Bentley’s Assembly Plant Hums With Addition of Mulsanne
Twenty-first century automation combines with Bentley’s old-world hand craftsmanship to build bodies for the new flagship.
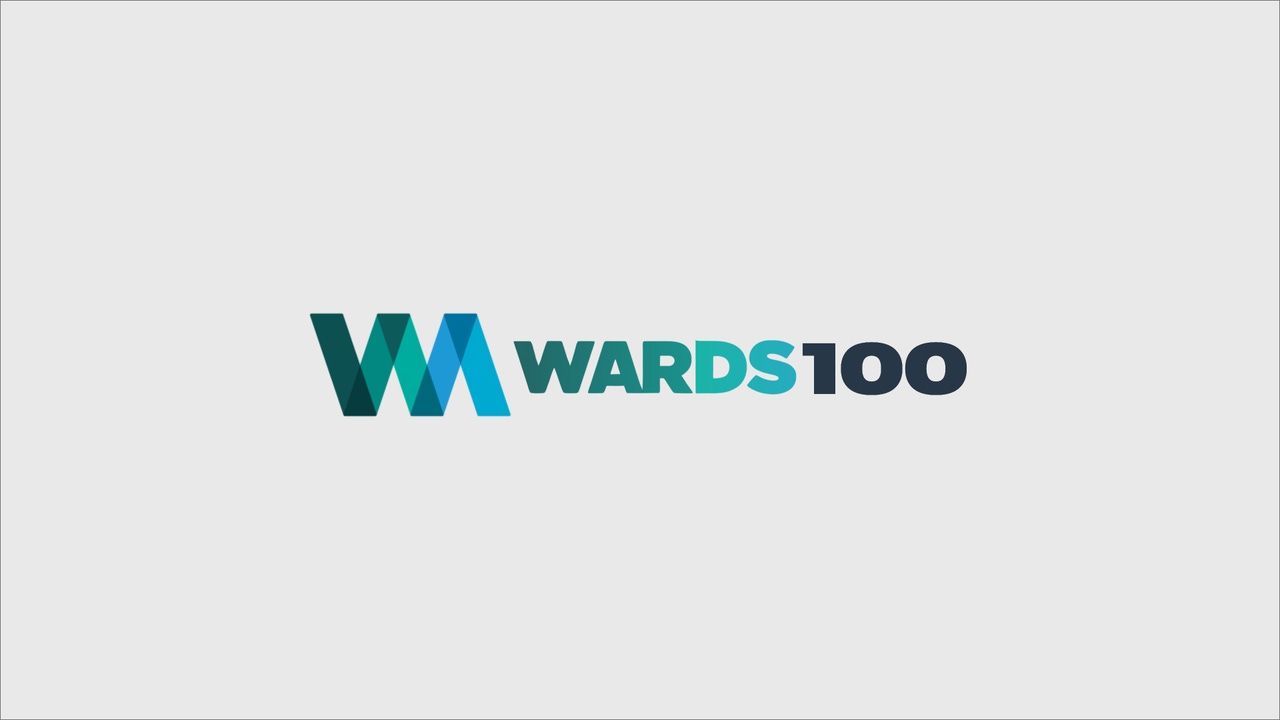
CREWE, U.K. – Crewe is humming once again.
After drawing back production last year as sales tumbled 39% worldwide and 49% in the U.S., its most-important market, the lone assembly plant for Bentley Motors Ltd. is back at capacity.
However, capacity for this iconic coach-building operation some 169 miles (272 km) north of London means four days of production per week.
Bentley reserves the fifth day for maintenance and public tours. But during the more than 37 hours of operation, its green-shirted workers build some 25 units off the Continental line and expect a maximum of 20 on the newly tooled Mulsanne line.
“Whether we will make 20 might be difficult,” says Nigel Lofkin, a former sheet-metal trimmer turned tour guide for the Bentley Experience.
The Bentley Experience takes long-time and would-be owners on a tour of the 72-year-old facility, with stops at all five points – the historic Lineage Room, the main build hall, body shop, wood-working shop and engine room.
On this day, Lofkin leads a group of American and Canadian journalists down Pyms Lane as background for the Mulsanne sedan, which launches worldwide later this year.
It is the first “Big Bentley” in 80 years, and no expense was spared in development for the $285,000 luxury liner, including a new €27.5 million ($34.7 million) dedicated body shop.
The plant receives bodies for the Continental from offsite. But Lofkin says, to make a true Bentley, the auto maker’s corporate decision makers thought Mulsanne bodies should be made onsite.
Meticulous craftsmen make Bentley body beautiful.
Construction of the 7,500 sq.-m (80,730 sq.-ft.) body shop was begun March 2008 and completed May 2009. Inside, 21st century automation combines with Bentley’s old-world hand craftsmanship to build bodies for the flagship Mulsanne.
To create the muscle-bound front wings of the Mulsanne, for example, Bentley borrows from the aerospace industry an advanced technique called superforming. In superforming the Mulsanne wings, a sheet of aluminum is heated to 932° F (500° C) and forced into shape with air pressure.
“Common presses could never make the lines that create the strong, powerful shape of the wings,” Lofkin explains.
The process delivers weight-savings, too, which allows Bentley to add more wood, more leather and deeper-pile carpet to the Mulsanne. For comparison, the Mulsanne will use between 17 and 18 full hides, while a Continental 2-door coupe consumes 11-12 hides.
Contrasting against high-tech superforming for the front wings, craftsmen shape the seamless sweep of the rear wing, as well as the roof and trunk. Workers clad in white jumpsuits hand-braze the seams, stopping occasionally to pencil in guide lines.
The larger body shop process, which entails some 5,800 spot welds, is assisted by 11 robots. Nonetheless, 154 manual welders also take part in the process. Robots perform hemming to achieve perfectly paper-thin gaps for the Mulsanne.
However, some elements of the process are performed offsite. As a niche player, Bentley cannot afford its own press line, so components such as the floor and some door pieces come from German steel-company Salzgitter AG.
Body-shop tooling, an order originally costing €15 million ($19 million) and growing incrementally by the week, comes from Italian supplier Comau SpA.
About 35 bodies are completed per week, consuming roughly 125 man hours. Each undergoes examination in a room outfitted with hundreds of high-powered lights before heading to the main build hall for general assembly.
And each week, quality-control engineers pull a body off to their own examination room outfitted with more powerful lights to scrutinize for the slightest imperfection.
In the leather room, Bentley creates a “Center of Excellence” for the Mulsanne. That means workers handling the leather each have at least five years of experience, as well as special off-the-job training.
Again, the attention to detail is meticulous. For example, inspectors spend an average of three hours studying the hides bound for a single car. An automated cutter then scans the hides for imperfections a second time before cutting out 390 pieces for one Mulsanne – 30% more than the Arnage it replaces.
A third inspection of the leather occurs at its application.
At the steering-wheel station in the main build hall, it takes five hours to wrap a wheel. Perhaps no job more reflects the uniqueness of Crewe’s workforce, which is represented by the Transport and General Workers union.
Last year, management trimmed the plant’s employment 10% but was careful not to eliminate the more highly skilled such as Kath Green.
Green is one of two people at Crewe qualified to wrap steering wheels. Asked if she’s irreplaceable, Green replies with proper British modesty: “I’d like to think so.”
Inside the luxury-car industry’s largest wood shop, technology and hand-craftsmanship also coexist. Giant automated lathes trim thick blocks of wood down to dimensions craftsmen can handle before applying the mirror-matched veneer leaves.
Most of the veneer comes from California, such as the most-popular Burl Walnut, although Bentley also seeks wood species from Spain, Central America and South Africa.
All wood parts, including the distinct waistrail that circles the rear cabin of the Mulsanne unbroken, are sanded by hand before entering the lacquer process where up to five coats of polyurethane upwards of 1 mm in thickness is applied. The parts are cured for several days before polishing and shipment to the main build hall.
Inspectors check paint quality.
As testimony to Bentley’s “spare-no-expense” approach to the Mulsanne, the auto maker dedicates one person to manufacturing the wood and leather-lined iPod drawer that pops out of the car’s center stack.
Although the Mulsanne represents the first Bentley developed with extensive use of computer-aided design and engineering, the company’s craftsmen were brought into the process early on to provide input, Lofkin says.
“Technology working alongside customer preferences,” he says.
At the heart of Crewe lies its engine plant, arguably the heart of every Bentley built as well. In addition to the redesigned 6.75L twin-turbo in the Mulsanne, workers produce the 12-cyl. “W12” engine for use in other Bentley, Audi and Volkswagen products.
According to engine-room manager Steve Ball, the operation produces 28 W12 engines and five 6.75L motors daily.
Contrary to popular belief, one person does not assemble an entire 700-part Mulsanne engine. Ball, a 34-year veteran of Crewe, says it would lead to too many inconsistencies. Therefore, the auto maker divides the process between five workers, with the person performing the final inspection receiving his signature on the engine.
Each process takes 95 minutes, beginning with the loading of the cylinder block and installation of the main bearings and crankshaft. At the next station, the pistons are inserted, the flywheel installed and the engine balanced. A third person performs functions such as adding the cylinder heads, fuel rails and the turbo charger.
A fourth station fits the power-steering pump, air pump and other accessories, while at the final stop, the motor receives items such as its pipe work, coolants and undergoes testing to ensure spotless noise, vibration and harshness characteristics.
Each week, one engine is pulled off both lines and disassembled for a quality check.
After testing, the engine and transmission are united and dropped onto the car’s rear suspension, which also is built in the engine room. From the first work station until it heads to the main build hall, workers spend an average of 30 hours on each Mulsanne motor.
Sixteen people, each with an average 16 years’ experience, work on the Mulsanne V-8.
Inside the main build hall, where the “L”-shaped Mulsanne line hugs a “U”-shaped Continental line, the Mulsanne receives its wiring, fuel tank, front suspension and subassemblies trimmed in leather, wood and stainless steel.
A dedicated team of 98 workers focuses exclusively on production of the Mulsanne. Before it is fueled and placed on a shaker rig for final testing, more than 2,000 quality checks will have been performed.
About the Author
You May Also Like