Detroit Faster on Its FeetDetroit Faster on Its Feet
During the oil crises at the beginning and end of the 1970s, soaring prices changed consumer tastes almost overnight. Detroit auto makers were devastated each time because most of their products were gas-guzzlers and they could not revise their lineups fast enough. Is history about to repeat itself? Fortunately for General Motors Corp., Ford Motor Co. and Chrysler Group, the product-creation process
July 1, 2006
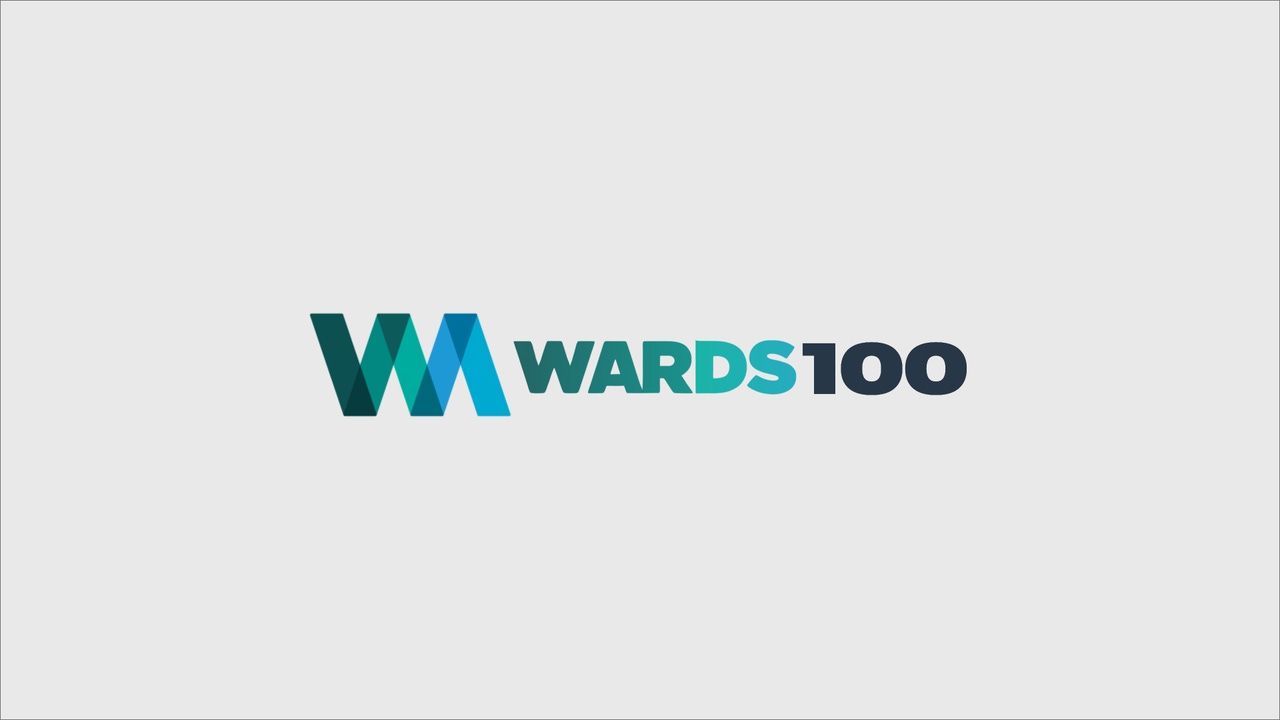
During the oil crises at the beginning and end of the 1970s, soaring prices changed consumer tastes almost overnight.
Detroit auto makers were devastated each time because most of their products were gas-guzzlers and they could not revise their lineups fast enough. Is history about to repeat itself?
Fortunately for General Motors Corp., Ford Motor Co. and Chrysler Group, the product-creation process is conspicuously different this time around. Back then, there was a huge gap in product development time — 60 months for Detroit vs. about 36 months for Toyota Motor Corp. and Honda Motor Co. Ltd.
According to Automotive Product Design & Development Delphi, a study by the Center for Automotive Research (CAR) completed last year, the product-development gap among regions has narrowed significantly, although Detroit still is chasing the fastest Japanese auto makers.
For carryover platforms, in 2004 U.S. auto makers took 16 months for product development, design and launch (the period from an approved clay model — “design freeze” — to production of the first salable unit).
European car companies required just 15 months, while Japanese auto makers completed the process in 13 months.
For a vehicle built on an all-new platform, the concept-through-freeze-to-production time span in 2004 stood at 36 months in North America, 32 in Europe and 29 in Japan.
By 2009, it will contract to 32 months in North America, 29 in Europe and 26 in Japan, according to the Delphi study, which compiles the views of selected executives representing an industry cross-section.
GM, for one, stopped discussing this aspect of its product-creation process. It's now held as proprietary, says a GM spokesman. Besides, the spokesman adds, “we found that everybody measures it differently. It's impossible to do an apples-to-apples comparison.”
Brett Smith, CAR assistant director-manufacturing, engineering and technology, notes that Honda and Toyota still develop new vehicles the fastest, “by quite a bit.” Meanwhile, South Korea's Hyundai Motor Co. Ltd. “is also moving toward the Toyota/Honda standards.”
All auto makers have gained in the design-time race by using new engineering technologies that continue to advance. The old terms: computer-aided design; computer-aided manufacturing; and computer-aided engineering (CAD, CAM and CAE); still broadly apply to the software tools that engineers use.
Managers still rely on product-data management and product-lifecycle management software to organize, control and disseminate engineering information. Specialty software suppliers — led by the big three in the field: Dassault Systemes of Paris; Parametric Technology of Needham, MA; and UGS of Plano, TX — still provide the majority of tools used by auto companies.
But in recent years, those tools have acquired so much capability they make their predecessors look as antiquated as manual drafting.
With abilities such as morphing available in CATIA design software from Dassault and NX from UGS, the tools automatically generate new designs from performance requirements typed into a spreadsheet. Following rules set up by the manufacturer, morphing keeps the product variations it creates within cost boundaries, manufacturing constraints, performance parameters, and so on.
More sophisticated tools have helped vehicle engineers approach some longstanding goals, especially simultaneous engineering.
“The idea used to be that you couldn't start the manufacturing design process until you had all of the design elements figured out,” says Monica Schnitger, senior vice president-market analysis at technology consultants Daratech in Cambridge, MA.
In other words, engineers no longer have to quantify every piece of information down to its most detailed level before they can start sharing it.
Design executives report parallel engineering is helping speed manufacturing planning and product testing, in particular. For example, CAE tools “have come miles in their ability to help us predict accurately the performance of the car,” Mark Chernoby, vice president-advanced vehicle engineering for Chrysler, says.
At a recent conference, Toshiyuki Nakajima, senior manager-Vehicle Planning and Strategy Development, Vehicle Production Engineering Div. at Nissan Motor Co. Ltd., says his company used DELMIA process-planning software from Dassault to digitally simulate manufacturing of the Note, a small car sold in Japan.
Note production began after only one manufacturing trial, rather than the three trial runs Nissan ordinarily performs, Nakajima says. That helped cut the company's customary 20-month procedure to 10.5 months, he says.
But no matter how quickly Detroit auto makers kick out new-product designs, they still are stuck with old habits that could hamstring their time-to-market.
Those habits fall in the category of cultural practices. One is their long-standing emphasis on large trucks — pickups and SUVs — that leaves them lacking experience in designing small vehicles. The other is a lingering inconsistency in design operations that makes the translation to manufacturing less efficient and effective. Those inconsistent practices also make it harder to assure their products will excel in every competitive measurement.
“The Detroit three are definitely at risk,” says CAR's Smith. “The light-truck focus during the last decade has left them with limited small-car development resources,” he says.
His colleague, Richard Gerth, a research scientist at the center, says another issue is launch time and reliability.
“The traditional domestics are more at risk because they have difficulty retaining knowledge between launches; and their designs have tended — more so in the past — to be different from program to program,” Gerth says.
By contrast, Gerth says, a hood design within Toyota has the same basic architectural characteristics regardless of the product: small car to truck or SUV. This reduces the likelihood of things going wrong and increases the likelihood that someone will know what to do if something does go wrong.
However, organizational changes are helping cut design times while improving engineering practices.
In North America, auto makers are “decoupling” system and component development from vehicle-design programs, says the GM spokesman.
Whether tackled by OEM or a supplier, new technology is developed independently and then incorporated into a vehicle design. The approach is already popular with Japanese auto makers, especially Toyota.“They do a whole lot of heavy lifting early; and it's pretty smart,” he says.
So-called decoupled development is a big part of the evolving Chrysler Development System, or CDS — a large-scale initiative to make product and production-process verification fully digital, without recourse to physical prototypes.
While it advances component technology, decoupled engineering also helps Chrysler push component re-use, to save time, shave costs and assure quality by capitalizing on pre-existing parts that already have been designed and tested.
To decouple design, Chrysler set up two engineering sectors. In one, component teams design, update and maintain individual parts. The other sector consists of product teams that engineer new vehicles. To assure communication between the component teams and the product teams, the company created a software system it calls “automotive schema.”
A digital representation of a vehicle, automotive schema is the mandatory starting point for product engineers embarking on a new design. Speaking at a Dassault conference, Roger Lundberg, Chrysler's director-vehicle engineering operations, calls it “one-stop shopping” for components.
“We fundamentally changed the way an engineer makes a part,” Lundberg says.
“He now goes into automotive schema and pulls out a part number. We provided the component teams the ability to lock down certain parts, so an engineer on a new program team could not just start from scratch.”
Reorganization on a global scale is a large part of the plan to jump-start small-vehicle development at Ford and GM, says CAR's Smith.
While Chrysler has taken small-car development back from Mitsubishi Motors Corp. “Ford and GM are increasingly relying on overseas operations to engineer their small cars,” Smith says.
That means Ford of Europe and Mazda Motor Corp.; for GM, Adam Opel GmbH and its Daewoo Auto and Technology Co. joint venture, Smith says.
Beginning Jan. 1, GM implemented a single, integrated international design and engineering organization. Formerly, engineers in different regions worked independently to create similar vehicles.
Now it has global development centers for all architectures in regions that have expertise for certain vehicles. Those centers will oversee the architectures from cradle to grave. For example, North America will take responsibility for trucks and utilities and derivatives, Europe will handle midsize cars and Asia develops small cars.
Under this structure, says the GM spokesman, “If we get a market shift — say, for example, gas prices go higher — it makes it a lot easier to look at another region, identify a vehicle and quickly homologate it for the U.S. market.”
Read more about:
2006About the Author
You May Also Like