Powder Metal Use Continues to Grow in '02
Applications on several key new engine and transmission programs will increase the use of powder metal parts by 4% in the '02 model year, representing a gain of 1.5 lbs. (0.7kg) per vehicle over last model year, according to industry estimates. For instance, the trade paper American Metal Market says automatic four-speed rear-wheel drive transmissions on the new Chrysler fullsize Dodge Ram pickups
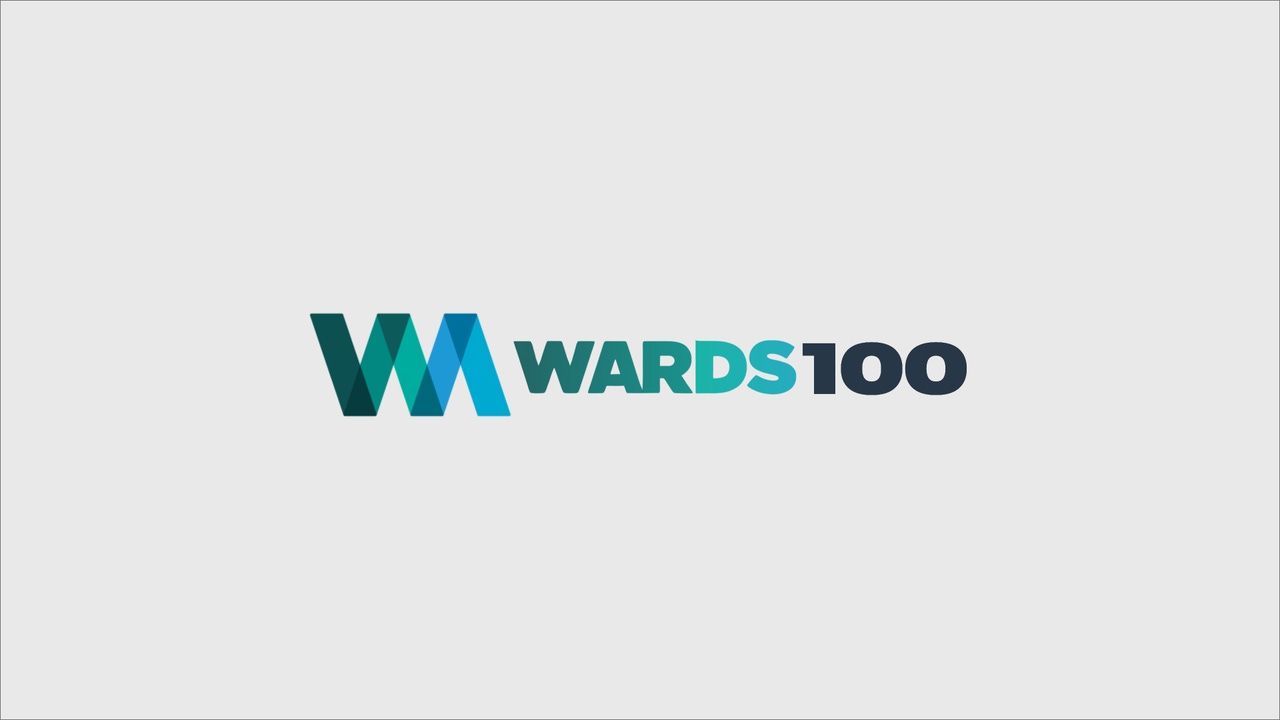
Applications on several key new engine and transmission programs will increase the use of powder metal parts by 4% in the '02 model year, representing a gain of 1.5 lbs. (0.7kg) per vehicle over last model year, according to industry estimates.
For instance, the trade paper American Metal Market says automatic four-speed rear-wheel drive transmissions on the new Chrysler fullsize Dodge Ram pickups and the new Jeep Liberty sport/utility vehicle (SUV) use a number of new P/M components, including clutch plates, oil pumps and chain drive sprockets.
General Motors Corp. also is ramping up production of its new Vortec inline truck family engines and is expected to add a 3.6L I-6 or a 3L I-5, joining the 4.2L I-6 currently used in its midsize SUVs, the Chevy Trailblazer, Olds Bravada and GMC Envoy. All of the engines in the new family will be equipped with P/M connecting rods, main bearing caps, cam bearing caps and numerous smaller components. The 4.2L I-6s use nearly 30 lbs. (14 kg) of P/M parts per engine, a record high for I-6s built in North America, AMM says.
Although its growth has slowed somewhat recently, P/M remains one of the fastest growing automotive materials on a content-per-vehicle basis. Use has soared in the past 10 years, from 23.5 lbs. (11 kg) per vehicle in 1991 to 39 lbs. (18 kg) in the '02 model year. That's a faster growth rate than plastics, aluminum, and most other automotive materials, points out Donald G. White, executive director of the Metal Powder Industries Federation.
Powder metals are attractive to automakers because they are metals that can be formed into intricate parts almost like plastics. The P/M process allows manufacturers to cut costs on critical parts such as sprockets and gears by eliminating expensive machining operations that would be required for conventional metal parts. P/M now is used extensively for parts such as connecting rods, sprockets and gears, and a growing range of other parts.
Chrysler's 2.7L V-6 engine contains 88 P/M parts and General Motors Corp.'s new 4.2L Vortec I-6 truck engine uses 79 P/M parts, says Mr. White.
Despite the growing list of new applications, Mr. White says the P/M industry — which is more reliant on automotive than most other material groups — is suffering from slowing production volumes at the U.S. Big Three automakers. It also is becoming increasingly concerned about the growing popularity of gasoline-electric hybrid and other types of alternative powertrains, which use far fewer P/M parts than traditional internal combustion engines. “As an industry, we must push for a strong seat at the hybrid vehicle materials selection table,” he says.
Mr. White says key growth areas for P/M parts include stainless steel exhaust parts such as flanges and sensor bosses, especially flange applications in the hot end of the exhaust system, from the catalytic converter to the engine manifold.
He also expects the use of P/M planetary gear carriers in automatic transmissions to increase substantially in the future, because they offer reduced assembly weight, increased durability and near-net-shape processing.
The metal injection molding (MIM) business, which allows metal parts to be injection molded just like plastics, is another bright spot on the industry's horizon, Mr. White says. In automotive, MIM competes against cold forging, screw machining, investment casting and die casting. MIM automotive applications include a solenoid actuator for interlock shift mechanisms, intricate air bag parts and sunroof stop cams.
Other key new applications, according to AMM and other industry sources:
Connecting rods and main bearing caps on an upcoming 5.7L V-8 engine with hemispherical combustion chambers for heavy-duty versions of Ram pickups.
Connecting rods and bearing caps on GM's third-generation Vortec V-8 truck engines. The 4.8L, 5.3L and 6L V-8s contain an estimated 28 lbs. (13 kg) of P/M components.
Planetary gear carrier assemblies on GM's 4L60E four-speed automatic transmission, which now is being used on the '02 Avalanche and redesigned Cadillac Escalade.
Connecting rods and other parts on Ford Motor Co.'s new 1.8L, 2.0L, 2.3L, and 2.8L I-4 engines.
Connecting rods on the Ford Thunderbird V-8 engine and hubs, gears, plates and sprockets in its 5-speed automatic transmission.
Main bearing caps on Honda's Anna, OH-built V-6 engines.
Flanges at the hot end of the exhaust systems of '02 Cadillac Escalade and Avalanche models.
DaimlerChrysler 2.7L Engine
Connecting Rods | 6 |
---|---|
Main Bearing Caps | 4 |
Crankshaft Sprocket | 1 |
Camshaft Sprockets | 4 |
Valve Seats | 24 |
Valve Guides | 24 |
Aluminum Cam Caps | 24 |
Water Pump Pulley | 1 |
88 P/M parts | |
GM Vortec 4.2L | |
Connecting Rods | 6 |
Main Bearing Caps | 7 |
Valve Seats | 24 |
Valve Guides | 24 |
Aluminum Cam Caps | 14 |
Oil Pump Gear Set | 1 |
Crankshaft Sprocket | 1 |
Camshaft Sprocket | 1 |
Aluminum Air Cover Plate | 1 |
79 P/M parts |
About the Author
You May Also Like