corp. and Honda of America Mfg. Inc.
What's more, General Motors Corp., long derided as one of the world's least efficient producers, is suddenly making big efficiency leaps as well. Its labor efficiency improved 9% over last year, far more than any other company in the study. "GM has transformed many of its facilities and processes into some of the best in North America," says Ron Harbour, president of Harbour and Associates.
The Chrysler operations of DaimlerChrysler AG now trail Ford and GM in labor productivity, but it retains the highest profit per vehicle. It averaged $1,470 per vehicle, ahead of Honda's $1,440 profit per vehicle. Nissan, for all its productivity prowess, has a history of losing money on the vehicles it builds so efficiently. Last year it lost $17 per vehicle. In 1998 it lost $66 per vehicle.
The once-huge productivity and profit gap between Detroit's best plants and Japan's best is rapidly closing - and in some cases already has closed. A decade ago, it took two workers in a traditional Big Three auto plant to do the work of one in a shiny new "greenfield" plant built by Nissan, Toyota or Honda.
The Big Three had lots of old plants, with old equipment and ways. As the saying goes, it is hard to teach old dogs new tricks. The Japanese came in with lean ideas and equipment and schooled their green workforce in kaizen ways, as opposed to the more difficult task of retraining an existing workforce.
But now, Detroit's best plants can compete with Japan's best on North American turf. Ford, the most efficient domestic manufacturer, captured six of the top 10 truck assembly plant slots in the Harbour ranking and two of the top 10 car assembly plant slots. GM even managed to get two car and two truck plants on top 10 lists.
"We can learn from the Americans at this point," says Daryl Wilson, vice president of manufacturing for Toyota Motor Mfg. Canada, whose Cambridge North plant placed first in last year's study and third this year.
And there's plenty of room left for further improvement. Donald E. Hackworth, GM's senior vice president responsible for manufacturing and the North American Car Group, says GM can continue to make big productivity jumps with measures that do not threaten UAW jobs. It will focus most on trimming non-scheduled overtime: expensive overtime work added to plant schedules when they didn't build what they were supposed to during a regular shift. Typical causes of unscheduled overtime are equipment breakdowns and supplier delivery problems.
If GM could manage to keep all of its assembly lines constantly moving, Mr. Harbour says, it could eliminate the equivalent of 20,000 workers on its balance sheet - without ever actually laying anyone off.
Until the former Big Three make top performers of all their facilities, their Japanese mentors will watch carefully but stay their own proven course.
That is because - Big Three progress aside - it is the manufacturing operations owned by Nissan, Honda and Toyota in the U.S. and Canada, including stamping, powertrain and vehicle assembly, that remain best overall. Collectively, they are still better than Ford, GM or DaimlerChrysler facilities.
That's partly because the Japanese remain the new kids on the North American block, with only a handful of state-of-the-art manufacturing facilities. The American automakers have hundreds of assembly, stamping and powertrain facilities scattered across North America. Among the jewels are troubled plants that continue to drag down their average.
Leading the pack in company average productivity is Nissan Motor Co. with an average 18.7 man hours of labor per vehicle, followed by Honda, New United Motor Mfg. Inc. and Toyota.
But signs that the worm may be turning come from the latest Harbour Report. North American automakers, on an individual plant basis, can lead the field.
The benchmark this year for car assembly is the Taurus/Sable plant in Atlanta. Ford workers in Atlanta have been assembling vehicles for 53 years. They have perfected it so that it now takes only 17.16 hours to assemble each car. That's in spite of the fact that it launched a new model last year. Their colleagues at the Twin Cities (Minnesota) Assembly Plant set the standard for truck production, building Ford Ranger series in 18.97 hours.
As simple as it sounds, the key to Atlanta's efficiency is the ability of the plant to run on schedule and achieve its daily build. That eliminates the need to pay workers a premium to work an overtime shift to complete what should have been done on straight time.
Pains are taken to ensure there isn't a shortage of parts or manpower, or a defect that could force the line to stop.
At the Toyota Corolla/Solara plant in Cambridge, Ont., "the line rarely goes down," says Mr. Wilson.
He credits skilled maintenance workers on each of the two shifts and a conscious effort to get production workers involved in problem solving to ensure continuous production.
At Ford Atlanta, one of the keys to keeping the line running is strong labor-management relations and an absentee rate as low as 2%, which means the job is being done by the trained operator most of the time. The union has been active in keeping workers on the job; stressing the link between attendance and job security.
But Ford's Jim Padilla, group vice president of manufacturing, advises not to focus too much on the role of low absenteeism. "I don't think Atlanta is extraordinary in terms of absenteeism," he says. "The workforce is pretty dedicated, but absenteeism is a fact of life, and we have to learn to manage through that. That means you have to have a very qualified, trained workforce in the event that somebody is not there."
To their credit, GM, Ford and the former Chrysler Corp. have pretty much adopted the old adage that if you can't beat 'em, join 'em. They almost universally acknowledged Toyota's vaunted production system and lean manufacturing techniques as the world's best. They made it their benchmark, signaling that it is good and progressive business practice to study the competition and emulate their winning ways.
Manufacturing terms such as lean, kaizen and andon associated with the Toyota Production System became gospel because of the huge competitive advantage they represented. They also recognized multiple platforms and peculiar body architecture, where every model is different, makes a vehicle expensive to design and more costly to manufacture.
DaimlerChrysler has not fared well in the productivity rankings and recognizes it can reap even more profit by tightening up manufacturing. Harbour calculates DC could save $2.9 billion and would need 23,436 fewer workers if it operated its stamping, powertrain and assembly plants as efficiently as Nissan does.
The company realized, in 1994, that it was trailing the rest of the world in manufacturing efficiency and had to do something, says Gary Henson, DCC executive vice president, manufacturing.
Dennis Pawley, former head of manufacturing for the then-Chrysler Corp., embraced the Toyota system as the basis for the Chrysler Operating System or COS. Mr. Pawley, who has since retired, was its unabated champion. He threw himself into spreading the COS mantra so that it permeated manufacturing from the highest ranks down to the shop floor.
The carmaker continues to tailor Mr. Pawley's original operating system. Today it is called the Joint Activity Operating Principles and a key component is DaimlerChrysler's version of kaizen, which educates the leadership and involves workers in taking waste out of the manufacturing process.
"We realized we had rules and practices, but we had not taught people throughout the organization how to use them," says Mr. Henson.
Two years ago, DCC started pulling workers off the plant floor to participate in the Manufacturing Leadership Training program. There have been more than 55 sessions worldwide where the shop floor is put under a microscope to find ways to eliminate waste and cost, says Mr. Henson.
Savings have averaged $500,000 per session, or $25 million over two years, contributing to the $300-million impact lean production has had on the base cost of manufacturing since 1998, says Mr. Henson.
Another focus is to trim costs during launch. While labor only accounts for 10% of vehicle cost, changes account for 20% to 40% of the cost of a new program, and the automaker is turning over the bulk of its lineup between now and 2005.
To that end, it is investing in equipment and training to make its facilities more flexible. It expects to reap more than $3 billion in savings during product launches alone over the next four years, says Mr. Henson.
The company also is paying more attention to the order in which components are put together, something that must be reflected in both vehicle and plant design.
Investment in equipment and the workforce must go hand-in-hand to achieve world class productivity, says Mr. Henson.
The payback on all these initiatives is better plant layout, higher morale, lower warranty costs and improved customer satisfaction, based on internal audits, says Mr. Henson.
It may not be very exciting stuff, but it works, agrees Toyota of Canada's Mr. Wilson. "There is no silver bullet, no precise thing, just continuous plodding along."
But Toyota's version of "plodding" is carefully mapped and predicated by years of instilling a culture of continuous improvement. "We design the vehicle and the process to be moving the bar up with each generation," says Mr. Wilson. "Once we have the process and vehicle, we mobilize the people." It may sound simple, but "it's not easy to do. It takes a lot of discipline," admits Mr. Wilson.
The Canadian Toyota plant may have slipped from first place to third this time around, but it only missed the top spot by 40 minutes - an indicator of how tight the competition is among the industry's most productive players.
Ironically, productivity improved year-over-year; at 17.56 hours per vehicle, it cut 10 minutes off its winning time. And it occurred during a period of increased production: from under 200,000 to more than 210,000 through overtime and Saturday shifts, as well as preparations to launch the Solara convertible in February of 2000.
The facility will continue to pursue productivity gains as it prepares for a major redesign of the Corolla and assembly of the RX 300, the first Lexus to be built outside Japan.
After a slow start, GM has embraced Toyota-like lean manufacturing with a vengeance. It also has made great progress in designing vehicles that are easier to assemble. Fewer and larger parts mean less assembly required. That means fewer stations on a shorter line manned by fewer workers, who are freed up to do more value-added work.
"We're putting in place our global manufacturing system, and it involves everyone, from the operator on the plant floor to the design and process engineer upstream," says Mr. Hackworth. GM's gains were made by reducing waste and non-scheduled overtime, increasing throughput in its plants and commonizing parts and processes," he says.
GM's push to lean manufacturing "permeates its vehicle designs" says Laurie A. Felax, a Harbour and Associates analyst. "They have picked the low hanging fruit. Now they are starting to differentiate themselves... they're starting to pull away."
So now Ford, GM, and DC all are reaping the benefits of Toyota-style lean manufacturing, but only after wasting years trying to get productive in other ways. For instance, the Big Three spent billions in the 1980s trying to replace workers with robots. It didn't work. The robots turned out to be expensive to maintain and often were unreliable.
"The concept that some thought was the salvation of manufacturing 15 years ago, where you could automate your way through anything, is pretty much debunked," says Ford's Mr. Padilla. "In reality, you need flexibility, and the most flexible assets you have are your people."
The Detroit automakers have made gains in recent years, Mr. Wilson acknowledges, and he says Toyota is monitoring their progress. And while the Americans have closed some of the gaps, Toyota is committed to leading the pack on all key indicators, bolstered by the "strong culture underneath us," says Mr. Wilson. The company's drive to stay on top will keep it from becoming a victim of its own success, he says.
For now, the Toyota plant's benchmarks "continue to be our sister Japanese plants," says Mr. Wilson.
Nissan in Smyrna, TN, isn't standing still, either, adds Harbour's Ms. Felax. She says, in particular, Smyrna is developing new techniques to have suppliers deliver their parts in sequence with its assembly line. While it's commonplace for seats and instrument panels to be delivered this way, Nissan is expanding the concept to steering wheels, door trim panels, radiators and other parts. "They're doing everything they can, and they're making substantial improvements in their own process," she says.
"It's easy to fall in love with your own success," says Mr. Wilson of Toyota. "The danger is to get too proud and think you're invincible." That, of course, is the mistake Detroit automakers made 20 years ago.
Read more about:
2000About the Author
You May Also Like