More Than Skin Deep-New IP covers represent big technological strides
Just what makes an attractive, high-quality instrument panel? Ask designers and you'll get one set of answers, ask engineers and you'll get another. Consumers will give you still different opinions.What's more, a recent study by the ITB Group Ltd., an international consulting company, shows that automakers in Europe, Japan and the U.S. don't even agree on the importance of basic instrument panel styling
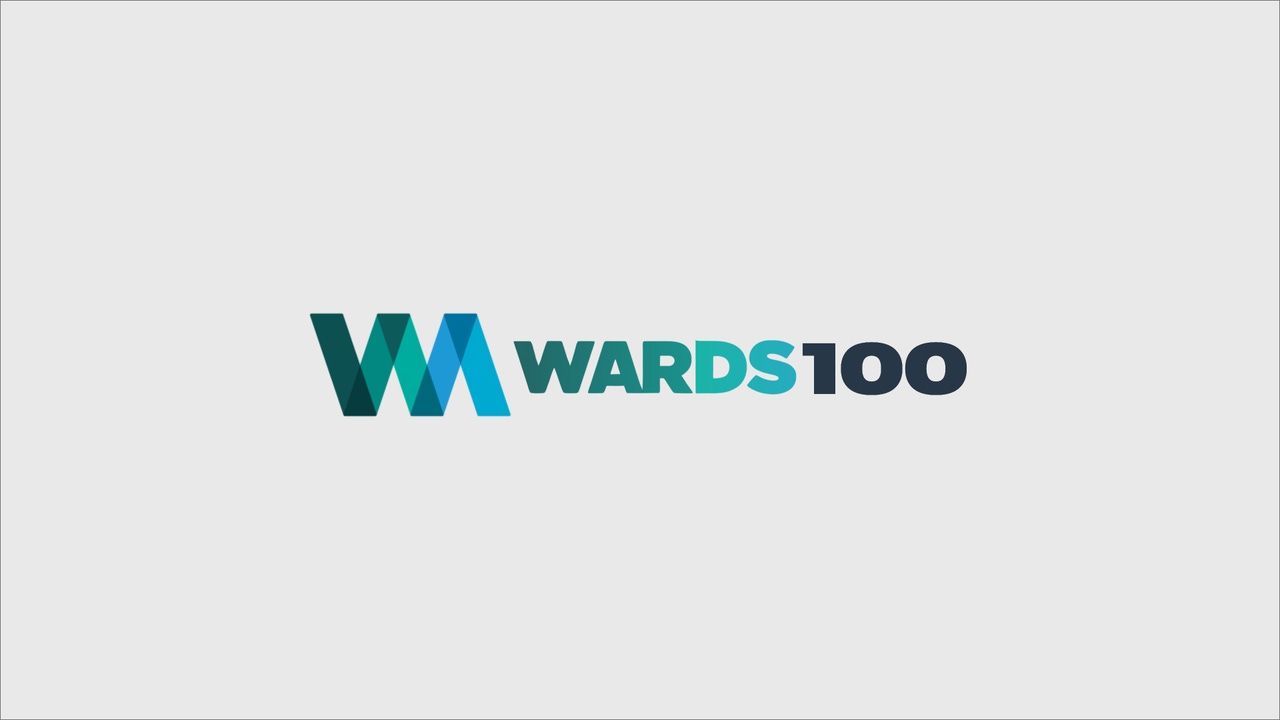
Just what makes an attractive, high-quality instrument panel? Ask designers and you'll get one set of answers, ask engineers and you'll get another. Consumers will give you still different opinions.
What's more, a recent study by the ITB Group Ltd., an international consulting company, shows that automakers in Europe, Japan and the U.S. don't even agree on the importance of basic instrument panel styling trends and concepts such as providing "a feeling of space and harmony," having very low gloss interior surfaces and eliminating air bag door seams.
ITB says seamless air bag doors are a "definitive trend" in Europe, but only a "small trend" in the U.S.
Likewise, having surfaces with "gloss close to zero" seems to only be a top priority in North America.
While designers and consumers worry about gloss levels and textures, engineers have to make sure the plastic won't splinter at -401/2F when the air bag goes off - and worry about what recycling rules there will be in 2009.
Two recent finalists in the Society of Plastics Engineers awards for most innovative use of plastics - both from DaimlerChrysler - are examples of how beauty runs far more than skin deep.
Not only do these IP skins pass the leather-look test with flying colors, they both are on the cutting edge in materials and processing technology. Both technologies enable designers to hide air bag door seams if they wish, and are much more environmentally friendly to boot. Improving recyclability and eliminating chlorine from materials are becoming high priority issues among all automakers as they move to global vehicle platforms that must comply with myriad environmental regulations throughout the world, many of which are tougher than U.S. standards.
"Nobody wants to do multiple validations for the use of one material in the U.S. and another in Europe," says James A. Obermeyer, engineering manager at Delphi Automotive Systems. Delphi developed the new Mercedes M-Class IP skin in partnership with Mercedes-Benz and Mytex Polymers, a partnership between Exxon Chemical and Mitsubishi Chemical Corp.
Textron Automotive and Bayer Corp. developed the IP skin on the 1999 Chrysler Concorde/LHS/300M after eight years of research. Called Texin DP7-3014, it is an entirely new type of thermoplastic material that required the design and construction of a new polymerization plant as well as the invention, design and installation of special processing technologies that resulted in a number of new patents.
It is generically known as a cast-moldable aliphatic thermoplastic polyurethane, and it features a chemistry that sets it apart from all other thermoset and thermoplastic polyurethane plastics, which feature a more traditional chemistry called aromatic. The result is a very soft, luxuriously textured material that is 15% lighter than traditional vinyl and far more resistant to the ravages of heat and sunlight.
Unlike vinyl, chlorine is not used in the manufacture of Texin. That makes it easier to recycle and far more attractive to environmentalists, who consider chlorine a serious environmental threat - especially in Europe.
Meeting European environmental goals also is one of the drivers behind replacing the IP skin material on Mercedes' M-Class sport/utility vehicle assembled in Vance, AL. The new thermoplastic olefin material is being used for IPs on right-hand-drive export versions of the vehicle and will be gradually phased in on left-hand-drive versions during the 1999 model year.
Delphi's Mr. Obermeyer says the new TPO material does have a "richer, softer feel" than the current vinyl, but it also is substantially more resistant to cracking and embrittlement - even after decades worth of sunlight exposure. Other benefits include better color stability and cold-temperature impact properties. Replacing the vinyl with the TPO alsodidn't require major process changes, Mr. Obermeyer says. He declines to give de tails, but he says Delphi has several more TPO IP skin programs in the works.
Ron Price, marketing manager of Polymers at Exxon Chemical's Automotive Business Unit, adds that using a thermoplastic olefin skin is an important first step in the development of a future "monomaterial" IP. That module includes a skin, plastic foam underlayer and IP structure all using the same plastic chemistry. That greatly enhances recyclability compared with most of today's IPs, which are a mishmash of several different plastics and metals. And developing IPs that are more recyclable seems to be at least one issue that designers, engineers and consumers - from all countries - want to do.
About the Author
You May Also Like