What to do before starting that new building projectWhat to do before starting that new building project
Any dealer who has ever built a new store or remodeled an existing facility knows what a nightmare it can be. Land considerations, manufacturer guidelines, municipal codes and the customers themselves all must be factored into the new plan. If you plan your work, and work your plan, the project will proceed smoother, even though the best laid plans can encounter snags and imponderables. The plan should
May 1, 2001
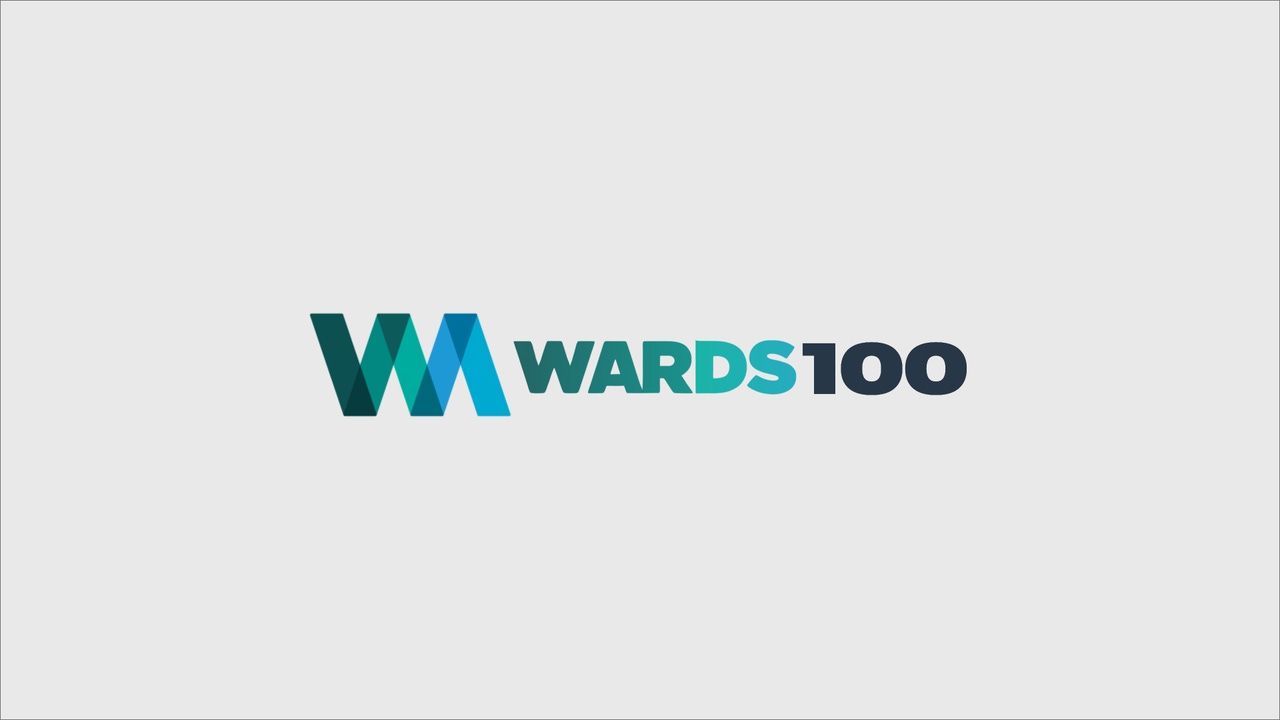
Any dealer who has ever built a new store or remodeled an existing facility knows what a nightmare it can be. Land considerations, manufacturer guidelines, municipal codes and the customers themselves all must be factored into the new plan.
If you plan your work, and work your plan, the project will proceed smoother, even though the best laid plans can encounter snags and imponderables.
The plan should be carefully drafted, relying on various experts in their fields, and also drawing on the dealer's own expertise, says Roger Berry of the Dallas-based dealership construction consulting firm that bears his name.
“A dealer needs to sit with a consultant before the planning begins to discuss the size of the facility he needs based on the market and projections and the size of the property he needs,” says Mr. Berry.
Most important is to engage a consultant who is specific to the automotive business, says Mr. Berry.
“Then get an architect and a construction company to take the consultant's plan and turn it into a workable blueprint that is up to the local codes,” he continues. “I usually advise the dealer to acquire more property than he needs to allow for future expansion.”
Remodeling projects are more difficult than a new build. Says Mr. Berry, “It's at least twice as difficult because you have so many limitations you have to live with.”
Other limitations are manufacturers' specifications on how they want dealerships representing their brands to look and feel. Many are very specific, including what materials to use and where to get it.
“You really have to rely on your architect,” says Mr. Berry. “Sometimes he can get you equivalent materials locally, perhaps not at a lower cost, but with lower shipping costs.”
Mr. Berry adds that dealers know their markets better than the manufacturers do and likely will adjust to factory guidelines.
“Dealers should take the manufacturers' specifications and combine them with what the they knows they want and need.”
12 REMODELING TIPS
Use metal hallide lighting supplemented by fluorescent lighting over work areas in the service department.
Consider shielded fluorescent “bright stick” type drop lights.
Use “stone hard” Park Avenue material for shop floors.
Install overhead fans for shop circulation.
In warm climates, utilize thermostat controlled roof vents in shop and parts departments.
In hot and dry climates, “swamp coolers” should be considered.
Reception areas could use infrared heating in cold climates.
Install overhead electric door controls that can be operated by drivers of a car.
Interlock overhead doors electrically in areas that might create a wind-tunnel effect. It can be switched off during the summer.
Investigate waste oil furnace for supplemental heating.
Install a bridge crane with electric or air chain lift for transferring parts to second floor storage.
Keep shop ceilings as low as possible.
Source: R.G. Berry & Assoc.
Read more about:
2001About the Author
You May Also Like