Gloomy Near-term Outlook for Steel Asia crisis, other woes hurt production,pricing
By most accounts the completion of Ispat International NV's purchase of Inland Steel Co. to become the world's seventh largest steelmaker in mid-July was a happy affair.After all, for a relatively modest $1.4 billion, Ispat gets the sixth largest U.S. steel producer, and a respected, relatively efficient one to boot. Ispat also gets I/N Tek, the 60% Inland-owned joint venture with Nippon Steel Corp.,
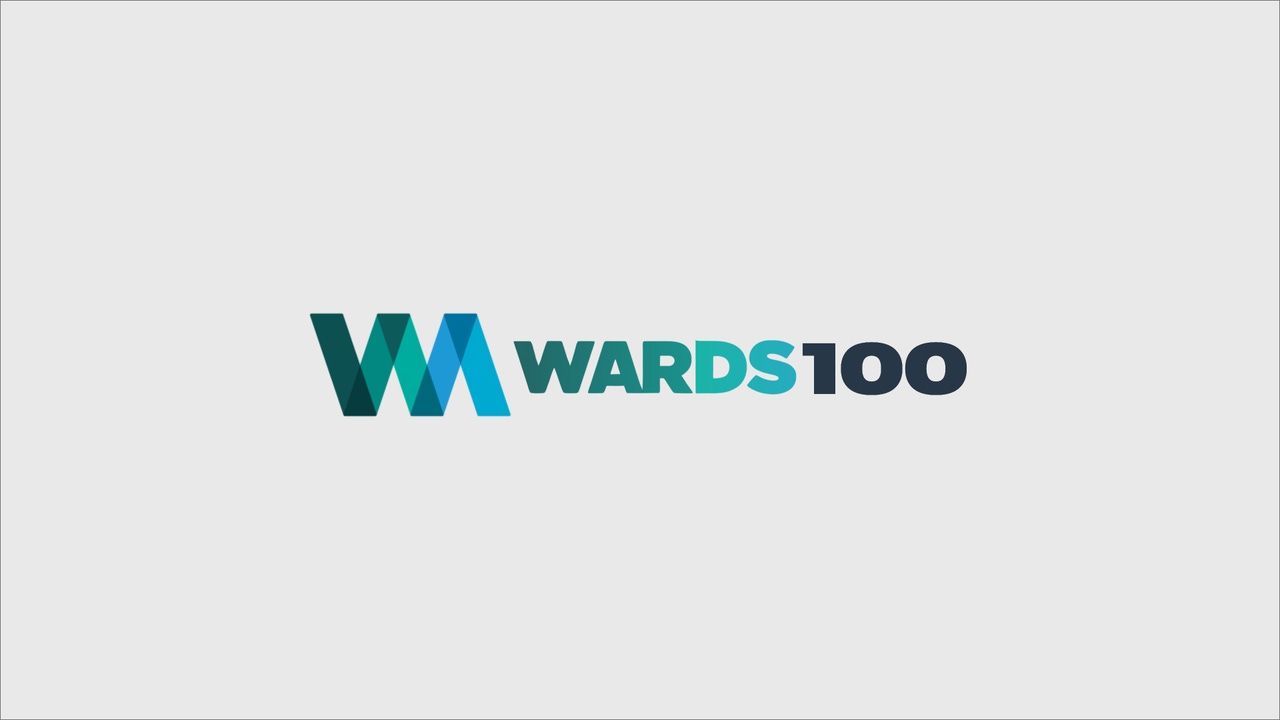
By most accounts the completion of Ispat International NV's purchase of Inland Steel Co. to become the world's seventh largest steelmaker in mid-July was a happy affair.
After all, for a relatively modest $1.4 billion, Ispat gets the sixth largest U.S. steel producer, and a respected, relatively efficient one to boot. Ispat also gets I/N Tek, the 60% Inland-owned joint venture with Nippon Steel Corp., and I/N Kote, the 50% Inland-owned JV with NSC. Both are high-tech steel finishing operations in Indiana.
Furthermore, Ispat has ambitious plans to boost production by more than 1 million tons per year and chop costs by $120 million annually during the next four to five years through global purchasing synergies.
The Ispat/Inland deal also is expected to spur a healthy round of consolidation in the steel industry.
But digging up a steel analyst with a rosy near-term outlook is about as hard to find as a bargain on an air conditioner in Dallas.
Continued economic weakness in Asia and the promise of increasing pricing pressure in the U.S. have many steel industry experts singing the blues.
Analysts at the investment bank Goldman Sachs say global demand for steel is likely to fall 0.7% in 1998 and grow only 2.6% in 1999, compared to 5% growth in 1997.
Steel demand in Asia is predicted to fall 4% in 1998, and Eastern Europe also is expected to be soft.
Two top steel experts speaking at a recent industry conference are even more downbeat. PaineWebber analysts Karlis M. Kirsis and Peter F. Marcus say the global steel industry is "on the verge" of its most severe cyclical decline since the mid 1980s. In a presentation that had some wondering if predictions of plagues and locusts also would be forthcoming, the analysts predicted "pricing is going to collapse in the United States, particularly in sheet products . . ."
They predicted worldwide steel consumption could drop 4% this year, with the Pacific Rim sinking 10%. The two analysts also said that U.S. producers are not cutting costs fast enough to stay competitive with other world producers.
With Asian prices "much lower than those in other regions" the global market is now facing "too much steel searching for a home," says Goldman Sachs.
Continued weakness in China's economy also has industry watchers worried because it is the world's biggest consumer of steel after the U.S.
The almost complete shutdown of GM's North American Operations - the steel industry's single biggest customer - also hurts.
Nevertheless, there are a few positive signs: South Korea-based Pohang Iron & Steel Co., the world's second largest steel producer, said that profit grew by a better-than-expected 26.5% in the first half this year because of higher domestic steel prices and foreign currency gains. Posco, as the state-owned company is known, won't be able to sustain the growth because of production cuts and slumping demand from Asian economies. Its costs already are rising as stocks of imported raw materials need to be replenished. Still, the company earned a surprising 687 billion won ($524 million) in the six months ended in June, up from 543 billion won ($414 million) a year earlier.
Also, demand in the U.S. - at least prior to the GM strike - was "higher than at any time during the past 30 years," Goldman Sachs says. Inventories in the U.S. also have been relatively low, and cheap Asian steel imports have been gaining ground more slowly than anticipated.
CCV Gets Second Plastic Supplier
As Chrysler Corp.'s plastic car development efforts start to heat up, Montell Polyolefins is putting out the word that a glass-reinforced version of its Hivalloy resin now is being seriously evaluated for use in the program.
Larry Oswald, executive engineer-advanced body engineering at Chrysler, says Ticona Corp., formerly known as Hoechst Technical Polymers, still has the inside track with its polyethylene terephthalate (PET) resin because of its longer tenure with the program and Chrysler engineers' familiarity with the material. However, Hivalloy is being added because the automaker doesn't want to be limited to evaluating only one plastic or one supplier for body material.
Montell officials say their Hivalloy engineering resin was still in development when Chrysler's Liberty program began testing over a dozen grades of plastics for the project in 1995 - and settled on Ticona's PET.
Although Hivalloy was submitted late, Chrysler and its molder, Cascade, soon found that the properties of Hivalloy came closest to the target specifications established by Chrysler engineers. Features that impressed Chrysler were Hivalloy's strength, weatherability, stiffness and impact resistance. The material also has good molding features, colors well on press and is cost-competitive, Montell says.
Chrysler engineers were impressed with how body panels made of Hivalloy maintained their resiliency throughout a demanding 200,000-mile durability test, showing no cracks or separations, says Montell.
But Mr. Oswald makes it clear that the testing is only beginning. Rigorous evaluations targeting repairability, crashability and other features are scheduled for late this year, extending into the first quarter of 1999. Some suppliers speculate Chrysler might decide on a possible production vehicle this year, but Mr. Oswald predicts it will be at least three model years before the company is confident enough in the technology to bring a product to market.
DSM Signs Technology Agreements
Netherlands-based DSM Performance Polymers, the fourth largest polypropylene producer in Europe, signs two separate technology licensing agreements for its Automotive Polymers business unit. With Mytex Polymers (Jeffersonville, IN), a joint venture between Exxon Chemical and Mitsubishi Chemical Corp., it inks an agreement to cross-license polypropylene compounding technology. A second agreement has been concluded with Japan Polychem Corp. (Tokyo), a joint venture between Mitsubishi Chemical Corp. and Tonen Chemical Corp.
The agreements will allow DSM to use the technologies for compounded polypropylene of Mytex polymers and Japan Polychem Corp. in Europe. The company's compounded polypropylene is used in bumpers, body moldings, interior trim, instrument panels and wheel well liners.
"These agreements allow us the opportunity to meet global needs of our European, North American and Asian automotive customers. As more and more automotive manufacturers are globalizing, suppliers need to be able to provide them with identical products in each part of the world," says Hans Dijkman, business unit director of DSM Automotive Polymers.
Ford Motor Co. and its diesel engine supplier, Navistar International Corp., decide to use conventional gray iron rather than compacted graphite iron (CGI) for the cylinder blocks of the new V-6 diesels that Navistar will make for some of Ford's pickup trucks, vans and SUVs in three years, American Metal Market reports. CGI is a type of iron that has the potential of significantly reducing the weight of castings and making iron more competitive with aluminum, but it has had trouble getting specified in major high-volume automotive applications.
Metal/Plastic Seat World First
In what is being called a world first, Mercedes-Benz has introduced a high-volume car seat that uses a load-bearing metal/plastic composite part. The rear seats of the Mercedes V-Class minivan (sold only in Europe) feature integrated seat belts and are 30% to 50% lighter and 10% to 20% less costly than traditional seats, Mercedes says. The seat was jointly developed by Mercedes, Bayer AG and seat manufacturer Grupo Antolin Irausa SA of Spain. The seat back, which normally consists of 20 to 30 parts, was reduced to only one component. This plastic back with frame-stiffening ribs also features an integrated head-rest support and belt housing and mechanism. A metal frame is married to the plastic on the side where the seat belt is attached.
About the Author
You May Also Like