The cloud over ChryslerThe cloud over Chrysler
Chrysler Corp.'s juggernaut appears to keep on rolling, like the Chicago Bulls on the way to the NBA title. First-quarter profit: $1 billion. Market share through April: 16.7%, highest since 1968. And a string of new-model styling hits.Shareholders are elated by the recent 17% dividend hike--the fifth increase in two years--followed by a 2-for-1 stock split. Life doesn't get much better.But nagging
June 1, 1996
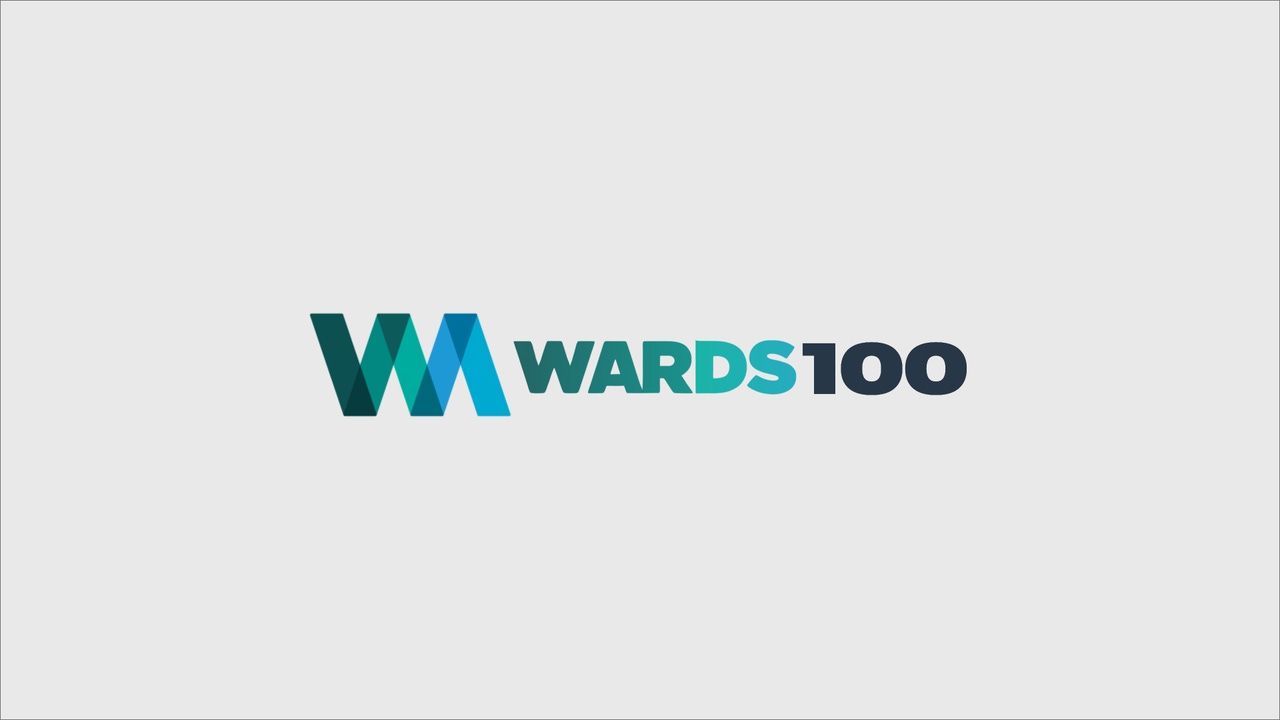
Chrysler Corp.'s juggernaut appears to keep on rolling, like the Chicago Bulls on the way to the NBA title. First-quarter profit: $1 billion. Market share through April: 16.7%, highest since 1968. And a string of new-model styling hits.
Shareholders are elated by the recent 17% dividend hike--the fifth increase in two years--followed by a 2-for-1 stock split. Life doesn't get much better.
But nagging quality questions, like the next unpredictable Dennis Rodman tantrum, remind the brain trust at Chrysler's Auburn Hills, MI, headquarters how delicate the chemistry of success can be. To its credit, Chrysler has moved beyond defensive spin-doctoring or punishing reporter, who raise the "Q" question.
Just ask Dennis Pawley, the cut-through-the-crap executive vice president for manufacturing. It's the system, stupid, he'll tell you. or, until recently at Chrysler, the lack of one.
"If (Toyota Chief Executive) Hiroshi Okuda and the half-dozen top executives from Toyota were on a plane coming over to benchmark Chrysler and the plane took a deep dive over the Pacific, what would happen?" Mr. Pawley asks. "They'd probably have a mourning service in a Shinto shrine somewhere. The next day the company would take off running just like it did the day before. I firmly believe that.
"It Bob Eaton, Bob Lutz (chairman and president, respectively) and myself and Francois Castaing and (Purchasing VP Thomas T.) Stallkamp and (Vice President of Product Design and International operations Thomas C.) Gale were going to Japan and the plane took a deep dive over the Pacific, what would happen to this company? I think the son of a bitch would dissolve."
Arrogant? Perhaps, but honest.
Chrysler's quality is getting better, but so is most everyone else's. on the latest J.D. Power and Associates Initial Quality Study, which measures any "problem" a customer notices in I the first 90 days of ownership , Chrysler's score is 1.28 problems per vehicle, down from 1.3 a year earlier. Ford Motor Co.'s and General Motors Corp.'s overall scores are 1.13 and 1.18 problems per vehicle, respectively. Toyota Motor Corp. remains the benchmark with only 0.77 defects per vehicle, but that's not quite as good as Toyota's 1995 score of 0.73.
Why does it matter when people want your product, your profit per vehicle leads the industry ($1,200 in the first-quarter) and your designs draw raves? Why not tell the nervous nellies and media hounds to go shove it?
It matters because no automaker can forever catch the wave of every market trend the way Chrysler has with its minivans, Jeep Grand Cherokee and Dodge Ram pickup.
It matters because the vast majority of its passenger cars look great, but aren't yet close enough to flawless to take sales away from Toyota and Honda.
And it matters because Consumer Reports tells its readers that in a recent road test of small sedans the Dodge Neon died on the road several times because of an electrical short.
"There are a number of their products in our current survey --Grand Cherokee and Concorde--that have shown steady improvement," says Robert Knoll, director of automotive testing for Consumer Reports and a long-ago Chrysler engineer. "It's too bad that people who buy those cars right after their introduction have as much trouble as they do."
As one of the first American managers hired at Mazda Motor Mfg. USA Inc.'s Flat Rock, MI, plant, Mr. Pawley understands the limits of how far a Japanese approach will work with American workers.
"Americans; you have to sell them and you need to explain why," Mr. Pawley says. "I've worked in a Japanese company. The manager is God, believe me."
Before he captures hearts and mind on the factory floor, Mr. Pawley is preaching his liturgy to those who report to him, who, in turn, teach it to those who report to them.
To reinforce how far Chrysler has yet to go, the course begins with two case studies.
The first is taken straight from the Harvard Business School. It focuses on Toyota's Georgetown, KY, plant, analyzing how management and team members solved a problem in May 1992, when cars were coming off the line with defective seats or no seats at all.
The second looks at a problem Chrysler experienced at its Bramalea, Ont., assembly plant with water leaks in the first two years of building the Dodge Intrepid, Chrysler Concorde and Eagle Vision.
In the Toyota system the plant's top two managers jump in as soon as the maximum eight cars end up in the reprocessing area. By talking with production workers who place seats into the body, they learn that a plastic hook protruding from the back of a rear seat bolster sometimes broke off. The bad news: the hooks were breaking less frequently. By the end of the first day they learn that it will cost the seat supplier $50,000 to solve the problem.
The plant's assembly manager files a report in which he takes full responsibility for the problem. He then tries to analyze ways to keep a similar defect from happening in the future.
The case doesn't say if or when the problem disappears, but managers and team members are confident they asked the right questions.
By contrast, the water leaks in Chrysler's LH cars were reported by dealers and customers shortly after the cars were introduced in 1992. By late 1993, the problem was occurring on 1,000 to 1,500 cars per shift per week, or at least 20% of the cars built.
Chrysler chose a typically American approach: form a committee. They even called it the Dry Car Committee.
The committee included members from body-in-white, paint and trim, and final lines. They met once a week, seeking root causes--variations in various processes--that caused the leaks. Their efforts paid off. Over the next six months the leaks per shift fell from an average of 800 to 139. But much of the improvement came by applying excessive amounts of sealer.
Meanwhile, although many of the appeared to be plugged, new leaks emerged. Finally, one day in mid-October a worker noticed an unusually large notch in the rear quarter panel.
Engineers from the paint and body shops met and looked at their process-control charts, but they found no sign of anything that might have caused the notch. They then consulted a stamping engineer and after an hour they discovered the defective subassembly that included the notch didn't match the sample on display at the end of the stamping line.
Aha! They had found the root cause.
After inspecting the die set used for the subassembly, they found a faulty punch that created the oversized notch. Workers in the stamping plant recast the die over the following weekend, but more than 500 cars already had been assembled with the defect. It took two weeks to go back and replace the flawed subassembly.
To prevent it all from happening again, the Dry Car Committee, after six months of weekly meetings, decided to conduct weekly maintenance on the stamping plant's 52 die sets so each one would be checked once a year. Finally they had a partial grip on this very costly glitch.
Did it have to take six months and untold thousands of dollars for overtime and extra sealant and using people to trouble-shoot problems that could have been corrected through a simpler process? Obviously not, in Mr. Pawley's vision.
But conditioning Chrysler's 85,000 hourly workers in the U.S. and Canada to rethink how they do their jobs is no simple feat. Many of them are new. Chrysler has hired 16,000 new workers since its 1993 agreements with the United Auto Workers and Canadian Auto Workers union, and more are on the way. Up to half of the current work force will be eligible to retire in the next five years. Therein lies an opportunity.
For the last two years, Chrysler has put its new hires through a rigorous screening, testing not only basic math and reading skills, but trying to measure their aptitude for problem-solving and working together in a team environment.
Historically, new hires would likely come from a list of referrals from both management and UAW members. That is beginning to change. After all, in Japan auto companies recruit production workers from only the top 20% of technical high school graduates.
"Yes, I want the sons and daughters and best friends of management and the UAW, because they understand what it takes to build good cars and trucks," Mr. Pawley says. "They've seen it in their families. They know this is a hard business, that they're not walking into a rose garden. But I want them only if our testing shows they have the right skill set."
To understand the "right skill set," it helps to visit the "learning line" at Chrysler's Jefferson North assembly plant in Detroit. This is where the principles of the new operating system translate from the theory to practice.
It's a tiny fraction of the entire plant, where about 4,200 workers crank out 1,175 Jeep Grand Cherokees per day. The area stretches perhaps 100 feet and encompasses eight work stations and about a dozen workers. There's a yellow and on cord for workers to pull when they notice a defect or can't finish their task in the allotted time. There are charts mapping how many times workers pulled the cord, how many minutes the line was stopped each day and how many parts were rejected as scrap.
At each work station there's a diagram illustrating how the worker should insert the window glass, attach the wiring harness or whatever the task may be. Next to the diagram, the steps for doing the job are listed in writing. This is the standard operating procedure. It is meant to economize on workers' movements, reducing both the risk of repetitive motion injuries and general fatigue.
None of these elements is unusual. Take a visit to almost any assembly plant these days and you're likely to see them in some form.
But they weren't programmed into Chrysler's operations until the beginning of this year, and even then only incrementally.
Learning-line workers are grouped into teams of 10 to 12 under the leadership of a team coordinator. Team members elect their coordinator once a year under the local labor agreement at Jefferson North.
Steve Lynn, 26, is one of the team coordinators at the facility's learning line. The company hired him three years ago. Before that, he worked at a dealership handling parts orders.
"The whole idea is that any problem gets fixed within the work station before it goes down the line," Mr. Lynn says. "As soon as someone pulls the cord, I go over and try to help. It's usually pulled a couple of times a day. We know if it's never pulled, then there must be a problem."
If there is a recurring problem, team members leave a note on the communication board for the next shift, explaining what happened and how they handled it.
Ideally, they also are supposed to rewrite the standard operating procedure if they find a quicker, easier way to complete a job. But none of his colleagues has revised an SOP since the learning line began in January, says Mr. Lynn.
Still, the andon cords and charts draw attention from other workers who wonder when this experiment will expand into their work areas. That will not be up to them, says Mr. Pawley. "They are not allowed to move outside the learning line until a vice president who has responsibility for the area goes in and says, `OK, you've mastered it, and you can spread it to the next 10 operations,'" he says.
So far, the UAW is reserving judgment on the effort. says Walter Harris, shop chairman of UAW Local 7. Union leaders have taken part in classroom training, but are watching the impact on employment.
"We have not bought in entirely," says Mr. Harris. "Based on the feedback from our members, it appears to be positive. but some of lower management; needs to learn to walk the talk." "
Indeed, those expecting instant results will be disappointed. In the recent J.D. Power survey, Grand Cherokee's number of increased marginally to 1.27 from 1.11 in 1995, a change that Mr. Harris attributes to several factors, including a faster line speed, more than a year of three shifts and the introduction of hundreds of new workers.
Don't expect Mr. Pawley to abandon his system because of a statistical blip like that, at least not when Chrysler is selling 20,000 Grand Cherokees a month.
"Look. when Taiichi Ohno began what is now the Toyota Production System, he knew that the process would have to change constantly, and 40 years later it is," Mr. Pawley says. "When I die, I hope they put on my tombstone: Denny Pawley--He was the Dr Ohno of Chrysler Corp."
Measuring automotive quality V has become a growth industry itself, but the proliferation of studies may be adding more confusion than clarity.
Chrysler Corp. scores better than last year, but slightly below the industry average, on Power and Associates' just-released Initial Quality Study. Yet in Strategic Vision Inc.'s "Best Loved Cars and Trucks" study, Dodge Intrepid, Chrysler Town & Country, Jeep Grand Cherokee and the Dodge Ram pickup capture the top spots in their respective categories.
What gives?
Cynics might note that a pair of retired Chrysler public relations staffers arranged Strategic Vision's Detroit press conference. But each study employs its own methodology. Power asks customers to list anything they didn't like about their new vehicle during the first 90 days of driving.
It's very subjective. Don't like the layout of the radio controls? That's one problem. The transmission slips? That's a real problem. In the Power study, the two count the same.
Darrell Edwards, president of San Diego-based Strategic Vision, says his research elicits what people like about their vehicles.
"When you only look at things they don't like, that whole factor is shrinking to somewhere between 0 and 0.1 problems per vehicle. At that point, it doesn't have any power to explain a person's experience," Mr. Edwards says.
Then there's the demographic factor. Younger buyers, especially in certain model segments such as midsize sedans, are harder to please than older buyers.
"Just look at our best Power scores: They were on LHS (0.75 problems per vehicle) and New Yorker (0.67)," says Rex L. Franson, Chrysler vice president of quality, capacity and process management. "Ten years less age (on the buyer) means about 0.2 more things gone wrong per vehicle."
Perhaps the best measure is warranty costs, a figure each company hides by lumping it in with dealer allowances, rebates and other incentives.
"Yes, Chrysler has a ways to go on quality," says Walter Norris, owner of Livonia (Ml) Chrysler-Plymouth. "The warranty dollars spent by the corporation with us are down from the past. They are still reasonably high, but they've made great gains."
Mr. Franson oversees a budget of about $100 million from which Chrysler can draw to implement quality-enhancing changes to its manufacturing process.
It might include torque wrenches with more precise performance or testing equipment used to verify the symmetry of a vehicle when it comes off the line. More recently Chrysler bought higher-intensity lighting for its Sterling Heights assembly plant to make sure interior colors are more consistent on the Dodge Stratus, Chrysler Cirrus and Plymouth Breeze.
"Most of it is pretty boring stuff," says Mr. Franson. "We talk about the analogy of the decathlon. In order to be Bruce Jenner, you don't have to win every event, you just have to place highly in each one. We will not spend ourselves into defect-free oblivion."
TOWSON, MD -- With the exception of a few vocal shareholders concerned about product quality and pricing, the atmosphere surrounding Chrysler Corp.'s annual meeting can best be described as triumphant.
With the takeover attempt by Kirk Kerkorian a thing of the past, Chairman Robert J. Eaton delighted stockholders with a two-for-one stock split of Chrysler's common stock and a 10 cent increase in the quarterly dividend, from 60 cents to 70 cents.
"(The stock split) reflects our confidence in the company's continued prospects for strong earnings growth," beams Mr. Eaton. "Our stock is trading at near-record levels, and this represents an opportunity to further increase shareholder value."
He says the dividend increase, the highest in the company' history, means that Chrysler has raised its dividends by 360% since December 1993. "It also means that our dividend yield of 4.3% is the top quartile of the S&P 500," adds the chairman.
Icing on the cake for Mr. Eaton is his proclamation that during the course of the meeting the company's stock price rose 1 5/8.
Questioning by stockholders about Chrysler's quality problems prompts Mr. Eaton to echo segments of his address to them. "Quality is our number-one concern," he says. "Our quality continues to improve every year. And we did have our problems."
Mr. Eaton emphasized that foreign markets represent the company's best opportunity for growth. "Our goal is 20% growth per year, but in 1995, we were up almost 30%," he stated. "About 40% of our Jeep production from our Toledo, OH, plant is now going overseas."
Although Chrysler had earlier announced the end of the Eagle Summit sedan and wagon, fueling speculation that the division's day are numbered, Mr. Eaton says in Towson that a new Eagle product is due in 16 to 18 months. And despite the apparent schism between Chrysler and Mitsubishi Motors Corp., Mr. Eaton says the two automakers will continue their technical exchange.
In an effort to keep the focus on automaking, Mr. Eaton says, "We expect to complete the sale of most of our aerospace business later this year. We agreed to sell it because we don't want anything to take our attention away from our core business."
Other actions included:
* The re-election of directors Lilian H. Affinito, James D. Alijian, Robert E. Allen, Joseph A. Clifano Jr., Thomas G. Denomme, Mr. Eaton, Earl G. Graves, Kent Kresa, Robert J. Lanigan, Robert A. Lutz, Peter A. Magowan, John B. Neff, Malcolm T. Stamper and Lynton R. Wilson.
* Amendment of compensation for the 11 non-employee directors from between $25,000 and $37,000 to the equivalent in shares of the company.
About the Author
You May Also Like