Chrysler Assures Hemi's Future
The Ward's 10 Best Engines competition celebrates 13 years of recognizing outstanding powertrain development. In this fourth of a series, Ward's charts the development of Chrysler Group's popular Hemi V-8. Watch for features on the other 2007 winners throughout the year.
June 1, 2007
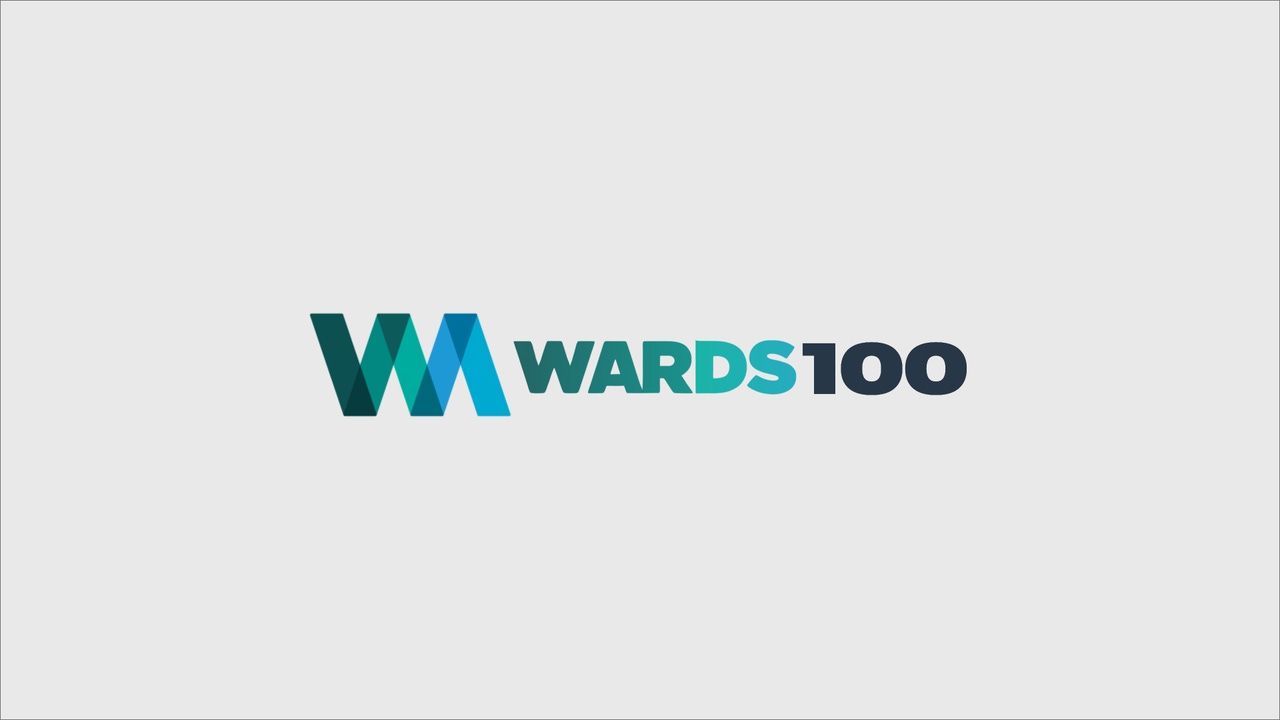
The Ward's 10 Best Engines competition celebrates 13 years of recognizing outstanding powertrain development. In this fourth of a series, Ward's charts the development of Chrysler Group's popular Hemi V-8. Watch for features on the other 2007 winners throughout the year.
Five consecutive years as a Ward's 10 Best Engines winner — not to mention more than 1 million Chrysler Group customers — are testimony the Hemi 5.7L OHV V-8 is one of the auto industry's most satisfying and emotive mass-market V-8s.
Now, the only thing left for the Hemi to prove is whether it, and other large-displacement V-8s, can continue to be relevant in a market where customers and regulators alike share a mindset that is an ever-deepening shade of green.
One person, Robert Lee, is certain the Hemi can adapt to a market where $3-plus gasoline appears here to stay. Lee has a pretty credible perspective as Chrysler Group vice president-powertrain product engineering and generally is credited as the “father” of the modern-day Hemi architecture.
“The initial Hemi design (introduced for the '03 model year) was done with several future upgrades enabled,” Lee says.
The engine was introduced in trucks first, and then fuel-saving Multi Displacement System (MDS) cylinder-deactivation hardware was added when the passenger-car version arrived for the LX vehicles, including the Chrysler 300 and Dodge Magnum.
Now, MDS is fitted to almost every new Hemi, whether it's in light trucks, SUVs or passenger cars.
But there are more improvements coming to augment MDS, Lee says.“Although we don't comment on the specifics of future products, it's safe to say that additional (efficiency-enhancing) design features will be unveiled very soon which will build upon the Hemi architecture,” Lee says.
“I believe derivatives of the Hemi architecture will still be relevant in the Chrysler Group product line in the 2015 timeframe,” he adds.
First and foremost, however, Lee reminds that the Hemi's foundation architecture — and the basis for its nickname — was chosen for its intelligent, logical design.
“The key to performance in any IC engine is efficiently getting air into the combustion chamber such that the appropriate amount of fuel can be added to make the desired power,” Lee says, adding that the geometry of hemispherical combustion chambers allow for straight ports and optimized valve angles for the air to enter and escape.
“For a 2-valve-per-cylinder design, this is the most efficient configuration,” he says. And there are manufacturing advantages, too. The 5.7L and 6.1L Hemis use a cast combustion chamber and conventional valve seat machining, Lee says.
“A pent-roof chamber typically has flat surfaces and a much smaller included valve angle than a hemispherical chamber. This is convenient for placing two valves side-by-side on both ‘slopes’ of the roof. This is the typical geometry for the 4-valve-per-cylinder configuration for gasoline automotive engines.”
That means although the Hemi is slated for advances, don't look for any changes to the seminal cylinder-head design from which the engine takes its name. The Hemi will remain a Hemi.
“I believe there is a place for a relatively simple, large gasoline engine architecture, especially in work-mission-related vehicle applications,” Lee says. As fuel-economy requirements rise, he says more can be done with the platform to simultaneously optimize performance while maintaining affordability.
“The present 5.7L/6.1L engines are very competitive in the market against other engines which use variable valve timing, active intake manifolds, charge motion control valves, etc.,” Lee says. “These and other technologies could be applied in the future to extend the capabilities of the Hemi.”
Although the Hemi seems certain to change, Lee says another crucial aspect of the engine's cylinder-head design, the signature twin-sparkplug layout, also will stay, although without the “staggered” ignition the design makes possible, but not always profitable.
“The twin-plug arrangement is an integral part of burn-rate control with the Hemi architecture,” he says.
When the Hemi was introduced in '03, the hardware and control system were capable of staggered spark timing primarily to mitigate burn rate-generated noise from combustion. However, Lee says it was learned late in the development program that this provision was not needed, and it was subsequently removed.
Most intriguing in the Hemi's immediate future is its pairing with hybrid-electric components for Chrysler's first production hybrid-electric vehicle, the Dodge Durango, slated for 2008.
Chrysler says the Hemi in a 4-wheel-drive Durango Hybrid will deliver a combined city/highway fuel economy rating of better than 19.4 mpg (11.9 L/100 km) — a 20% upgrade compared with the combined 15.5 mpg (15.2 L/100 km) of today's conventional Hemi-equipped Durango.
Lee says hybridization and MDS are mutually supporting technologies. “Hybridization is a system optimization exercise,” he says. “Of course, it involves the engine, but more so it involves all aspects of the powertrain and vehicle system. I really think of hybrid vehicles as control systems on wheels.
“Adding an electric motor, or for that matter a hydraulic motor, allows additional torque to be added to the system upon demand.” This can be used as a “range extender for MDS operation under certain conditions,” Lee says — meaning the Hemi can use MDS more often to operate in 4-cyl. mode.
“This is just one of many ways ‘optimization’ is possible with hybridization,” Lee says, adding the Hemi's dual-plug ignition and MDS provides an excellent “platform” for hybridization.
Pursuant to improving overall vehicle economy, Lee says it's also conceivable the Hemi — to now, using a cast-iron block — could one day move to all-aluminum construction, if the cost-benefit ratio is worthwhile. And considering the steadily rising price of gasoline, that ratio appears more attractive almost daily.
Weight is always an important consideration in the tradeoff decisions for engines, Lee says. “The manufacturing processes for aluminum cylinder blocks are well known, and so are the weight benefits.
“To date,” Lee counters, “other systems on the engine have been a better value to satisfy government and customer requirements. Now, with the heightened emphasis on fuel economy, we are revisiting the tradeoff benefits of aluminum blocks as well as other technologies.”
Does Lee worry rapidly advancing diesel technology may make large-displacement gasoline engines irrelevant?
Not much. He admits diesel engines are superior in fuel economy, but they require significantly more effort to comply with increasingly stringent emissions standards.
“Gasoline engines are well understood, and the emissions systems are very well developed,” Lee says. “Now, the major emphasis is to improve the fuel efficiency by adopting engine technologies which are more diesel-like: Direct injection, higher compression ratios, and eventually ignition without a spark are on the horizon.”
This will result in lower emissions than a diesel, as well as performance rivaling the diesel at low speed and likely better than the diesel at higher engine speeds, Lee promises.
Meanwhile, which of the Hemis past does Lee consider the “classic?” He is an assiduous student of history's variants of the hemispherical combustion chamber that date to Chrysler's first use in a fighter-plane V-16 layout in 1939.
“I would have to go with the 426 cu.-in. (7.0L) ‘street’ Hemi,” he says. The 426 Hemi V-8 was introduced in 1964 for racing applications and was made available for production cars in 1966.
He says only about 11,000 were made, but the engine was so vastly superior to other V-8s in the market that it solidified the Hemi name and image.
“It simply dominated,” Lee says.
ENGINE SPECS
DaimlerChrysler AG
5.7L 90° OHV V-8
Displacement (cc): 5,654
Block/head material: iron/aluminum
Bore × stroke (mm): 99.5 × 90.9
Horsepower (SAE net): 340 @ 5,000 rpm
Torque: 390 lb.-ft. (529 Nm) @ 4,000 rpm
Specific output: 60 hp/L
Compression ratio: 9.6:1
Assembly site: Saltillo, Mexico
Application tested: Chrysler 300C
EPA fuel economy, city/highway (mpg): 17/25
About the Author
You May Also Like