Flexible Manufacturing Comes ‘Standard’ at ChryslerFlexible Manufacturing Comes ‘Standard’ at Chrysler
Model changeovers and on-the-fly introductions of additional models will be measured in days, not weeks, “once we have the base process installed,” says Chrysler manufacturing chief Scott Garberding.
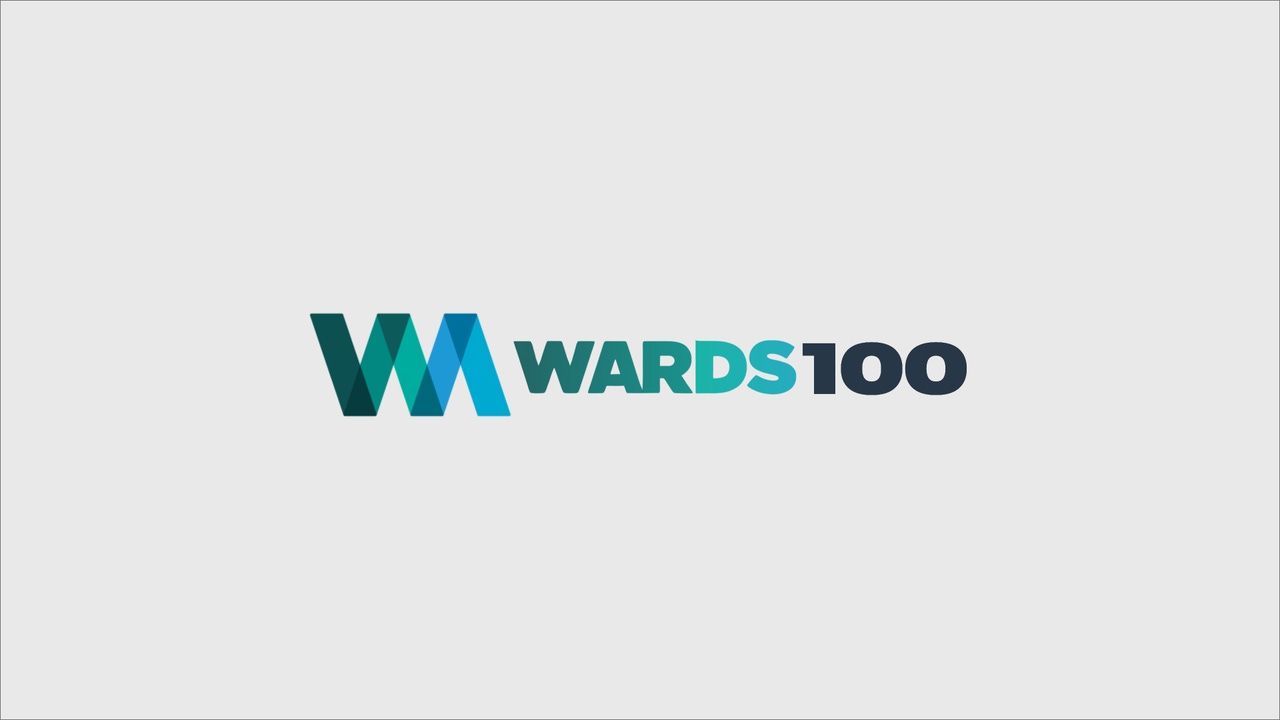
Special Coverage
The Flexible Industry

The tangible signs of Chrysler’s flexible manufacturing ambitions are apparent in the 638,000-sq.-ft. (59,272-sq.-m) expansion of its assembly plant in Belvidere, IL. But the genesis of the auto maker’s latest manufacturing strategy is invisible to the public eye, beginning on the drawing board, where disparate vehicles are designed to neatly file nose-to-end through cookie-cutter body shops.
“Process is a function of the vehicle design,” says Scott Garberding, senior vice president and head of manufacturing.
Body shop expanding at Chrysler’s plant in Belvidere, IL.
And, borrowing technology and inspiration from alliance-partner Fiat, Chrysler expects its new process to deliver critical time savings in the all-important race to market. Model changeovers and on-the-fly introductions of additional models will be measured in days, not weeks.
“Once we have the base process installed, we can add in new models pretty transparently, without really shutting our assembly process off,” Garberding tells Ward’s.
Improving manufacturing flexibility is not a new goal for Chrysler. It has been high on the auto maker’s agenda since at least 2005. Then, as now, Belvidere was Ground Zero.
Nearly $420 million was pumped into the plant’s body shop to accommodate output of D- and C-segment vehicles. But only the latter saw production at the site as cataclysmic economic developments conspired to thwart Chrysler’s aspirations.
Fast-forward to today. The auto maker is investing another $600 million at Belvidere, the first Chrysler plant to benefit fully from the auto maker’s tie-up with Fiat.
“The products that we’re working on right now, for the most part, will be based upon a Fiat-originated architecture from which we are developing several platforms,” Garberding says.
Belvidere-made Dodge Caliber will give way to Fiat-based car.
Chrysler has said Fiat-based platforms will account for some 56% of its worldwide car volume by 2014.
Garberding is mum on precise product plans, but the Belvidere-built Dodge Caliber C-car is scheduled to go out of production in 2012. It will be replaced by a C-segment vehicle based on a platform dubbed C-U.S. Wide and adapted from the bones of Alfa Romeo’s acclaimed new Giulietta.
Early iterations of the pending Dodge, which will be joined by a Chrysler-badged cousin, rival the Volkswagen Golf’s ride and handling characteristics, according to Chrysler design chief Ralph Gilles.
Tooling is a key enabler in the evolution of Chrysler’s manufacturing flexibility, Garberding says. So the auto maker has enlisted Fiat subsidiary, Comau, to build Belivdere’s new body shop – a project set for completion this year.
The relationship is not new. After a troublesome Caliber launch soured Chrysler’s relationship with ABB, the auto maker partnered with Comau to oversee the 2006 retooling of its midsize car plant in Sterling Heights, MI.
Going forward, expect Belvidere’s new Comau body shop to be replicated at other plants.
“We absolutely will continue to refine the design so that we get better every launch,” Garberding says. “As opposed to starting with a clean sheet of paper every time we do a body shop, we can focus on the areas that need focus and leave the other areas alone.”
Asked where the next investment will be, Garberding does not tip Chrysler’s hand. But he promises “several” U.S. plants with enough flexibility to build “most” vehicles from a single Fiat architecture. And there will be “at least one plant that can produce all the vehicles in the family.”
As a result, Chrysler’s assembly network will have “nearly the same flexibility as if all of our plants were completely flexible.”
Reflecting a new discipline instilled by CEO Sergio Marchionne, who also heads Fiat, bang-for-the-buck is essential to Chrysler’s manufacturing strategy. So don’t expect to see Fiat 500 minicars rolling off the same line as a Ram fullsize pickup, Garberding says.
“It technically could be done, but there would be almost no economy. Where we’d like to be is to have groups of plants that can produce multiple vehicles that are designed with the same architecture, but can serve multiple platforms.”
This strategy also extends to stamping plants and engine production. Garberding expects significant benefits from the plug-and-play versatility of Chrysler’s new Pentastar V-6, which has been designed to replace seven 6-cyl. engines.
The Pentastar is produced at two identical plants: Trenton, MI, and Saltillo, Mexico. Each can accommodate mix changes “quickly, without process tear-up” when decisions are made to add content, such as direct injection or turbocharging or Fiat’s MultiAir valve-actuation technology, Garberding says.
Underscoring Chrysler’s flexible-manufacturing efforts is the implementation of Fiat’s World-Class Manufacturing quality-control system. The protocol’s customer-based focus is what keeps Garberding awake at night.
“It’s true,” he says. “Because the market’s moving fast for us.”
While Garberding is tossing and turning, Chrysler workers at Belvidere are resting easier. The site’s new body shop is concrete evidence of the auto maker’s commitment to build multiple models there.
“It makes us feel a lot better,” says Bill Campbell, financial secretary of United Auto Workers Local 1268.
About the Author
You May Also Like