Cautious expansion: UTA gets more sales without costly constructionCautious expansion: UTA gets more sales without costly construction
TAMPA, FL--Wall Street's infatuation with growth and the auto industry's focus on lean systems are the Catch 22 of the 1990s for the supply community. Growth usually means a cash outlay, which must be recovered via higher product prices.United Technologies Automotive's electronics plant here has found a way to serve both masters. UTA-Tampa is expected to increase its sales volume from $76 million
June 1, 1996
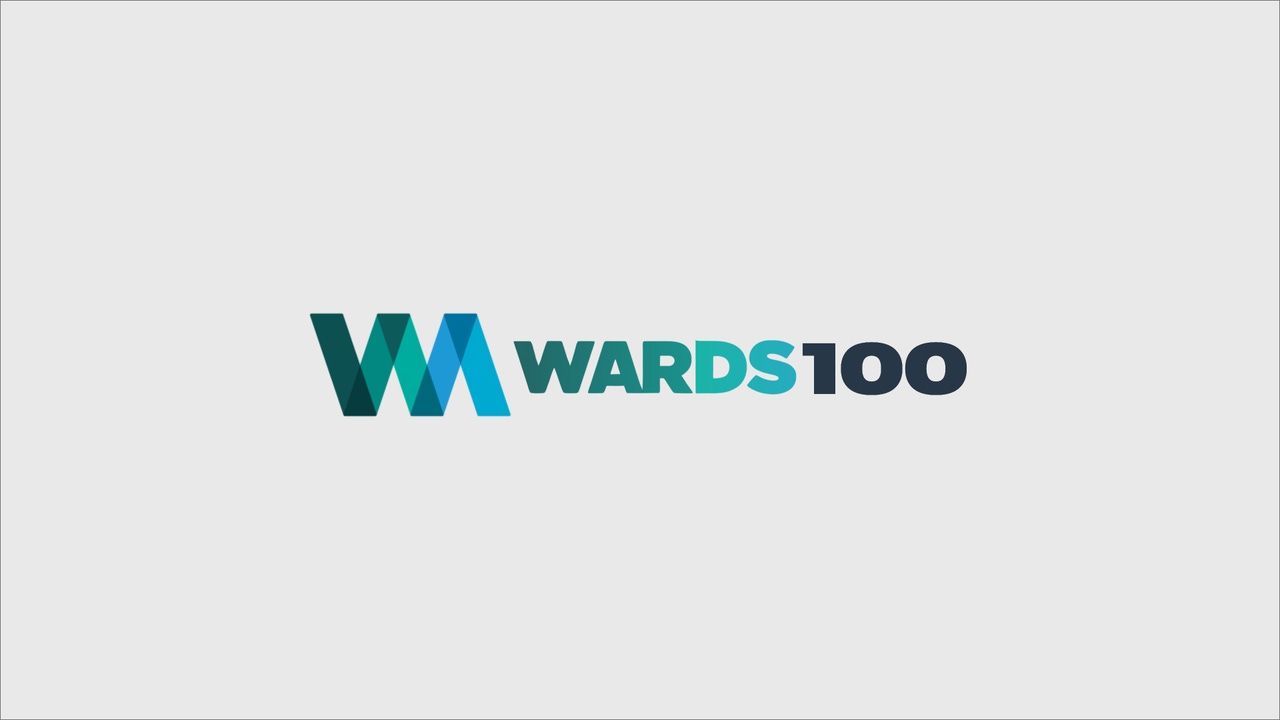
TAMPA, FL--Wall Street's infatuation with growth and the auto industry's focus on lean systems are the Catch 22 of the 1990s for the supply community. Growth usually means a cash outlay, which must be recovered via higher product prices.
United Technologies Automotive's electronics plant here has found a way to serve both masters. UTA-Tampa is expected to increase its sales volume from $76 million in 1995 to $179 million by 2000 without adding to the plant's 100,000 sq. ft. (9,290 sq. m). It's doing this through a combination of astute management, increasing vehicle electronics content and the expansion of component capability. In fact, the number of units coming out of the plant will drop from 13.1 million in 1997 to 7 million in 1998 and hit 8.7 million in 2000.
"The density and complexity of the units boosts the dollar value of the components," says Daniel S. O'Dell, plant manager at UTA-Tampa, which manufactures electronic modules and circuit boards for automotive customers in North America, Europe and Japan.
An example of expanding component functions is UTA's 1990 two-board remote-entry receiver module. The latest version has only one board and 35% less board space, yet 15% more function.
From Tampa, UTA supplies remote entry systems for Buick, Pontiac and Oldsmobiles; immobilization modules, key/ transponder communications and two interior body controllers for BMW AG; a 14-function generic electronic module (GEM) for the '96 Taurus/Sable; door-lock modules and remote entry systems for Honda Motor Co. Ltd.; and remote entry systems for Nissan Motor Corp.
It also supplies a transfer case controller for 4WD Ford Motor Co. vehicles and circuit cards for switches to UTA's own facilities in Zanesville, OH, Traverse City, MI, and St. Matthews, SC. The transfer case business will disappear after 1996 and the switch business goes away after 1997, which helps free up space for new business.
So far, future bookings consist of a multiplex system for a '98 Honda model, a body controller for a '99 Rover model (the plant's first design job for a European customer), all remote-entry key fobs for '98 General Motors Corp. trucks, memory seats and mirrors for some '98 Cadillac models and remote entry for the '98 or '99 Nissan Quest and Mercury Villager minivans.
Besides making room on the plant floor, UTA-Tampa is investing $10 million on new equipment this year. Among the planned improvements are a failure analysis lab and an upgrade of electrostatic discharge (ESD) prevention procedures.
"ESD is the hidden killer of all electronics," says Mr. O'Dell. "When you're talking about single-digit ppm (defective parts per million), it's going to come from ESD."
Mr. O'Dell says his facility currently ships about 108 defective parts per million, a solid number by today's standards and good enough to earn quality honors from GM, Ford, Honda, Nissan and BMW. In the near future, however, anything other than zero ppm will be unacceptable. To that end, the facility has 64 machines that computer-check components coming off the line for defects. Environmental testing also can be performed on site.
Sometimes a worker in a customer assembly plant "can zap a circuit board" with static electricity, which ultimately shows up as a defective part. To cut down on that problem, Mr. O'Dell says his people will do testing of automaker plants and offer ESD solutions as a service to its customers.
Read more about:
1996About the Author
You May Also Like