Wrong Answer Is RightWrong Answer Is Right
When placing stock replenishment orders, parts managers should strive for level ordering as much as possible.
January 1, 2007
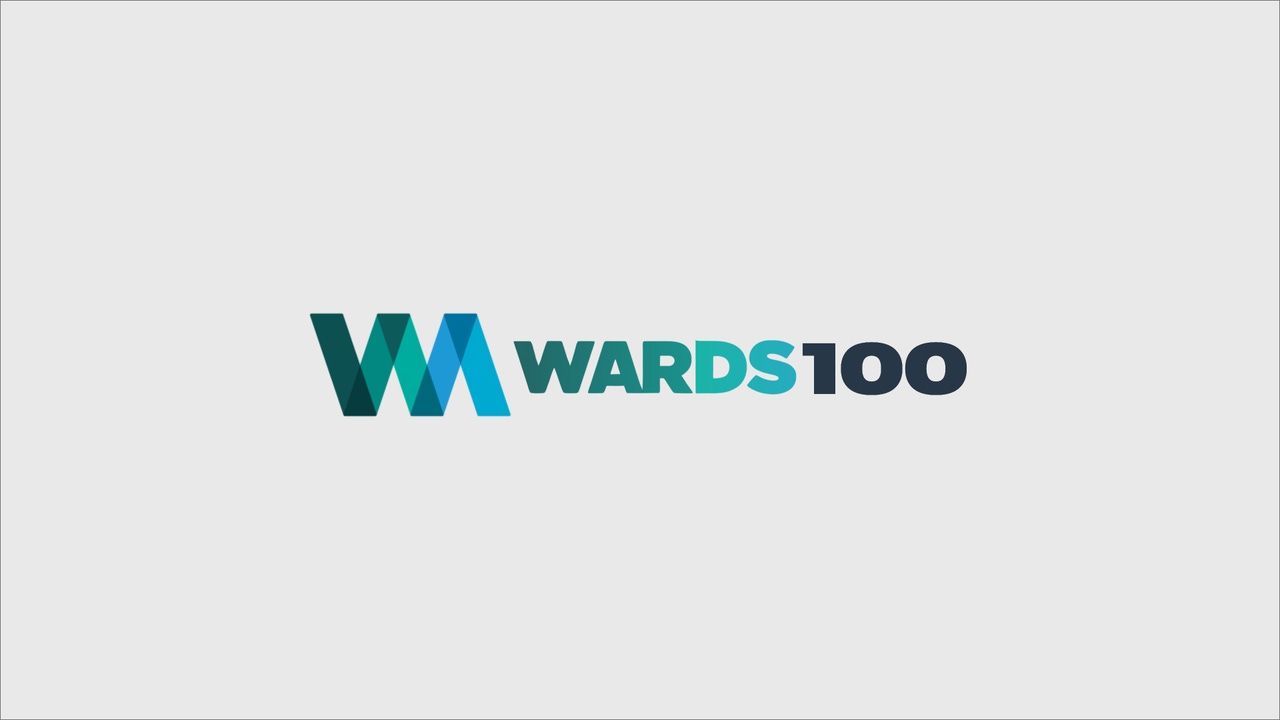
When placing stock replenishment orders, parts managers should strive for “level ordering” as much as possible.
Level ordering means the parts manager is ordering consistently with every order placed, eliminating the potential of having larger orders placed at one point as opposed to another in a given month.
Doing so will help replenishment orders more closely match customer demands filled from the stocked inventory. It also can reduce the possibility of excess inventory.
Unfortunately, several things can impair a parts manager's ability to achieve level and stabilized ordering when placing daily stock orders (as most manufacturers now allow their dealers to do).
A potential impairment is the type of dealer management system a dealership uses. If it happens to be ADP, and “weighted averaging” is used for stock order calculation, how the parts manager responds to certain standard questions when running a new stock order, can determine whether level ordering is possible.
In particular, I'm referring to two specific questions that come up when the parts manager runs function “STK,” the routine used for creating new stock orders. The questions are: “How many business days this month?” and “Which business day is this?”
Logic would suggest that each question is answered specifically. For example, if it is a month with 30 days and it is the fifth day of the month you answer the questions accordingly. Likewise, if it's the same 30-day month and it's the 24th day of the month you again answer with the actual periods. With weekly stock orders, it is okay to use the system as designed.
But when placing daily stock orders, the answers to these questions can cause problems. In the daily stock order environment, using the actual monthly periods when answering the questions causes a suggested increase in inventory levels at the beginning of the month and a suggested decrease in inventory levels for the end of the month.
In essence, the parts manager actually is changing the weight of previous months sales. Remember: the system uses prior sales, actual and lost, to predict what must be reordered. That can significant affect maintaining a stocking level relative to customer demand.
So, if it is not a good idea to answer the two aforementioned questions with actual periods when calculating new stock orders for daily submission, what should the parts manager do?
Here are my recommendations.
Answer “30” for “How many business days this month?” Answer 15 for “Which business day is this?” These answers will result in an approximate 50% weight.
Then — to ensure that your stock levels are optimized as best as possible to customer demand — monitor and track shop fill rate and actual inventory levels relative to user-defined dealer management system BSL (Best Stocking Level) and manipulate the excess buy up or down as necessary to attain the best possible inventory level.
Another suggestion — depending on your customer demands and market — is to add, at the middle of the month, a couple days to the question, “Which business day is this?” For example, use 16 or 17. The parts manager may find this suggestion will help to better maintain the correct stocking level of fast moving parts.
Does this work? Absolutely! During my years as a working parts manager, I did it with good results.
Again, it is important to monitor fill rates and inventory response to customer demands and to make necessary setting corrections or DMS adjustments. I've recommended these responses to parts managers for a long time now. The feedback has been positive.
Gary Naples is a parts consultant to dealers and manufacturers. He's authored two books on parts management. He's at 570-824-1528/[email protected].
Read more about:
2007About the Author
You May Also Like