Repair Shops Turn to Technology to Combat Disruption, Drive ScaleRepair Shops Turn to Technology to Combat Disruption, Drive Scale
With growing labor shortages and increased demand for vehicle repairs, shops need to consider increasing their use of technology systems to keep up with repair cycles.
May 9, 2022
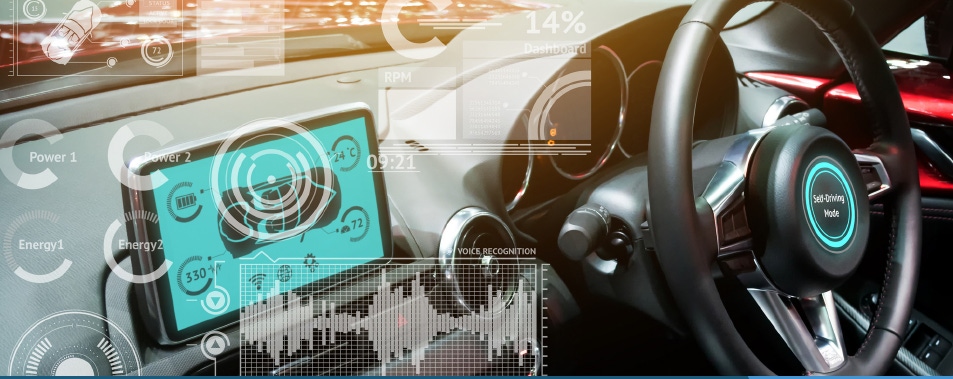
The vehicle repair industry is booming.
A shift in daily driving patterns has led to an influx in the frequency and severity of accidents across the country, and while business is up for collision repairers, it’s also a cause for concern. Labor shortages have been ravaging almost every industry in the U.S., and vehicle repairers are no different. In fact, according to the Bureau of Labor Statistics, we could see a 4% decline in employment in the auto-technician field through 2029.
In an already aging field where 30% more employees are aged 55 and older , these numbers can seem alarming.
The growing complexity of vehicles also has challenged repair shops. Advanced driver-assistance systems, including features such as backup cameras, automatic emergency braking and more, have become more prevalent and advanced over the years, requiring new tools and expertise to repair. With so many new systems to learn for different vehicle makes and models, it can be hard for shops to keep up.
To keep pace with innovation, more repairers are turning to technology to power their knowledge, drive efficiency, scale up operations and redefine the customer experience. As repair demands threaten to surpass capacity, automated systems can help with cumbersome tasks to keep repair cycle times in check while satisfying consumer demands throughout the process.
To enhance efficiency and the overall customer experience, repairers need to identify gaps in the business. Is cycle time increasing due to staff shortages? Are estimates taking longer than usual? If so, technology can aid in streamlining operations.
Adapting to Repair Complexity
As vehicle technology becomes more complex, so does the process of identifying needed repairs and parts. AI photo-estimating tools can jumpstart the estimating process, allowing estimators to spend less time on non-value-added tasks and more on providing a differentiated customer experience. AI integrated into the repair process can prepopulate predicated repair lines on the estimate, leaving the pros to approve and accept these line items, speeding the process of estimate writing. The time spent preparing estimates can be reduced through assistance from AI.
Diagnostics and calibration tools also have become essential as newer vehicles include an ever-increasing number of sensors, cameras and lidar. Recent data shows that from 2017 to 2021, the percent of appraisals including a line entry denoting a “scan/diagnosis/health check” operation grew from less than 5% to over 48.9%.
By another measure, nearly 16% of all repairable appraisals included a repair or replacement of nearly two camera, radar or sensor parts by Q4 2021. Historically, diagnostics scanning tools functioned outside of a repairer’s workflow, making them cumbersome to use. But as vehicle technology advances, so do the tools for repairers; today’s cloud-based diagnostics technology can integrate into existing workflows and attach scan results directly to repair-work files to improve accuracy and efficiency.
With so much new technology embedded within the vehicles themselves and in the increasingly complex repair process, effective training becomes even more crucial for technicians. The Inter-Industry Conference on Auto Collision Repair (I-CAR) delivers best-in-class training, helping technicians keep pace with vehicle and repair technology and procedures.
Keeping Pace With Growing Demand
As demand for repairs grows, shops can gain efficiencies by letting technology do the administrative work. Today’s communication platforms can automate repair status updates with your customers and capture their feedback post-repair to drive further improvements in the shop. Electronic parts ordering not only can speed up parts acquisition, it also can accelerate and streamline invoice reconciliation within a shop’s billing system. Digital payments can save shops, customers and insurers even more time while capturing more data within digital workflows.
Enhancing the Customer Experience
Recent data shows repair shops using repair management technology decreased cycle time on average by eight hours. A decrease in cycle time can lead to an increase in positive customer experience. Yet speeding up cycle time is just one aspect of the customer experience; repair shops should be thinking about how they can create an exceptional customer experience end-to-end. Photo-estimating technology can accelerate the intake process, allowing customers to capture damage photos for a near real-time assessment and cost estimate within minutes post-accident. Adopting digital tools for customers to book appointments, check in and receive automated repair updates can increase convenience and drive satisfaction.
Mark Fincher_Headshot
Thriving in a Challenging Era for the IndustryVehicle technology and personal mobility preferences have changed everything, making nearly every repair more complex. This trend toward complexity will only grow as vehicle and repair technology advances and customer behavior evolves. Yet despite this industry’s surmounting challenges, repairers are poised to thrive. By staying agile to the changes and making smart investments in technology to improve operations, repairers can adapt to the growing complexity while still delivering exceptional service.
Mark Fincher (pictured, above left) is vice president-automotive services market solutions for CCC Intelligent Solutions.
About the Author
You May Also Like