Materials: Demand Drives Plastics InnovationMaterials: Demand Drives Plastics Innovation
The mother of invention is necessity. And what automakers need these days are lightweight, environmentally friendly, durable, inexpensive parts to make their cars and trucks.It's a relatively strict list of parameters for originality. And it continues to grow. They are standards that might stop some industries or would-be inventors in their tracks, or at least slow down the pace to near stagnation.But
December 1, 1999
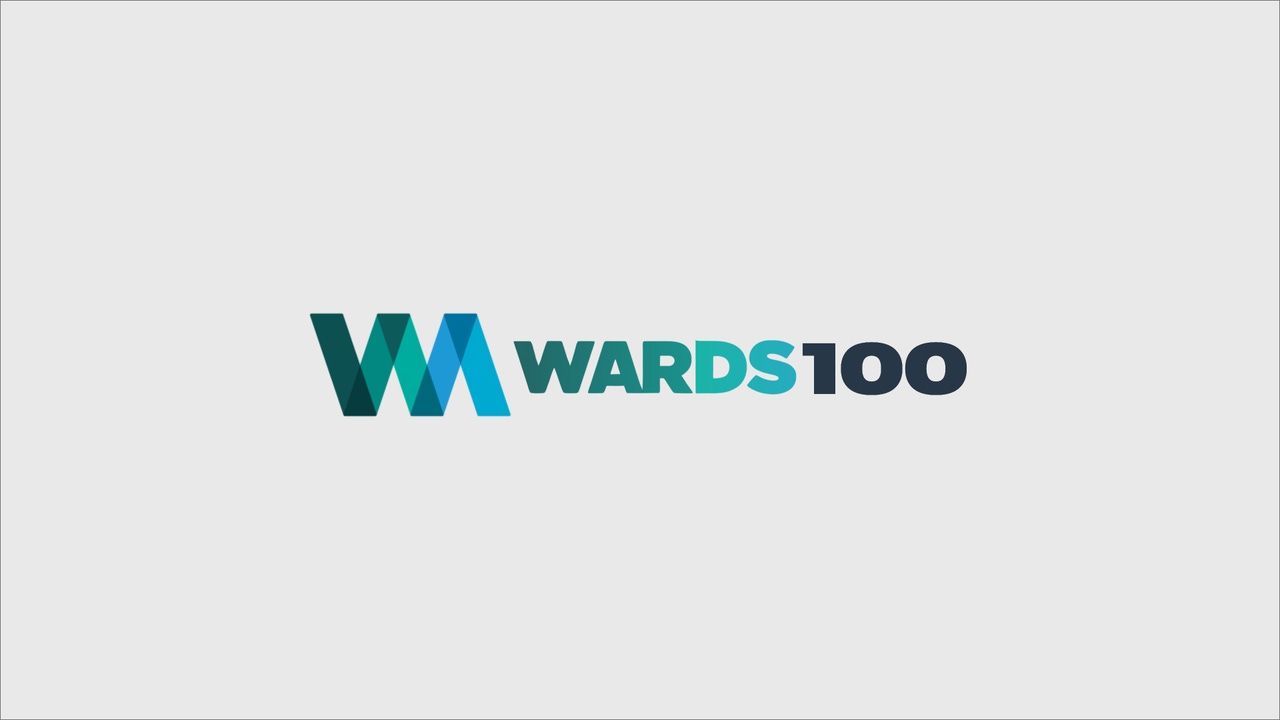
The mother of invention is necessity. And what automakers need these days are lightweight, environmentally friendly, durable, inexpensive parts to make their cars and trucks.
It's a relatively strict list of parameters for originality. And it continues to grow. They are standards that might stop some industries or would-be inventors in their tracks, or at least slow down the pace to near stagnation.
But the Society of Plastics Engineers year in and year out have no shortage of nominees for its annual awards for innovative use of plastics in the automotive industry.
And 1999 was no different. In fact, if it was different, that's because by all accounts it was one of the most stellar years in recent memory.
Instead of being a detriment, automakers' stringent demands actually are giving engineers the impetus to attack nearly every aspect and angle of an automobile that, as recently as the early '90s, would have been considered off limits to plastics.
Here's a brief rundown of this year's winners:
The folks who designed the RITec Fan Shroud Reservoir should have been competing against David Copperfield instead of other engineers. How else but by magic would you explain integrating five components into one?
But that's what DaimlerChrysler Corp. and McCord Winn Textron accomplished with the RITec - Reservoir Integration Technology, which won the process and enabling technologies category and the SPE's Grand Award.
DC was redesigning the cooling system for the '00 model year Dodge Dakota and Durango. The automaker asked for the development of an integrated shroud for the coolant reservoir, rear and front washer reservoir, fan shroud and rear filler assembly.
And McCord Winn Textron answered in a big way. RITec reduced labor time as well as mass - by 1.1 lbs. (0.5 kg). Shipping costs were cut and a number of fasteners were removed. With the coolant and washer reservoirs moved to the front of the vehicle, service access was enhanced. The receptacles' fluid capacity was increased to 1 gal. (3.9L), "so that you're not left with that annoying little amount at the bottom of the bottle that everyone hates," says an engineer involved in RITec's creation.
The development was swift, too, going from concept to production in two years. McCord Winn Textron used deep draw blow molding to make the complex fan shroud - a first in the automotive industry.
Other winners were:
* Powertrain: The sophisticated KV6 2L/2.5L intake manifold made by Rover and Mann+Hummel once again shows plastics is growing as a viable option for engine applications. Switching from aluminum to glass-reinforced nylon 66 resulted in a weight reduction of 50%. There also was a 30% cost savings due to the multiple molding and material technologies along with new assembly processes.
It is the first such component to use plastic flaps and a patented overmolding process to lessen complexity while delivering significantly more power and torque. Powertrain was one of the stronger categories in this year's awards. Judges also highly compli-mented the GM premium V-8 ignition cassette and the Dodge Neon 2L thermoplastic throttle body.
* Chassis: With North American design and manufacturing moving more toward front-end modules, the grille opening reinforcement used on the Ford Focus deservedly snagged the top spot in the chassis division. Body-In-White is a new arena for thermoplastics. And with its impressive characteristics and results, the material likely will be considered for a series of applications. Visteon Automotive Systems - using Bayer Corp. technology - designed GOR. The component is 100% recyclable and delivers a weight savings of 40%, while cutting costs 30%. The compressive, torsional and flexural strengths of the plastic/metal hybrid exceed 1.8 times that of conventional metal designs.
* Body Interior: Where else would the flashiest instrument panel be other than a Pontiac? The full soft thermoplastic polyolefin (TPO) instrument panel, offered on the '00 Bonneville and developed by Delphi Automotive Systems, is the first of its kind in North America and the only one in the world with an air bag-deployable top pad.
TPO is a material made by combining rubber with polypropylene, a petroleum by-product. Besides being 100% recyclable, TPO provides seamless "hidden air bag" doors, a soft leather-like feel, and it eliminates window fogging. Another major development on the Bonneville application is Delphi's use of a unique water-based coating system that overcame the challenge of offering deep draw capability with soft TPO skin.
* Environment: Used tires present serious environmental and health risks, but the junk piles may begin shrinking if more uses for Symar-T are found. Developed by NRI Industries Inc. and used for three seals on DaimlerChrysler Corp.'s Jeep Grand Cherokee, Symar-T is a hybrid plastic rubber made of 70% recyclable content.
The tire-derived material contributes to the recovery of 15 million tires annually. "So that's 200 million lbs. (91,000 t) of rubber, 97 million lbs. (44,000 t) of steel and 22 million lbs. (10,000 t) of fiber that are avoiding landfills each year," says Mark DeAngelis, product engineer, Jeep cooling systems.
Impressive. And just a start. NRI is looking into using Symar-T for other applications, including body molding and wheel well interiors.
* Body Exterior: A tough decision here. But the MCC Smart car MIC body panels with clearcoat won out. Talk about customizing, the creation by GE Plastics represents the first interchangeable molded-in-color plastic body panel. Smart drivers can swap body panels with each other or buy a new set for $800. Weight also was reduced from the previous body panels.
* Materials: Dupont Automotive's Surlyn Reflection Series resin enables Daim-lerChrysler's '00 Neon to have a nearly perfect fascia. Injection molded, the fascias feature a high gloss, scratch resistance and a body color match. Dupont and DCC worked together with A. Schulman (color development) and Build-A-Mold (tooling).
Read more about:
1999About the Author
You May Also Like