Materials
Nutrition experts say the best diets reduce weight very gradually, over a long period. Automakers in North America apparently have been listening. They're expected to reduce the total vehicle weight of cars and trucks by only 10% by 2009. So no matter how many super light-weight, all-aluminum and all-plastic concept vehicles you see on the auto show circuit this year, don't expect to see a lot on
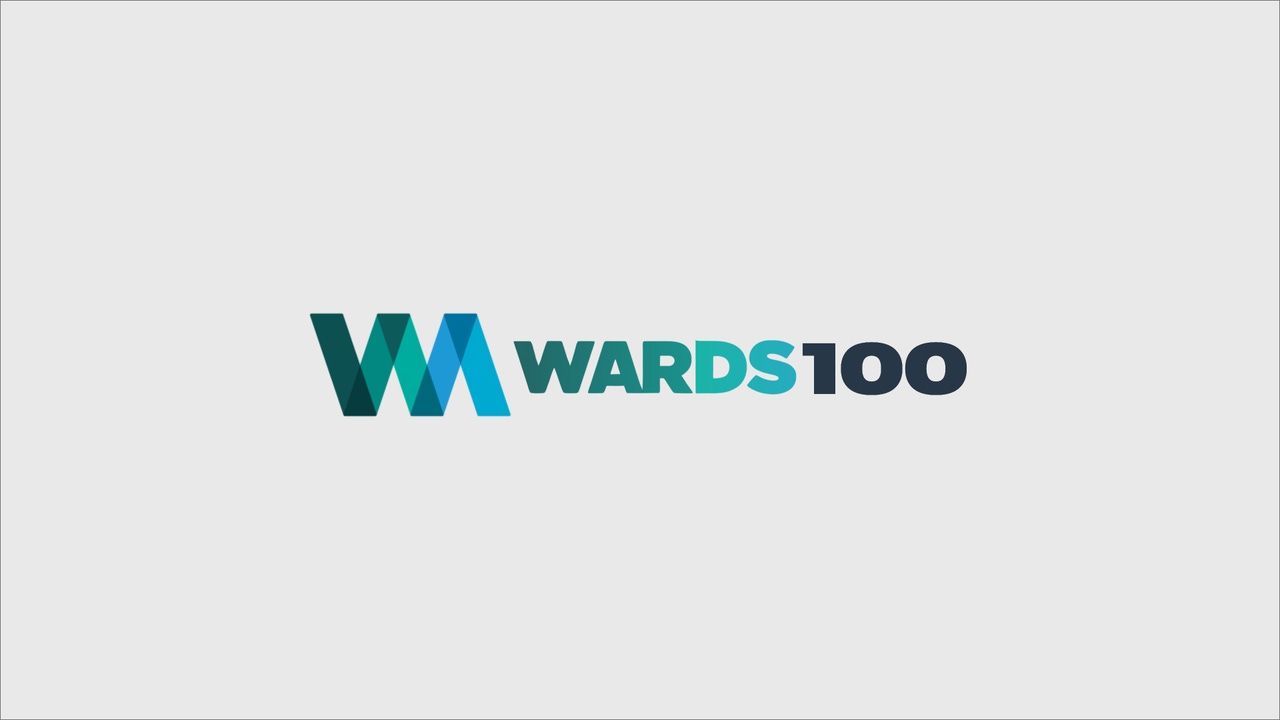
Nutrition experts say the best diets reduce weight very gradually, over a long period.
Automakers in North America apparently have been listening. They're expected to reduce the total vehicle weight of cars and trucks by only 10% by 2009. So no matter how many super light-weight, all-aluminum and all-plastic concept vehicles you see on the auto show circuit this year, don't expect to see a lot on the road anytime soon.
At least that's the conclusion of the University of Michigan's widely followed Delphi Study on automotive materials. The report is based on detailed responses from more than 200 auto industry experts in the 10th biennial U of M Delphi Forecast and Analysis of the North American Industry.
The report's conclusions may be disappointing to environmentalists and producers of lightweight materials, but they jibe with other fairly recent independent research (see WAW — Nov. '99, p.77).
The culprit, of course, is cost. Lightweight materials are generally more expensive than heavier conventional materials, such as steel and cast iron.
“It is very clear that the cost of materials and processing is the most important material-selection decision criterion,” says Brett C. Smith, who conducted the study for the U of M Office for the Study of Automotive Transportation. “Given several years of severe price competition, it is not surprising that cost reduction has been placed at the forefront of vehicle manufacturer purchasing strategy.”
Mr. Smith's comments were reinforced last month when both the Chrysler Group and General Motors Corp. announced aggressive new material cost reduction strategies in an effort to blunt the effects of sinking profits.
According to the study, total vehicle weight is forecast to decrease 10% for both passenger cars and trucks by 2009, mainly as a result of expected increases in Corporate Average Fuel Economy (CAFE) requirements. The weight reduction will be achieved through greater use of aluminum and plastics and less use of low-carbon steel and cast iron, but — contrary to some of the propaganda — the new lightweight materials will be used as sparingly as possible.
“Raw material cost is the most critical barrier to increased aluminum application,” says report coauthor Michael DiBernardo. “Interestingly, the metal's price volatility may be almost as disconcerting to automotive engineers as its relatively high price. In many instances, a vehicle manufacturer can justify the higher cost of aluminum, given its many positive attributes. Yet the fear of unstable prices may still make it difficult for an engineer making the material selection to specify aluminum.”
Formability issues, the challenge of joining and bonding aluminum and its compatibility with current assembly facilities are other barriers to greater use of the light metal, the researchers say.
Despite its liabilities, aluminum is forecast to see increased use for car hoods (22.5%), decklids (17.5%), truck hoods (30%) and rear hatches (17.5%) by the end of the decade. Furthermore, plastics are predicted to see increased use for car fenders (15%) and doors (10%) as well as truckbed applications (20%).
Meanwhile, the Delphi respondents predicted that steel will continue to be the dominant material in frame construction, body panels and chassis components for the next decade, although aluminum is expected to be used more often as frame material (15%) and space frame material (20%) by 2009.
Aluminum also is predicted to continue to replace cast iron and steel in many engine applications such as cylinder heads and engine blocks, the study's authors say.
While a 10% weight reduction over the next nine years may sound like a weak effort, it should be pointed out that despite the hype over the use of lightweight alternative materials such as aluminum, magnesium and advanced composites, cars and trucks got steadily heavier throughout most of the 1990s.
In 1990, family vehicles were the lightest they've been in recent history. By then, automakers had managed to chop almost 1,000 lbs. (454 kg) from the weight of a typical 1970s era family sedan; not by using lighter materials, but by downsizing and learning how to make more efficient steel body structures.
Steel industry sources say the switch from old-fashioned body-on-frame designs to lighter, more efficient unibody structures during the 1980s culled more weight — and more steel — from vehicles than all the aluminum, plastics and magnesium combined.
But since 1990, vehicles have been putting weight back on as consumers have gravitated toward bigger cars and trucks and more weighty options such as four-wheel-drive. The quest for stronger, stiffer body structures and more safety and electronics equipment also has added weight.
Yet despite rising gas prices, consumers have not shown a willingness to move back into smaller vehicles. That virtually eliminates the fastest, most cost-efficient means of reducing weight — downsizing — and leaves light material use as the much more difficult and expensive alternative.
About the Author
You May Also Like