Manufacturing Revolution Underway in Brazil Companies build Emerging-MarkettemplatesManufacturing Revolution Underway in Brazil Companies build Emerging-Markettemplates
CURITIBA, BRAZIL - Welcome to the Automotive New World Order.In the heart of South America's most populous nation, manufacturers and automotive suppliers are taking advantage of flexible labor forces and low-volume production to create a learning lab from which they hope to apply lessons to factories throughout the world.What grabs a visitor to factories like Chrysler Corp.'s new Dakota truck plant
August 1, 1998
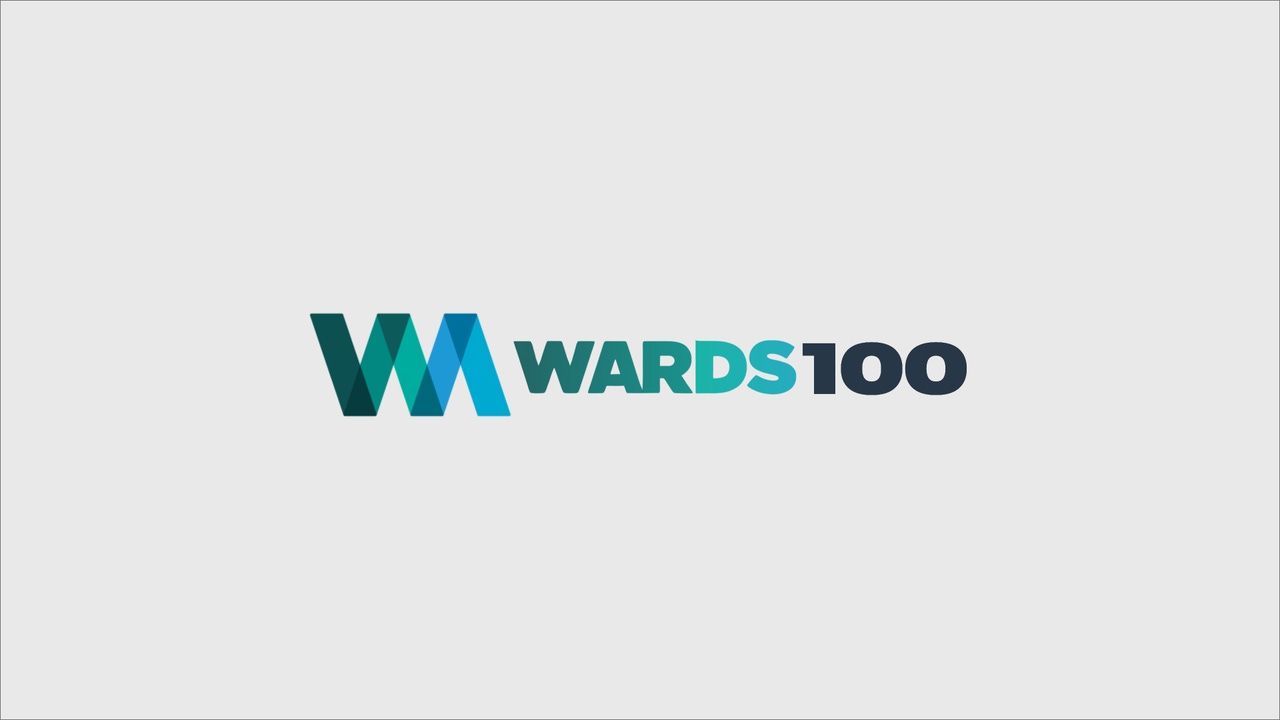
CURITIBA, BRAZIL - Welcome to the Automotive New World Order.
In the heart of South America's most populous nation, manufacturers and automotive suppliers are taking advantage of flexible labor forces and low-volume production to create a learning lab from which they hope to apply lessons to factories throughout the world.
What grabs a visitor to factories like Chrysler Corp.'s new Dakota truck plant here is how the line between original equipment manufacturers and suppliers is blurring almost beyond distinction. We're not just talking about sharing design and engineering; suppliers actually are making most of the finished vehicle.
One auto supply executive suggests that automakers might be best served if they concentrate on vehicle design and marketing, and leave the manufacturing end of the business to suppliers.
"Chrysler should sell pens and shirts - promote their brand and worry about design and direction," says Ruperto Jimenez, president of Dana Brazil, suggesting individual suppliers will be better suited to building the vehicle than the company that sells it. "We know how to make the best chassis. It's all we do," he explains.
If Mr. Jimenez is right, he'll be able to prove it in Brazil. Dana's revolutionary rolling chassis, borrowed from its program for heavy truck manufacturer Mack Truck, is only one of many experiments under way in Brazil.
Why Brazil?
Asia still holds together only on the thinnest of economic threads. Mature markets like the U.S. and Western Europe are held captive by heavy capital investment and strong labor unions. So Brazil emerges as management's next great hope. Auto companies are expected to pour about $40 billion in new investment into this country over the next few years. But rather than repeating the worn-out processes of mature manufacturing, they're trying out unconventional theories in a wide-open frontier where no one is constrained by the ways of the past.
"This market is small enough that companies can afford to take some risks," says Carl Swanson, Tenneco Automotive general manager for South America.
The experimentation forges closer relationships, agrees Michael M. Kamsickas, vice president of Lear Corp.'s Latin American Operations.
Indeed, many of the most efficient supplier and automotive operations in the world now are located in this emerging region.
Growth has exploded since Argentina, Brazil, Paraguay and Uruguay formed the Mercosur trade zone in 1994.
It was a market that smoldered for years with outdated vehicles. Only Ford, GM, VW and Fiat even bothered with programs. But with Mercosur and earnest attempts to stabilize the economy and streamline taxes and regulations, 10 new automakers have either built or announced plants.
Among the newest examples of the "laboratory" mood of Brazil is Chrysler Corp.'s Dakota pickup plan here in the state of Parana. The plant represents only a $315-million investment, well below what Chrysler typically pays to build a new assembly plant.
That's because the automaker was able to save millions by requiring suppliers to share the costs and risks of the project in hopes of sharing in the reward.
Dana's rolling chassis means the plant doesn't have to have the same kind of conveyor system required in conventional assembly operations. Suppliers run the paint shop and other areas of the plant. The parts distribution system is so simplified it can be done with small handcarts, so Chrysler decided to make the facility safer and ban heavier forklifts.
While Dana's rolling chassis is the most aggressive application of modular assembly - it represents 30% of the value of each vehicle - suppliers such as PPG Coatings, Lear, Goodyear, Tenneco and others also are assuming a larger chunk of responsibility than before.
An outside supplier even runs the tool bin in the Chrysler plant. The company only pays when a tool is used, so the tool supplier shares the overhead and inventory costs.
"This is very simple, proven technology," says David Elliot, the 35-year-old plant manager tapped from Chrysler's Graz, Austria, minivan plant. "There is nothing new here. It's not rocket science."
Instead, the Chrysler's Operating System Principles are used to create a more efficient, more flexible work force.
After three weeks of production, the quality of Dakotas coming off the line in Curitiba equals that at Chrysler's Warren Truck in Michigan, Mr. Elliot says.
The flexibility of the young workers is one advantage, he says.
"We're molding employees the way we want them," he says. The core teams of plant leaders studied Chrysler operations all over the world. Rank and file workers are offering three to four suggestions each per month.
But Chrysler also needs a different kind of operation because emerging markets operate by different rules. Because they build less of vehicle content in a plant, there is less automation. The only robot in the Dakota plant applies adhesive to the windows that are then manually attached to the vehicle. Of course, the lack of automation means the automaker takes 26 hours to build a Dakota instead of 20, but with volumes heading only to about 12,000 units in the near future, speed is not as important as cost.
Chrysler's labor rates here range between $5 and $10 per hour, including benefits, well below the $45 it pays in the U.S., but twice or more what most manufacturers pay in Mexico.
More importantly to suppliers, local content rules mean the automaker needs a way to ensure that local suppliers produce a higher percentage of the vehicle. And the best way to get local content is with modules.
For example, Brazil requires 60% local content.
If Chrysler bought all the parts and put them together, that would mean that six out of every 10 parts of the vehicle must come from local suppliers. Sometimes local suppliers are less sophisticated than high-volume foreign suppliers who can produce a part less expensively for import.
So, suppliers put together modules for Chrysler such as the chassis or the exhaust system, which are 60% Brazilian made and therefore qualify as local content. Chrysler then can count all of the parts in the module as local-made, even though as much as 40% might come from Mexico, the U.S. or Europe.
About the only thing Chrysler makes itself for the Dakotas assembled here are stampings and engines - and for diesel trucks, it buys the engines from Detroit Diesel Corp.
For everything else, Chrysler, like other automakers entering Brazil, has assembled a network of suppliers on the cutting edge of new manufacturing and modular systems. Among the innovations:
Dana Corp.
The supplier with its neck stretched the furthest into Brazil has to be Dana Corp. The supplier has committed to providing rolling chassis in sequence on a two-hour lead time in 17 different possible designs.
Dana gets the first indication of what chassis it needs to build when the trucks are rolling from the body shop. Another comes when the Dakota body rolls into the paint shop, and assembly begins.
Dana manages all suppliers for the frame but has direct control over only about 30% of the content. Mr. Jimenez says he expects Dana can get that to about 45% eventually by substituting non-Dana content with Dana parts.
The chassis isn't Dana's only modular business in Brazil. Even without the Dakota operation it has $500 million in modular business, with $300 million alone for front corners on a Volkswagen Gol.
Every 112 minutes Dana gets an order for Gol corners and delivers a module every 42 minutes. That will climb to 550,000 units yearly after VW is at full capacity.
PPG Industries Inc.
Paint supplier PPG has invested more than $100 million here as it builds a new plant north of Sao Paulo.
PPG operates inside the Chrysler Dakota plant, coordinating paint mixing and other activities. Nine PPG employees work directly in the plant, and the supplier provides all of the materials to keep the paint line running, including gloves and masks, says Glenn Thompson, PPG general manager for South America.
PPG actually has more than 20 employees in a Fiat SpA plant in Argentina and has plans for aggressive operations in an upcoming Brazilian Renault plant. It's also doing business with GM, Fiat and Toyota in the region and expects the market for automotive paints to grow to between $130 million and $150 million annually, Mr. Thompson says.
The Dakota plant also is set to benefit from a first-of-its-kind dual e-coat system that will eliminate the need to prime the pickups by hand, says Mr. Thompson. The first e-coat handles the corrosion protection and the next run replaces primer, he says. The process is automated so Chrysler will need fewer employees to run its paint shop.
And everywhere there are signs of new customers.
Two miles down the road from the new PPG Brazilian plant is a major 3M operation, and Honda has a plant across the street from 3M. Toyota is about 20 miles away, Mr. Thompson says.
Detroit Diesel Corp.
The Detroit Diesel plant located near Chrysler's Dakota facility probably is the best plant in the company, says Charles (Chip) McClure, DDC president. It's working out so well that the company will take what it has learned in Brazil and apply it back to the operation in Italy where the diesels were designed.
Detroit Diesel came to Brazil because Chrysler asked the company to support the Dakota project. Eager to develop a light-vehicle diesel engine market, the engine supplier rushed into the project and opened a new facility within a year.
The Brazilian factory now builds 2.5L diesel engines for plants in Toledo, OH, and Argentina, and in the fall will begin supplying diesels for the Dakotas in Curitiba. The plant produced 500 units last year, but is expected to churn out 11,000 to 12,000 engines this year and hit 21,000 by 2000.
Lear Corp.
Lear's operation for the Dakota seems almost too simple for someone with a North American perspective. The interior supplier puts together bench and bucket seats in what once was an abandoned warehouse within sight of the new Chrysler pickup plant.
The company admits the low-tech JIT plant, with capacity for 42 seats a day, is hardly innovative. But it comes close to reducing the interior to one part number as the supplier provides not only the seats but sun visors, carpet floor and back panels, says Chuck Fisher, president of Lear's Chrysler division.
"South America is the proving ground for these kinds of things," he says. "If it works, maybe they take it north."
And elsewhere in Brazil the supplier is staking out portions of plant floors as it gets ready to put together interior modules for other automakers right in their buildings.
The most likely next arena in which Lear may realize the goal of one modular interior also will be in South America, probably in Venezuela, says Mr. Fisher.
Tenneco Automotive Inc.
The Walker exhaust operation at Tenneco's plant in Mogi Mirim is among the most efficient in the company and just keeps getting better, explains Scott Buehrer, director of Tenneco's Chrysler business unit.
The company changes the configuration so often that all the machines are on wheels, and electric and hydraulic connections drop from fixtures in the ceiling. Even the space where the exhaust operations are located was cleared out using numerous kaizen blitzes to streamline a former parts operation. The exhaust parts go to Chrysler, VW, GM and others throughout Brazil.
Meritor Automotive Inc.
Meritor's biggest innovation for the Brazilian market is not for the Dakota project. The supplier, formerly the automotive operations at Rockwell Corp., is not even a Tier 1 supplier for Chrysler. It's actually a Tier 3 making steel wheels that it sells to Goodyear Tire Co., which then puts on tires and sells it to Dana for the rolling chassis.
While the quality is amazing - mistakes running at only 1 part per million - it's not any more innovative than efficient mass marketing.
Where Meritor is trying new innovations is in door cartridge installations. The supplier is making door cartridges for several automakers in Brazil. In one project, for Skoda, Meritor actually is taking over assembly on the door line right in the plant.
Goodyear Tire Co.
Goodyear also operates in the lower tiers on the Dakota project and several other innovative automotive operations in Brazil.
The tire supplier is getting ready to build its first new plant in more than a decade in Brazil. The actual assembly and molding of tires will be done in a southern Brazilian city near Ford's Amazon project and GM's Blue Macaw in the state of Rio Grande del Sol. But the raw material will be produced in central Brazil where Goodyear has excess capacity in its Danbury presses and mixing equipment.
"It's the best way to use our assets," says one Goodyear executive.
In addition, it will be the first time Goodyear adds a tire-wheel assembly operation within a plant, combining wheels and tires and balancing them before delivery to various automakers. Goodyear already has a small tire-wheel assembly facility near the Dakota plant that supplies Dana, but the new plant will be the first of its kind for the supplier.
To better understand Ford Motor Co.'s Amazon project, scheduled to be in operation sometime in 2001 in Brazil, you have to go back to the genesis of the automotive assembly system. What did the Dodge brothers and Fisher Body provide the automotive industry? Major modules. This allowed automakers to focus on assembly and maintaining the more critical elements in a factory, such as the paint shop and powertrains.
Fast forward to the 1990s and more modern modular plant concepts such as Ford's Amazon and General Motors Corp.'s Blue Macaw now are at center stage. Some have called the programs radical, but James Padilla, recently appointed president of Ford South American Operations, says Amazon is only a different way of mixing the elements.
"It is going to unlock a lot more creativity in the total value stream," says Mr. Padilla. "I think our suppliers have a lot of capability to deliver innovative approaches in a much more cost-effective manner and we plan to take advantage of it."
Unlike Volkswagen AG's plant in Brazil, where suppliers share space with the German automaker, Ford's innovative new factory will not have suppliers putting parts on cars, Mr. Padilla says.
"Others have tried that and have had more or less success, depending on the execution," says Mr. Padilla. "(Suppliers) will be on the site in a very intimate way. They will be integral with our operations. Now, will they be on the same shop floor? Our concept does not say they will be putting parts on the car. What we would like to do is clearly define roles and responsibilities. I think where some of the things have failed is when you haven't really clarified roles and responsibilities."
Instead, materials and some 25 modules will enter the plant from several sides and be assembled in a three-shift operation running six days a week.
Also a departure from today's current relationship, Amazon suppliers will be given more latitude to provide more input on the design of the product. Ford typically specifies a part and suppliers deliver. Instead, Ford will give suppliers a generic specification of the company's system and then it's up to suppliers to deliver. Ford benefits because the company no longer has to try and be an expert on, say, plated plastics used on a switch or button. Suppliers gain because products can be designed to better fit their own manufacturing operations.
"We are going to delegate things to world class suppliers who have demonstrated capability, not only in Brazil, but in other parts of the world, and we are going to partner with them. It is a different way of doing business," says Mr. Padilla.
Ford plans to spend at least $1 billion on Amazon. The automaker has construction equipment on standby waiting for state clearance to begin work on the plant in the city of Guaiba, Mr. Padilla says. By 2001, the factory will be in the early launch phase of a new microvan and car, both based off an all-new C153 Fiesta platform. Amazon is expected to produce about 88,000 microvans and 90,000 cars annually.
Pieces of what Ford learns from Amazon eventually will make their way into Ford factories around the world, Mr. Padilla says.
"There are no cookie cutters in the business we are in, but there are ways you can adapt your approach to a specific circumstance," he says. "Let common sense prevail; that is the most important thing in all of this stuff. This is not a mechanistic thing. This is a people thing. Unless the people believe in it and feel they have the ability to influence and change it, you are not necessarily going to make the headway you need. But if you can get them to embrace it, it will work."
Mr. Padilla points to Ford's Wayne, MI, assembly plant as one example. Elements of what Ford learned from Mazda Motor Corp. have made their way into how Escorts are assembled there. But workers don't look at it as being Mazda's way, but the Wayne Assembly way, Mr. Padilla says.
"You go out and talk to (UAW Local 900 President) Jeff Washington about a modern operating agreement. Hell, it is his modern operating agreement. That is the way we want it."
About the Author
You May Also Like