Manufacturers Get Digital – Or Say They DoManufacturers Get Digital – Or Say They Do
“Digital manufacturing is still in its early days,” McKinsey’s Richard Kelly says. Automakers “are putting a lot of effort and energy in it…But they don’t have a firsthand view of what other players are doing. Therefore, it’s a little hard to judge if you are ahead or behind.”
September 25, 2018
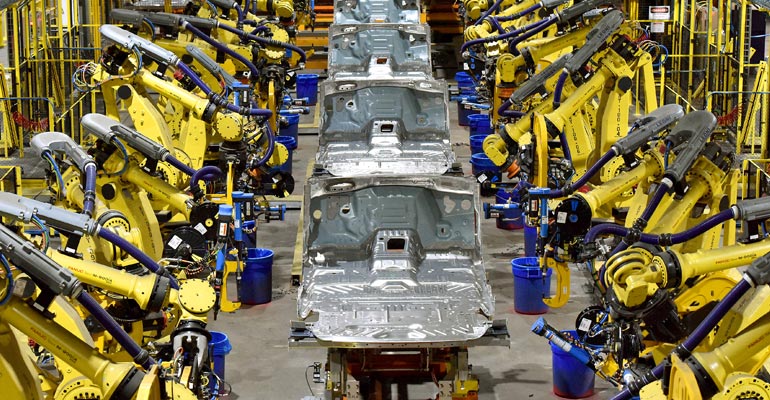
Every automaker and Tier 1 supplier surveyed in seven countries rates itself at least at par with the competition in digital manufacturing, according to a recent white paper by consultancy McKinsey.
Is this hubris talking?
Not at all, says Richard Kelly, a McKinsey partner and an author of the 2018 Manufacturing Global Expert Survey.
“Digital manufacturing is still in its early days,” Kelly tells WardsAuto. “(Automakers) know they are putting a lot of effort and energy in it. It’s a big focus for them. They are seeing some good progress. But they don’t have a firsthand view of what other players are doing. Therefore, it’s a little hard to judge if you are ahead or behind.”
Kelly rates automotive in the middle of the pack in key pursuits of Industry 4.0:
• Connectivity – Using digital performance management and augmented reality to move the right information to the right people in real time. These tactics help communicate interactive work instructions and standard operating procedures.
• Intelligence – Making better decisions through advanced analytics and artificial intelligence. This includes predictive maintenance, digital quality management and artificial intelligence-driven demand forecasting.
• Flexible Automation – Safer robotic technologies include interactive “cobots” that work alongside humans. Cobots have become a common sight in many auto plants.
“They are comfortable with (automation),” Kelly says. Companies know their robots generate huge amounts of data. “You’re seeing companies implementing predictive maintenance use cases, detecting micro-level deviation and using that as a predictor of reliability.”
He says integrating systems to create a real-time, data-driven view of performance for predictive analytics, and replacing a firefighting culture that relies on instinct and expertise are two barriers that must fall.
Automakers trail some industries in use of analytics and digital quality management. “There are lots of opportunities for paint quality or other kinds of quality management,” Kelly says.
The survey of 50 automakers and suppliers finds:
• 92% of OEMs have tried analytics for quality management and root cause analytics. Just 31% had rolled it out.
• 54% have 3D printing pilots but just 4% run at scale. Adoption among suppliers is 25%.
• 54% had tried augmented reality for operator guidance or training, but just 15% had taken it to scale. For suppliers, 63% had tried it and 8% had it in full use.
Like lean manufacturing in the 1980s, Industry 4.0 is subject to ever-maturing technology.
The New United Motor Manufacturing joint venture between Toyota and General Motors was among the first lean production experiments in 1984. It took years for GM to copy and implement its version of the Toyota Production System.
“This is a journey in the same way the other industrial revolutions have evolved,” Kelly says. “There isn’t a mature best practice for capturing the value from digital manufacturing. Technologies are constantly evolving. We have a long path ahead of us.”
About the Author
You May Also Like