Despite Troubles, Steel Moves AheadTrade disputes don't disrupt jointresearch effortsDespite Troubles, Steel Moves AheadTrade disputes don't disrupt jointresearch efforts
You judge the strength of a marriage by how well things go during the "for worse" periods, not the "for better" parts.The same can be said for business mergers and consortiums. So far, the steel industry's joint efforts to develop lightweight steel bodies that can compete with plastics and aluminum are passing the test.Despite plummeting demand in many markets, oceans of red ink and serious steel
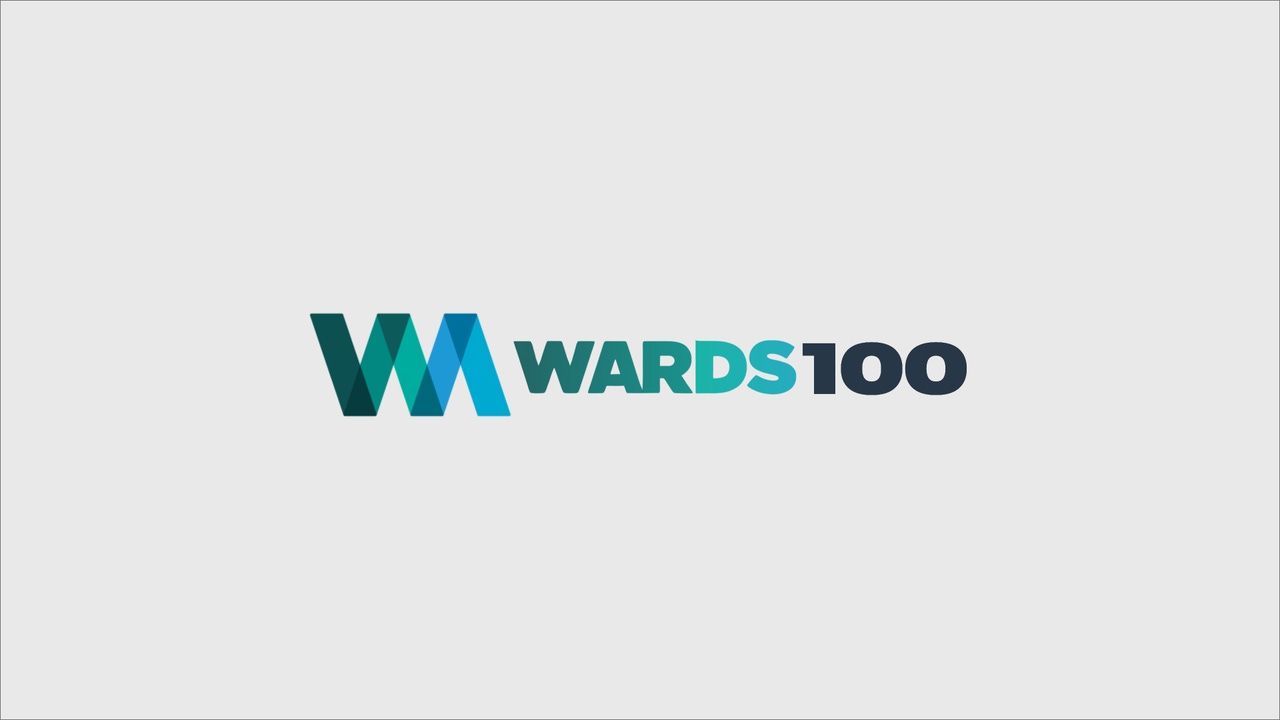
You judge the strength of a marriage by how well things go during the "for worse" periods, not the "for better" parts.
The same can be said for business mergers and consortiums. So far, the steel industry's joint efforts to develop lightweight steel bodies that can compete with plastics and aluminum are passing the test.
Despite plummeting demand in many markets, oceans of red ink and serious steel trade disputes within their home countries, 26 international steel producers still have ponied up $10 million and put aside their differences long enough to launch another major effort toward making ever lighter steel auto bodies.
The $10 million may be far less than some proponents initially hoped for, but it's hardly small potatoes.
This latest collaboration aims to produce steel bodies so light that they would meet the requirements of the U.S. Partnership for a New Generation of Vehicles (PNGV) "Supercar" and the European CO2 reduction program (EUCAR) project.
That boils down to making midsize cars that weigh 2,000 lbs. (907 kg) instead of 3,000 lbs. (1,360 kg) as they do now, and auto bodies that are 40% or 50% lighter. That's no simple task.
This program is the next evolution of the successful $22-million UltraLight Steel Auto Body (ULSAB) effort, which produced 12 prototypes of a steel body-in-white (BIW) at least 25% lighter than typically found on a midsize U.S. car.
Like ULSAB, the new ULSAB-AVC (Advanced Vehicle Concept) will take a clean-sheet approach to create a new vehicle body architecture, but it will go beyond the BIW and include closure panels, suspension, engine cradle and all structural and safety related components.
Porsche Engineering Services Inc. (PES) of Troy, MI, which developed the ULSAB, will handle this assignment as well.
"ULSAB has demonstrated that steel is capable of providing solutions to the most challenging automotive problems at affordable cost without sacrifice of safety or performance," says Dr. Christoph Schneider, chairman of the new consortium. "This new program will reaffirm the steel industry's commitment and further enhance steel's position as the material of choice in automotive applications."
Ideally, steelmakers hope to trot out lightweight steel prototypes capable of getting close to 80-mpg (3L/100 km) at the same time participants in the U.S.-government-funded PNGV program roll out high mileage cars made of aluminum and composites in 2004. Although the steel versions still may be heavier, steelmakers no doubt will argue they will be far less expensive to manufacture than more exotic PNGV creations.
But how do you collaborate with a company you also are accusing of harming your business by dumping their products into your home market below cost?
It's not that hard, says Darryl Martin of the American Iron and Steel Institute. Corporations have to learn how to "compartmentalize" emotions so they don't interfere with a greater good.
"The trade issues are for the lawyers, and the ULSAB-AVC is for the engineers and marketing people," he says. That might be a difficult stance to take in some industries, but veterans of the steel industry, who already have seen much adversity over the past 30 years, just grin and move on. They know they can't afford to allow infighting to slow them down.
Ford Buys More Aluminum Expertise
Reinforcing its stated commitment to increase the aluminum content of its vehicles, Ford Motor Co. announces plans to buy Troy Design and Manufacturing (TDM), a Redford, MI-based engineering company with special expertise in designing dies for stamping aluminum parts.
Ford has had a working relationship with TDM for 20 years. Although Ford will have 100% ownership, Neil Ressler, Ford vice president-Research and Vehicle Technology, says the automaker wants TDM to remain independent in order to maintain the "entrepreneurial spirit and culture that has made it the leader in die development." TDM also has expertise in draw development, soft tooling and die design, Mr. Ressler says.
TDM has 340 employees in two facilities in Redford and Warren, MI.
The giant Expedition sport/utility vehicle currently is Ford's most aluminum-intensive vehicle, with 335 lbs. (152 kg) of the light metal. Other high-volume Ford products that use lots of aluminum include Taurus, with 270 lbs. (122 kg), and the F-Series pickup, with 258 lbs. (117 kg). The upcoming Lincoln LS sedan will contain 415 lbs. (188 kg).
Read more about:
1999About the Author
You May Also Like