Taiwanese Fastener Industry Eyes Slice of U.S.’s EV PieTaiwanese Fastener Industry Eyes Slice of U.S.’s EV Pie
EVs require fewer fasteners than their combustion-powered counterparts, but EV manufacturing involves new technical issues for which new fastener solutions are needed, and U.S. fastener experts are confident that Taiwanese suppliers can deliver those.
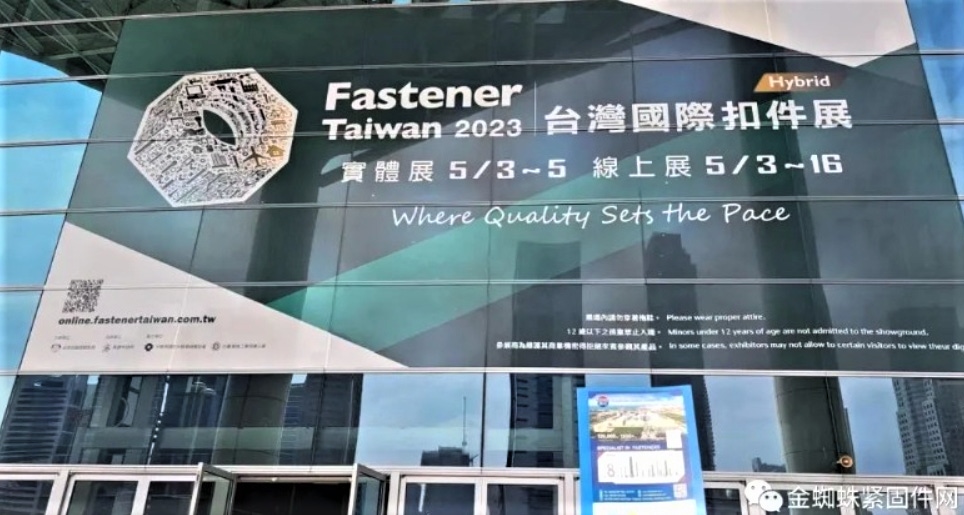
KAOHSIUNG, TAIWAN – Taiwan, the world’s second-largest fastener exporter by value after China, is positioning itself to be a main supplier of fasteners for the U.S. electric-vehicle sector, say participants at Fastener Taiwan 2023, a trade show held recently in this southern Taiwan city. https://www.fastenertaiwan.com.tw/en/index.html
Although EVs require fewer parts and fasteners than their combustion-powered counterparts, EV manufacturing involves several new technical issues for which new fastener solutions are needed. And U.S. fastener experts are confident that Taiwanese suppliers can deliver those.
“Electric-vehicle production serves as a major growth driver for fasteners in the U.S., as demand for lightweight fasteners grows,” Nick Ruetz, president of the U.S. National Fastener Distributors Assn., tells Wards at Fastener Taiwan 2023.
Fastener Taiwan thumb_0
“Taiwan and South Korea are the only two main Asian fastener exporters that are capable enough to serve the auto sector, with their defect rates being extremely low. For instance, we recently shipped in 10 million pieces from Taiwan without any defects,” Ruetz says.Tainan, Taiwan-based Boltun used the trade show to present its wide portfolio catering to applications spanning from electronics to trucks and even wind turbines. About 90% of Boltun’s output is destined for the automotive sector.
“Electronics companies shift away from the saturated laptop and smartphone markets to EVs, and to have those electronics installed in the EVs, the OEMs need the very small fasteners that we are able to supply,” says Jason Chen, sales director of Boltun.
“Another new EV-driven demand we are able to fulfill is the combination of lightweight aluminum structural elements with steel fasteners, which is a technically challenging task, given that connecting dissimilar metals can result in corrosion, requiring us to do special surface treatments, such as zinc-flake coatings, to enhance anti-corrosion features,” he says.
Similar upstream products are offered by Taipei-based Atotech Taiwan, a maker of specialty chemicals and auxiliary equipment for shaping electrolytic zinc, zinc alloy or post-machining passivate processes (techniques designed to reduce later corrosion of fasteners), The supplier has launched a “Zintek” inorganic silver zinc flake base coat, also designed to inhibit automotive fasteners from corroding.
Among the other ways to prevent corrosion between dissimilar metals is the use of patches at the screw head, as presented at Fastener Taiwan 2023 by Yangmei-based TSLG. The company also showcased screws treated with microcapsules that cushion the screws against vibration. When the external and internal threaded fasteners are locked together, the microcapsules are squeezed and then rupture, and the mixture of chemicals generates strong adhesion effect.
This growing market is reorienting how Taiwan fastener manufacturers work. Kaohsiung-based Sheh Fung Screws has been a major manufacturer of fasteners for the construction sector for decades and is now preparing to jump on the EV bandwagon. This involves an upgrade of the company’s technological abilities, including procuring machinery for special parts and hiring of special parts engineers.
“We will be facing fewer competitors in the auto sector than in the construction sector, but the upgrade to automotive takes considerable commitment, since virtually all fasteners used for the car structure are special parts that vary greatly between car models,” says Frank Lee, a Sheh Fung sales manager.
There are other challenges as well. For instance, one export director of a Kaohsiung-based automotive fastener maker, who asked not to be named, notes automotive OEMs are headed toward replacing carbon steel with low-carbon steel, which is in line with industry decarbonization efforts.
“But our main raw material source, (Kaohsiung-based) China Steel Corporation, has yet to develop 'green' steels,” the export director says.
Tainan-based JingFong Industry, a fastener manufacturer specializing in automotive self-locking nuts, says the immaturity of this market has caused some swings in sales. CEO Victor Kreng says an initial COVID-19 shock in the first half of 2020 caused a near-freeze of orders but was followed by a V-type rebound, with full order books recorded in the third quarter of 2020. That was followed by persistently high customer inventory, however.
“We are now seeing a completely new situation in which the OEMs ask Tier 1 suppliers to keep the inventory until the last moment, which translates into rush orders of small batches, which, of course, is bad for us,” says Kreng.
“We believe that this is mostly about the OEMs worrying about cash flow as a reflection of growing pressure from their shareholders.”
About the Author
You May Also Like