ZF Conquers Logistical ChallengesZF Conquers Logistical Challenges
Throughout history, Shenyang, a city in northeast China that once served as the capital of the Manchurian Empire, has reinvented itself time and again. Today, with 7 million people, it is an industrial city known for machine equipment and is attracting many foreign-owned auto-industry companies, including Germany's BMW AG and ZF Group. BMW was preparing to produce vehicles in the region with its joint-venture
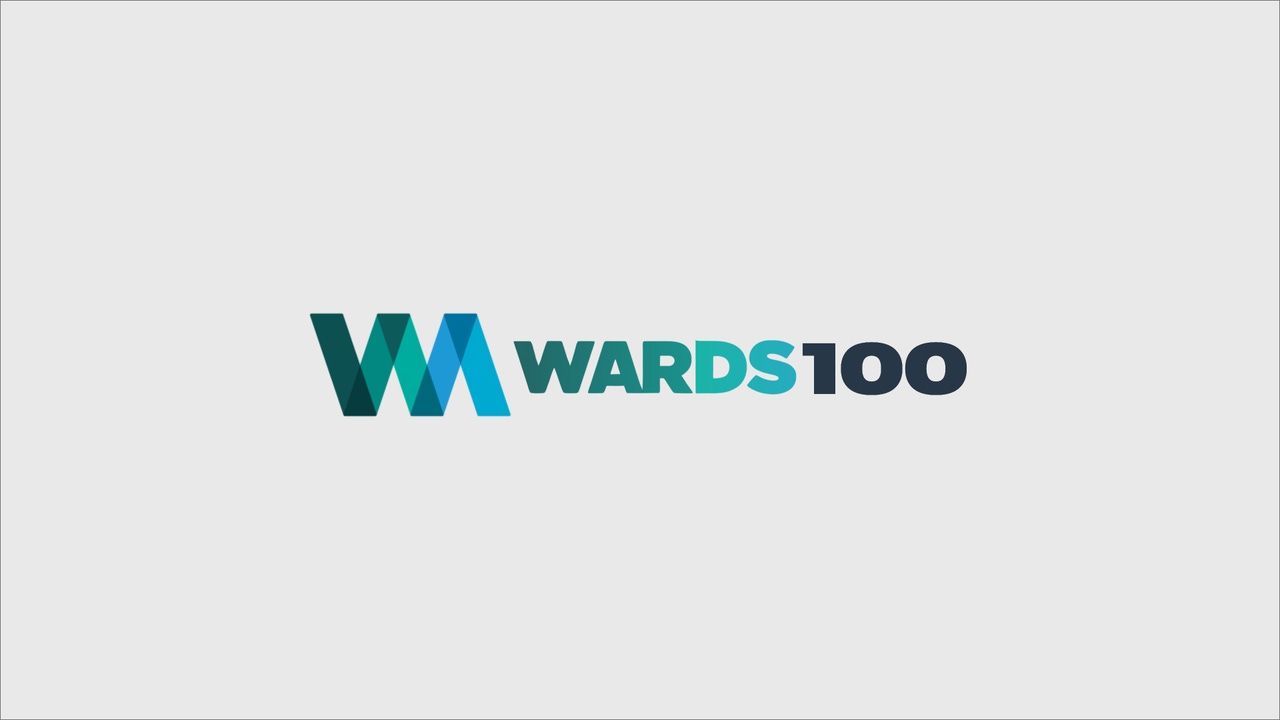
Throughout history, Shenyang, a city in northeast China that once served as the capital of the Manchurian Empire, has reinvented itself time and again. Today, with 7 million people, it is an industrial city known for machine equipment and is attracting many foreign-owned auto-industry companies, including Germany's BMW AG and ZF Group.
BMW was preparing to produce vehicles in the region with its joint-venture partner Brilliance China Automotive Holdings Ltd. and needed ZF's Lemforder division to locate nearby to supply front- and rear-axle assemblies for left-hand-drive 3-Series and 5-Series sedans.
The BMW venture, which recently launched production, reportedly is rolling out 42 cars per day and will increase that to 100 daily by the end of the year. The plant has a 30,000-unit annual capacity.
ZF signed a lease in February 2003 for a new building under construction in a Shenyang industrial park. While the facility would assemble complete-knocked-down axle kits, the logistical challenges were extreme. Production equipment and components would be shipped in from Germany and South Africa.
The 3-Series axle assemblies are shipped in 80 pieces, while the 5-Series modules are shipped in 200 pieces to Shenyang. The trip takes seven weeks, and watertight containers are used to prevent moisture from damaging the components.
“We want the auto industry to know we can build high-quality axle systems in China and deliver them just-in-time,” says Manfred Lagemann, a global project manager for ZF Lemforder. “And we deliver the same quality as we do in Germany.”
The supply-chain logistical software, supplied by SAP AG, is identical in Shenyang to the system used by ZF in Europe and around the world.
Despite the logistical challenges, and the low level of value-added content in Shenyang, ZF says the plant is profitable. Lemforder says the business model works.
Although 100% of ZF's components come from overseas to support Shenyang, the company is preparing to handle more direct production at the plant to fulfill the government mandate that 40% of a vehicle's content be locally produced.
Starting this year, ZF will begin meeting the 40% local-content requirement at Shenyang with suspension and steering components produced at other ZF plants in China. Companies that do not achieve 40% local content can expect higher import duties.
ZF owns 100% of the Shenyang facility. Many other plants in China (including ZF's) are joint ventures between a domestic and foreign-based company. But the Chinese government has been allowing more foreign ownership of facilities in recent years, the company says.
Gross pay for employees at Shenyang is about RMB1,500 ($181) per month, excluding benefits, says Plant Manager David Huang. The plant currently has 50 employees and will grow to 70 later this year.
Incentives in the region (tax breaks, infrastructure installation, etc.) have been so attractive that foreign companies are coming in droves to Shenyang.
“One year ago, there was nothing here,” Lagemann says of his building and the 10 others around it that have sprung up in the last 12 months. Some roads at the industrial park are so new they have no lane markers or posted speed limits.
About the Author
You May Also Like