Shooting Blanks
Shooting Blanks Aerospace company advances aluminum welding technology A Canadian engineering firm is adopting a unique strategy in the war to reduce vehicle weight.It's shooting blanks.Liburdi Engineering, a Toronto-area company with a high-flying reputation in aerospace, is on the radar screen of at least five automakers because of its welded aluminum blanks.Now a staple of the steel industry, so-called
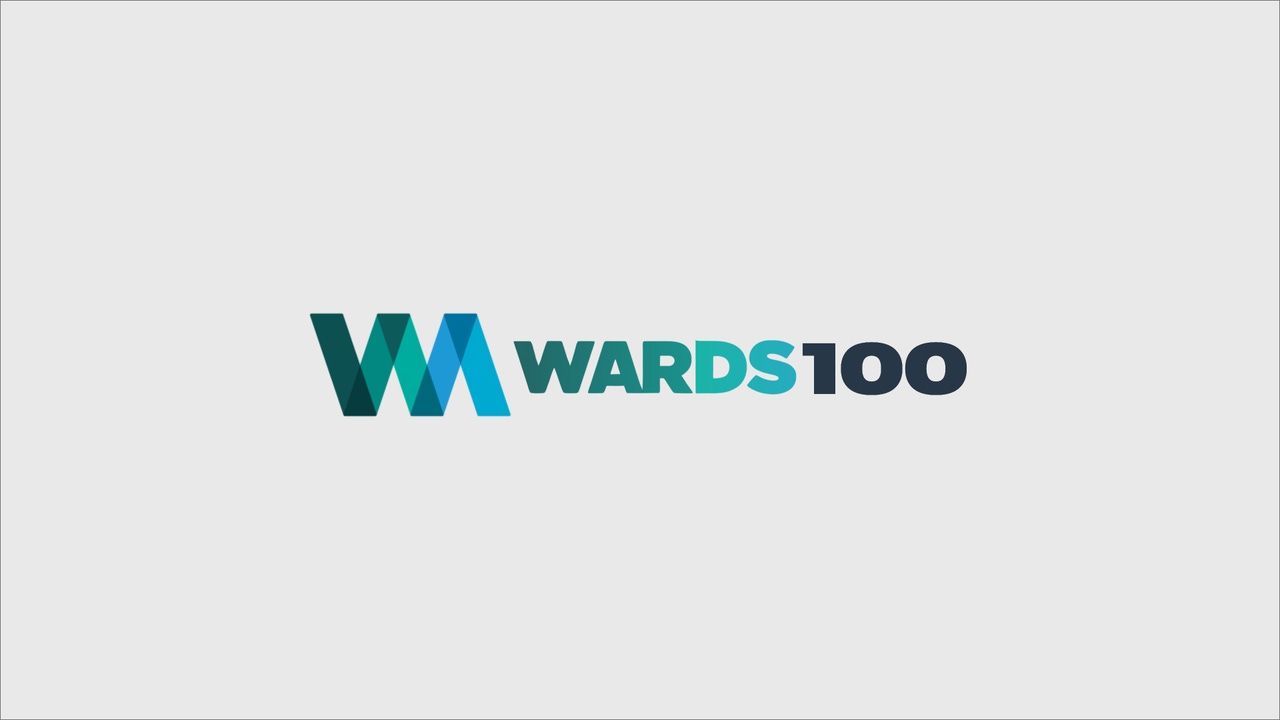
Shooting Blanks Aerospace company advances aluminum welding technology A Canadian engineering firm is adopting a unique strategy in the war to reduce vehicle weight.
It's shooting blanks.
Liburdi Engineering, a Toronto-area company with a high-flying reputation in aerospace, is on the radar screen of at least five automakers because of its welded aluminum blanks.
Now a staple of the steel industry, so-called tailor-welded blanks aren't new.
"They are very well-established on the steel side," says Liburdi president Joe Liburdi.
The metallic version of a patchwork quilt, welded blanks consist of thicker sections welded to lighter, thinner ones. Where strength is critical, such as the union of hinge and door panel, the thick sections are used. Thinner pieces of metal are used where strength is less important. The variation not only reduces waste, it trims weight.
"Now some of the people want to move to aluminum (welded blanks) for further weight reductions," Mr. Liburdi says. "And when you move from steel to aluminum you inherit a whole series of welding problems.
"One of the big things with aluminum is it has a very good oxide. That's how it keeps from rusting." But, he adds, the valuable compound also inhibits formation of a reliable weld.
"People have been looking for a solution to do the aluminum blanks. The laser people have tried to put two lasers together instead of one so that one beam kind of conditions the other one - which is kind of cumbersome and still doesn't do that good a job as far as we can see."
Detroit is experimenting with an Israeli process that marries laser technology with a plasma torch. But Mr. Liburdi remains unimpressed.
Little wonder. In aerospace, his engineers already are big-time operators.
How do they do it? By reversing the charges.
When traditional gas-metal arc welding is employed, current flows just one way, says John Micheli, a metallurgical engineer with Liburdi Pulsweld, a Liburdi Engineering subsidiary.
But reversing the polarity to facilitate two-way current "cleans" oxide from aluminum, making it weld-ready.
Says Mr. Liburdi: "When we weld aluminum on the aerospace side, we use this very low-polarity plasma technology that basically combines cleaning and welding in alternating cycles. It's not like alternating current. It's what we call `square wave.' And we do it in a very controlled fashion."
This innovation, for which a patent is pending, is called VPPAW - for "variable polarity plasma arc welding." And it has led to involvement in the U.S. space program.
"We provided the welding system for Boeing for the Delta IV rocket just a couple of years ago," Mr. Liburdi says. "So we basically put the same technology that we used for that program and demonstrated that we could weld these aluminum sheets without any great problem."
With the help of Detroit-based stamping house Noble Metal Processing, Pulsweld - which has offices in Detroit, Los Angeles, Amsterdam and suburban Toronto - began pumping out prototypes while Mr. Micheli pounded the pavement.
Although not as aggressive as some European and Japanese automakers, the U.S. Big Three automakers have done extensive work with aluminum-intensive vehicles, from Ford Motor Co.'s P2000 high-mileage concept car and the fenders on the Lincoln LS to the Chrysler Prowler low-volume niche car.
General Motors of Canada Ltd. already is building vehicles with aluminum engine cradles assembled with Liburdi technology. Meanwhile, GM also is exploring the use of welded aluminum blanks.
Pulsweld also has had direct and indirect negotiations with Volkswagen AG and a Japanese automaker it declines to identify.
Aluminum parts on the industry's drawing board include liftgates, heat exchangers and fuel-delivery components.
The material's higher price tag can be offset at the consumer's end through fuel economy, Mr. Micheli adds. And forget any concerns about strength - VPPAW leaves a joint that is 95% as durable as parent material.
Cars such as Audi's aluminum-bodied A8 and A2, as well as Morgan's redesigned Aero 8, the Chrysler Prowler and older cars such as the Acura NSX are proof the lightweight metal works for series-produced vehicles. But why did it take so long to notice a process that has been in use for nearly 10 years as an aerospace application?
Mr. Liburdi gives automakers a wide berth.
"It just wasn't something that people in the automotive side were familiar with," he says.
Does Mr. Liburdi foresee other bends in the road?
"One of the other things that they're looking at is the next-generation frame where they want to use aluminum tubes welded together. And then you hydroform that whole thing - after you weld it."
This is accomplished using orbital welding apparatus, which also would allow an automaker to set up a space-saving assembly line where frames travel on a vertical axis.
Then Mr. Liburdi reveals a trend that should warm the hearts of automotive industry suppliers around the world.
"What's happening is that people are inviting us more at the design stage. They're asking, `How do you want this thing designed from the fabrication point of view?'"
If you're a supplier, we know what you're thinking: It's about blankety-blank time.
About the Author
You May Also Like