Productivity Soared for Most Manufacturers
Toyota was the most efficient vehicle producer in North America and Chrysler Group was the most improved in annual Harbour Report.
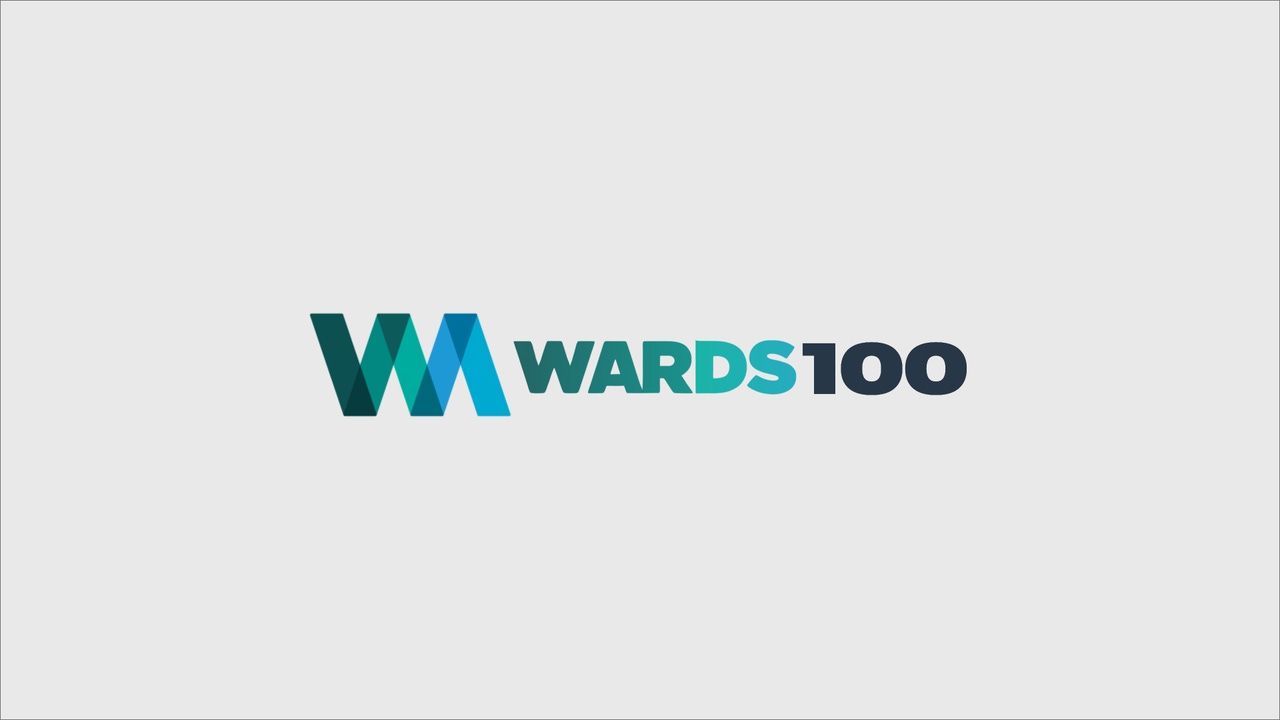
Overall, productivity was soaring in 2005. Toyota Motor Corp. was the most efficient vehicle producer in North America, Chrysler Group was the most improved and almost every major manufacturer managed to squeeze out some year-over-year productivity improvements despite falling volumes, according to Ron Harbour, president of Harbour Consulting Inc.
Revealing the results of the Harbour Report North America 2005, a measurement of the productivity of North American vehicle manufacturers during the previous year, Harbour said the improvements logged by the Big Three – during a year of slowing production and decreasing market share – showed manufacturing no longer was Detroit’s Achilles’ heel.
Toyota’s superior overall efficiency, which jumped 5.5% in 2004 (in the operations that participated in the study), still amounted to a $350 to $500 per vehicle cost advantage relative to General Motors Corp., Ford Motor Co. and Chrysler, he said, but falling revenue per vehicle had become the root of Detroit’s profitability problems, not manufacturing efficiency.
Even though GM was making lots of expensive vehicles, from Cadillac Escalades to highly optioned Chevy Suburban SUVs and large pickups, the average transaction price for a GM vehicle was a mere $20,659, Harbour said, far below its major competitors in North America and almost $6,000 less than the average price of a Toyota.
When Harbour started ranking labor efficiency in 1990, there was a huge gulf between the productivity numbers of Japanese auto makers compared with those in Detroit. But by 2005 there was little more than nine labor hours per unit between the best (Toyota) and least efficient (Ford) manufacturer for all their operations.
Nissan Motor Co. Ltd.’s new plant in Canton, MS – which had widely publicized quality problems – did not participate in the study, nor did the auto maker’s operations in Mexico. Honda’s Alliston No.1, Alabama and Mexico plants also did not participate, nor did Toyota’s assembly plants in Princeton, Ind., and Cambridge, Ont., Canada.
Harbour said GM was the auto maker that improved its efficiency most over the previous five years and had the best-established Toyota-style lean manufacturing methods of the Big Three.
But he also gave Chrysler kudos for quickly moving up the rankings. Thanks in part to a 9.5% leap in engine manufacturing productivity, the company improved its overall efficiency 19% since 2001 in assembly, stamping and powertrain operations, giving it the “most improved” title over the last three years.
Giving another example of GM’s manufacturing prowess, however, Harbour pointed out that GM’s Oshawa (No.1), Ont., Canada, plant was ranked the most efficient plant overall, with just 15.85 labor hours per vehicle (HPV), overtaking Nissan’s Altima assembly line in Smyrna, TN, which had won top honors more often than any other in the history of the study.
Nissan’s performance was hurt by the movement of some Altima production from Smyrna to the auto maker’s plant in Canton, MS, a spokesman said.
Oshawa’s achievement was stellar nonetheless, Harbour said, adding that four of the top 10 vehicle assembly plants belonged to GM.
In overall productivity, five of the six companies with assembly, stamping and powertrain operations in North America – Chrysler, Ford, GM, Honda and Toyota – showed improvement in 2004, led by Toyota’s gain.
Ford finished slightly ahead of Chrysler on assembly productivity (24.48 vs. 25.17 HPV). Ford also improved the labor productivity of its powertrain operations by 7%. Assembly productivity improved in nearly every Ford plant despite significantly lower production volumes, Harbour said.
In fact, five of the six participants in the engine portion of the study improved their engine manufacturing productivity.
In stamping, Toyota widened its lead, improving a whopping 28.3% to 1.37 stamping HPV and regaining its lead in press productivity with a record 775 average parts per hour.
“As in assembly, Toyota is separating itself from the rest of the industry,” Harbour said. “It is not a matter of spending more than its competitors. It reflects regular kaizen improvement activities and the flexibility that comes with well coordinated engineering and manufacturing.”
However, he said GM, Ford and Chrysler all have placed greater emphasis on metal stamping in recent years and have strategies in place to steadily improve efficiency.
“I think overall there were a lot of areas in this year’s report that we consider very positive,” summed up a Toyota spokesman, citing the 5.5% increase in productivity and the first place finishes of its Canadian stamping facility and West Virginia engine plant. However, in typical Toyota fashion he added: “Of course, we know we’ve got a long way to go to get where we want to be.”
It is Toyota’s conviction that it is always struggling, no matter how much money it has or how efficient it becomes, that keeps it on top, Harbour said.
Read more about:
2006About the Author
You May Also Like