Chrysler Brings New V-6 to Daimler Marriage
No one disputes the technical prowess of Daimler-Benz AG and its famed Mercedes-Benz cars.But in the pending merger of the German company with Chrysler Corp. to form DailmerChrysler AG, don't overlook technology the U.S. company brings to the marriage.A prime example is the new 3.5L, 253-hp V-6 engine powering the 1999 Chrysler LHS and 300 M models that go on sale this summer (see New Wheels p.56),
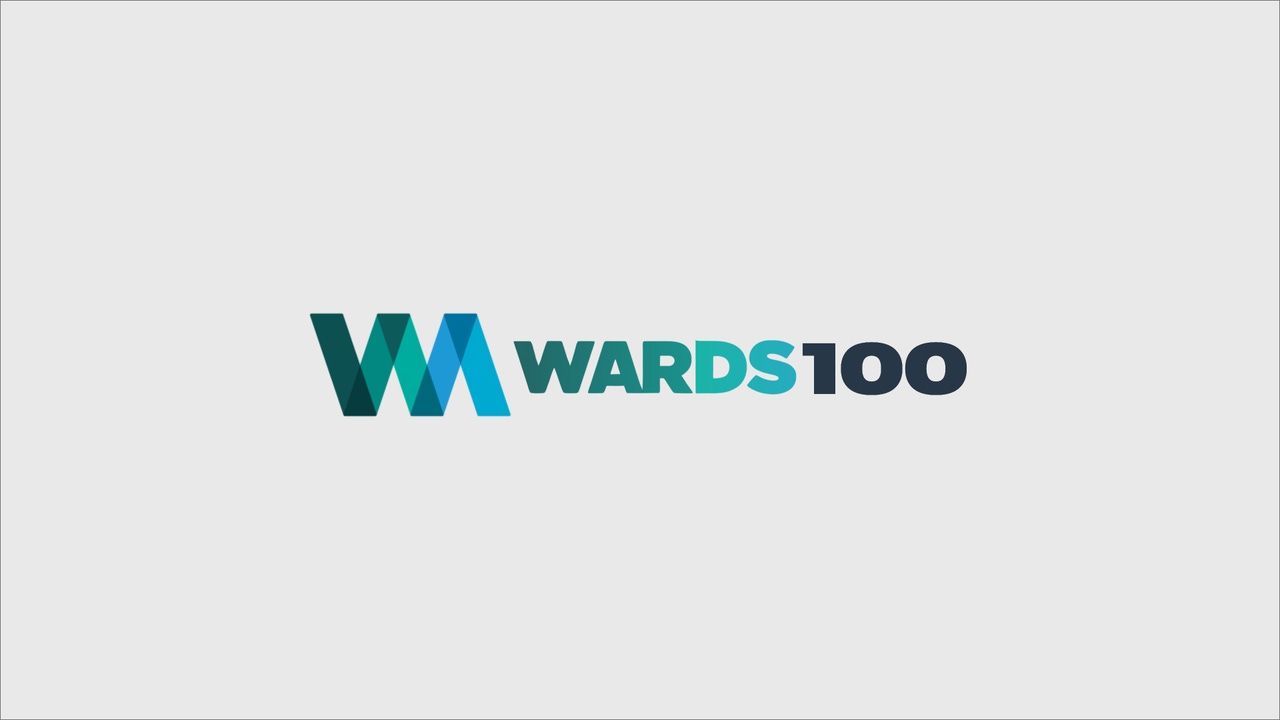
No one disputes the technical prowess of Daimler-Benz AG and its famed Mercedes-Benz cars.
But in the pending merger of the German company with Chrysler Corp. to form DailmerChrysler AG, don't overlook technology the U.S. company brings to the marriage.
A prime example is the new 3.5L, 253-hp V-6 engine powering the 1999 Chrysler LHS and 300 M models that go on sale this summer (see New Wheels p.56), developed using advanced computer engineering technology.
The 3.5 is the newest of a family of 4-valve-per-cylinder all-aluminum V-6s Chrysler began developing in 1995; 2.7L and 3.2L versions led the parade.
Chrysler invested $625 million in the V-6 project. The 3.5L version is standard in the LHS, while the 2.7L as well as 3.5L are offered in the 300M.
Generating 253 ft.-lbs. f torque at 4,000 rpm, Chrysler claims the 3.5 produces more horsepower and torque than the Mercedes E320, Lexus GS300 and BMW M3, all world-class performers. Benchmarking targets included Toyota's 3L V-6, Ford's 2.5L Duratec V-6 and General Motors' 4L Northstar V-8.
What makes the new V-6 family significant is that it was the first "paperless" Chrysler engine project, utilizing computer software to slash development time and improve reliability and performance.
Burke Brown, executive engineer for large car powertrain, led the 3.5L program. He reckons Chrysler saved 26 weeks of development time on the engine by using advanced computer engineering."To me, the single thing that made the most difference in everything from the cylinder head to the exhaust was that we used CFD (computational fluid dynamics)," he says.
First, he and his troops needed a software model that could be easily adapted to Chrysler's hardware. A program called Star CD was selected to map catalyst gas distribution. "We established a working plan with the software and gained confidence it would meet our targets," says Mr.Brown.
"We didn't want to test everything (actual hardware), so when we engineered the engine we used CFD for everything in the air flow," he adds.
The plastic intake manifold, for example, called for a three-plenum design to maximize performance at full throttle. Using CFD Chrysler engineers looked at hundreds of configurations to obtain the best structure, he says.
Most importantly, the software enabled Chrysler to push down computer power from its Cray super computers to engineers' desktop PCs. "That's the beauty of it," says Mr. Brown. "You can load in on Saturday morning, run over the weekend and come in Monday with lots of answers. No one today would make a change in the air-flow path without checking the model. If we had a change in the old days, we'd build a couple of cars to do emission tests."
Designing the cylinder head "was tough because we had to serve all masters, including the assembly process. There was a menagerie of packaging challenges," he says.
He credits both computers and "teamwork" for meeting "all objectives," including solutions to potential "Big Old Sally" problems in manufacturing such as cooling around the valves, shaping of the intake and exhaust ports, spark plug location and valve-train layout.
"In the end it's got to be manufacturable," says Mr. Brown. "That's the beauty of the model: All iterations and combinations could be tried and decisions made on the model. Then, in the test phase, the flow dynamics were already in place.
"That left dynamometer time to run more reliability tests. We didn't have to spend time breaking a bunch of components to make a change."
That saved both time and money. "Often if you run the first phase and you're off on fuel economy or emissions, you have to change your feasibility testing and go with different valves or ports and restart the program." Advanced computer engineering, he says, "reads back to huge reliability and confidence levels."
But computers can go only so far. Chrysler tested the new 3.5L V-6 over 4 million miles, half in cars and half on dynamometers. "We wanted to make sure it was bulletproof, and we found out computer engineering worked the way we thought it would," he says.
"We got the 0-60 time we targeted and more than 250 hp. It just came together. It was not that big a deal, although the guys would shoot me if I said that. Heck, we got 234 hp out of the box before any real development."
About the Author
You May Also Like