Chrysler Academy Focused on Cutting Waste, Problem Solving
Chrysler is adding online courses and a mobile trailer will be used to take training opportunities to plants outside Southeast Michigan. A satellite location will be opened in Mexico.
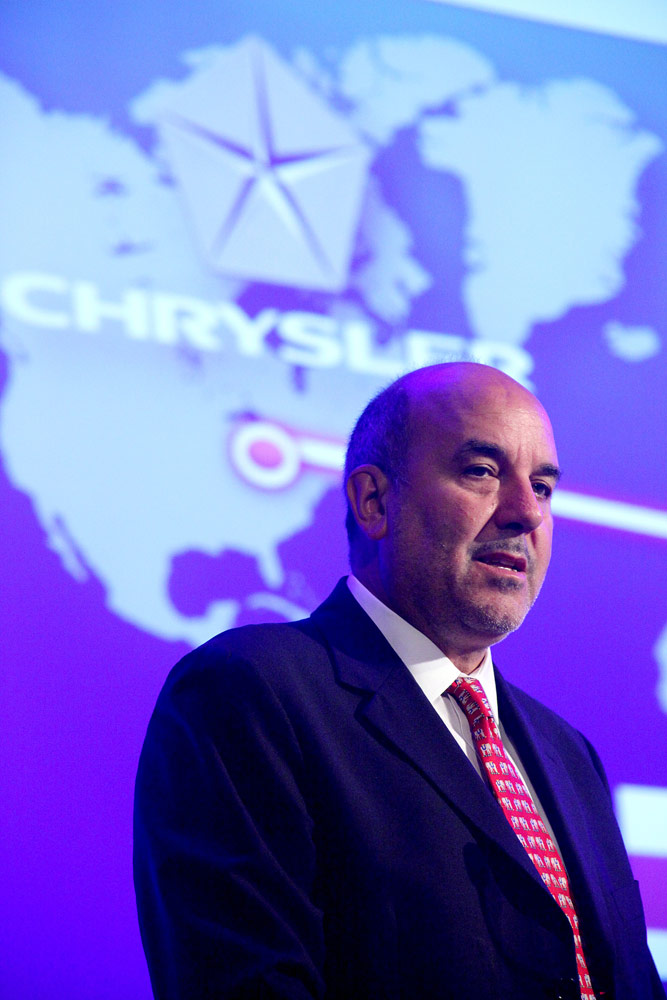
TRAVERSE CITY, MI – Chrysler’s World Class Manufacturing Academy, established in Warren, MI, four years ago, has helped eliminate nearly $1 billion in waste from the auto maker’s North American facilities, an executive says.
Mauro Pino, vice president-vehicle assembly operations, says employees sent to the academy first are assessed to determine their skill level, then tracked through specific training sessions developed to best enhance their abilities.
Students then are rated on a scale of one to five, with level-5 students certified to train others.
The WCM Academy is focused on identifying and eliminating wasteful practices in plants, as well as developing problem-solving skills. New students initially are taught through reading and lectures, then move to the hands-on instruction that accounts for about 70% of the total training.
Rather than concentrate on potential future manufacturing issues, sessions are centered on current problems being experienced at Chrysler’s factories, Pino says.
“It’s just-in-time training,” he says at the 2013 CAR Management Briefing Seminars here. “When finished, we look for employees to have the right skills to attack wastes and losses.”
At the time the academy was established, only 12 courses were available. Today there are 35, and more are planned. To date, some 5,000 Chrysler workers from Mexico, Canada and the U.S. have completed training at the academy.
Pino says the United Auto Workers union is a strong partner in the program, with a UAW facilitator taking part in each training session.
Classes are composed of 16 people, with 10 coming from a single plant and the rest workers from other facilities included for additional perspective. After training, workers go back to their jobs but return several weeks later for evaluation and to share experiences that may be added to Chrysler’s best-practices list.
Many employees are skeptical of the program at first, with some resisting the training. Those are among students Pino calls prisoners, who “show up only because they are ordered to,” and tourists, who “take a wait-and-see attitude to see if there is anything interesting.”
Those are weeded out, he adds, and “after removing the prisoners and tourists we’re getting positive results, with 95% of people coming to train.
“Once they become immersed, they see how (the academy) is not just the ‘flavor of the month’ and become advocates.”
Those newly converted have contributed to improving curriculum, Pino says, pointing to the 356,000 suggestions by former students. About 70% of those already have or are being implemented.
Chrysler plans to add an additional 15,000 sq.-ft. (1,393 sq.-m) to the academy floorspace, bringing total size of the training center to 40,000 sq.-ft. (3,716 sq.-m).
Online courses are being established and a mobile trailer will be used to take training opportunities to plants outside Southeast Michigan. A satellite location will be opened in Mexico.
“We want to remove excuses,” Pino says. “We don’t point fingers, but focus on removing problems as quickly as we can. Time is money and resources are not infinite. The future has challenges that you can’t predict, so that (the academy) puts a premium on flexibility and speed.”
About the Author
You May Also Like