McKinsey: Electronics Need to Become Core Competency
As the gizmo-driven fever generated by Convergence 2004 hits the auto industry full steam this week, at least one top management consulting firm is advocating a degree of cold calculation in the introduction of innovation. “Let’s be very clear, this is a little bit of a revolution we (in the auto industry) are going through,” says Stefan Knupfer, McKinsey and Co.’s leader-North American automotive
October 18, 2004
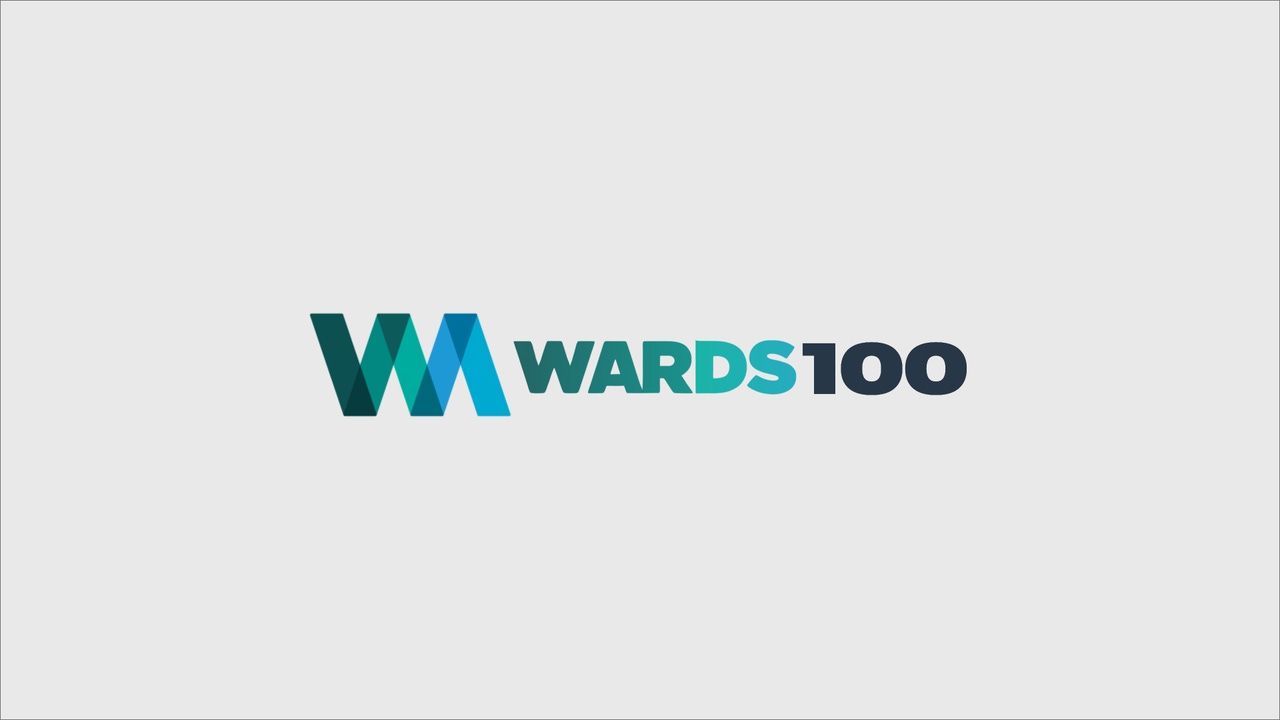
As the gizmo-driven fever generated by Convergence 2004 hits the auto industry full steam this week, at least one top management consulting firm is advocating a degree of cold calculation in the introduction of innovation.
“Let’s be very clear, this is a little bit of a revolution we (in the auto industry) are going through,” says Stefan Knupfer, McKinsey and Co.’s leader-North American automotive and assembly sector. Knupfer is co-author of the firm’s recent HAWK 2015: Knowledge-based Changes in the Value Chain.
Historically, “the car has been mainly a mechanical product,” he tells Ward’s on the eve of Detroit’s biennial auto electronics summit. “Now it becomes an electronic product, and it becomes about hardware and software.”
With sophisticated systems such as BMW’s iDrive, the share of electronics compared with vehicle cost is expected to more than triple by 2015.
The share of electronics compared with vehicle cost is expected to more than triple by 2015, with greater implementation of systems such as X-by-wire, infotainment and active safety.
McKinsey’s study, co-developed with the help of the Institute for Production Management, Technology, and Machine Tools (PTW) at Darmstadt University in Germany, estimates today’s typical small car contains nearly 70 control devices, with software eating up 2% of manufacturing costs, for example. By 2015, software’s share of the cost will jump to 7%.
While the cost burden will escalate, the potential for things gone wrong could follow right along – even as systems are applied on a wider basis.
The study cites German Automobile Club (ADAC) statistics estimating by 2015, 60% of all breakdowns will occur due to electronics and software hiccups.
That’s an 8% leap from today’s electronics breakdown rate in Germany, of which 32% are the result of infotainment and vehicle-electronics glitches; 20% stem from injection systems; 12% from vehicle controls and 8% come from the cooling system.
Two high-profile auto makers already have gained unwanted publicity because of the electronics challenge.
J.D. Power and Associates’ Initial Quality Survey routinely has in recent years marked down Mercedes-Benz for quality gaffes directly attributed to poorly running electronics systems.
BMW AG Chairman Helmut Panke shares the difficulties of his main competitor, recently telling Ward’s at a luncheon in Detroit that BMW’s biggest quality concern revolves around technological glitches.
When it became evident Mercedes was slipping, CEO Juergen Hubbert partially blamed a lack of focus, while Panke says the rate of innovation has in some cases outpaced the company’s readiness to deliver high quality.
Knupfer says auto makers, particularly Europeans who often lead the way in introducing electronics, don’t necessarily have to suffer from a quality gap.
“What’s much more important right now as you look at the (more-advanced) European market,” he says, is the fact “there is a gap between the complexity that goes into such a car and the capabilities in high-quality implementation.”
Says Knupfer: “If you have a luxury car that doesn’t move anymore because something electronic doesn’t work, then obviously it becomes a big deal.”
While auto makers and suppliers cannot stop the snowballing of electronic systems, especially as they grow increasingly integrated in, and responsible for, modern vehicle operations, Knupfer suggests the cost and quality problems aren’t inevitable for individual companies.
Knupfer’s solution: Make informed decisions about electronic systems early in the product-development process and be willing to hold off on a technology until it is mature and the market is ready.
In other words, auto makers need to do their homework on items once seen as emerging, pie-in-the-sky innovations.
“I think the more complexity you build with those new innovations in electronics, the more you need to be careful that you don’t get into a quality gap where you put more and more of those innovations into a car (without) your capabilities (being able to) keep up with this. You see a little bit of this right now in Europe, where a lot of the manufacturers do have quality issues.”
Knupfer says OEMs should focus more intently on electronics and create a value chain that is knowledge-based instead of one centered on business functions, which could realize a 20% productivity advantage, according to the HAWK study.
That productivity improvement is crucial, as escalating manufacturing costs are expected to far outpace sticker price inflation.
Suppliers play a major role in this transformation, as they currently hold much of the innovation knowledge OEMs are seeking.
The strength of supply-chain relationships becomes ever more important, for the sake of getting quality material and high-quality information.
In the process, however, OEMs need to make electronics a core competency, Knupfer says. Such systems would be developed with the same rigid focus devoted to powertrain development and safety.
Ford Motor Co. is one such auto maker that has publicly said it is taking this approach.
Chief Information Officer Marv Adams recently told Ward’s the auto maker has initiated a worldwide push to reign in electronics as a core competency.
About the Author
You May Also Like