Air bags brace for impact; producers develop greener alternatives to sodium azide
If you think the only impact air bag producers care about is in a crash, think again. Concerns over the environmental impact of junked air bags is forcing them to redesign their products and search for more ecofriendly pyrotechnic materials to inflate the bags.This is no public relations exercise, either. Automakers are demanding more environmentally friendly air bags, and the installation rate of
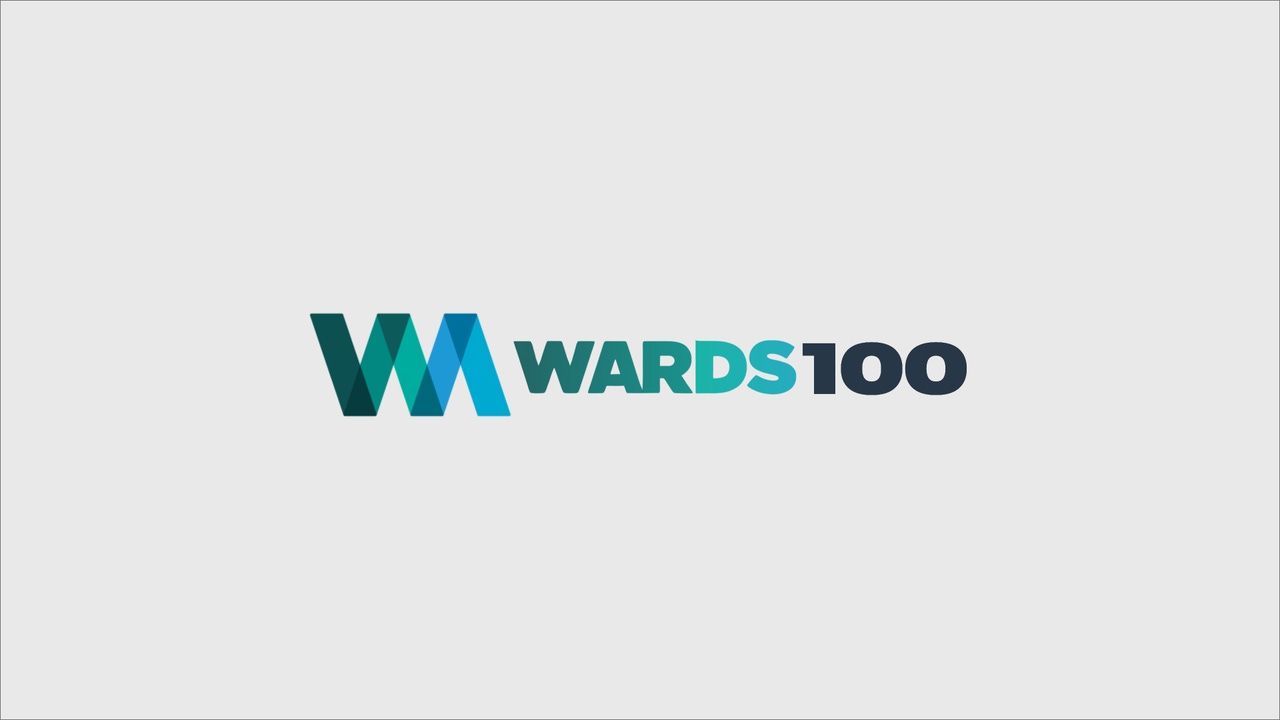
If you think the only impact air bag producers care about is in a crash, think again. Concerns over the environmental impact of junked air bags is forcing them to redesign their products and search for more ecofriendly pyrotechnic materials to inflate the bags.
This is no public relations exercise, either. Automakers are demanding more environmentally friendly air bags, and the installation rate of new systems is expected to soar by the late '90s.
It shouldn't be that much of surprise. Dual air bags will be standard equipment on almost all cars and trucks sold in the U.S. by then, and some will also feature side- and possibly rear-seat air bags as well. Considering that about 10 million vehicles are scrapped every year, the environmental implications are enormous.
Automakers and suppliers already have logged significant progress in making systems more recyclable. Materials used in air bag doors and the bags themselves are being altered for reuse, and steel and aluminum structures from scrapped units already are being recycled.
Morton International Inc., TRW Inc., Takata Inc., Breed Technologies Inc. and others say they are developing design for disassembly (DFD) strategies with automakers to properly identify and limit the number of plastics and other materials used in new designs.
But the main concern is dealing with the sodium azide propellant. When sodium azide "burns" (explodes) it generates harmless nitrogen gas that inflates the air bag in less than a blink of an eye. But in its solid state it is considered a toxic material with health risks; it can affect blood pressure and might possibly cause cancer if it's somehow ingested.
If many air bags are accidentally shredded at one site during the vehicle recycling process, it's feared the dust eventually could become a health hazard.
Recyclers currently handle the sodium azide problem by deploying the bags at the scrap yard prior to shredding, or removing the air bag modules and selling them as replacement parts - both imperfect solutions. Scrap yard operators don't like the inherent danger of constantly deploying the bags, and salvaging intact air bag modules for use as repair parts makes OEMS and suppliers very nervous about possible product liability.
Two solutions are in the works: Morton, TRW and other air bag system suppliers are introducing greener "azide-free" inflators, but more easily recyclable sodium azide systems also are being developed.
Last February, TRW's Occupant Restraint Systems Group introduced a heated gas inflator (HGI) that uses a mixture of hydrogen and air and a miniature scuba tank-style bottle. HGI reduces cost by up to 20% and weighs up to 40% less, and it sets new standards for environmental cleanliness, says TRW.
"From an environmental perspective, the heated gas inflator is a major breakthrough," says James F. Smith, vice president and general manager - inflatable restraint systems. TRW already has received a contract for use in the front passenger air bag on a '98 North American vehicle. He predicts that by 2003, 25% to 45% of air bags could use HGI technology.
Morton also has a non-azide inflator, which is expected to be available next year. But Jim Erickson, Morton's manager-advanced development programs, points out that developing nonazide inflators hasn't been easy.
A variety of pyrotechnic materials can be used to inflate bags, but 99% produce toxic byproducts when burning or are otherwise unsuitable. Many don't burn as predictably as azide, others smoke too much, don't age well, or produce a haze that initates the eyes or throat after deploying. Still others are affected by temperature swings, or make too much noise when they explode.
"It wasn't happenstance" that azide was picked as the propellant for most inflators, Mr. Erickson says. Even though alternatives have been developed, the search for better propellants and inflators continues.
But don't count azide out yet. ICI Explosives recently announced a new blending process for its "Microsaf" sodium azide propellant, which it says produces a recyclable, environmentally friendly material.
With the new process, the sodium azide particle size is much smaller and offers numerous advantages such as faster, more tailorable bum rates and less smoke. It also makes the material much easier to handle and recycle. And it's possible to retrieve the material from undeployed inflators for re-use, without the need to "chemically or combustibly destroy" it, ICI says.
About the Author
You May Also Like