Slow to Change--Materials use won't likely see major shiftsSlow to Change--Materials use won't likely see major shifts
Despite the importance of building lighter vehicles, analysts believe most high-volume cars and trucks 10 years from now will be made with roughly the same material content as today. There is reluctance to forecast materials use farther out than 10 years, but using history as a guide, it's unlikely there will be huge changes in materials use even by 2020 - unless there is a major new fuel shock or
November 1, 1999
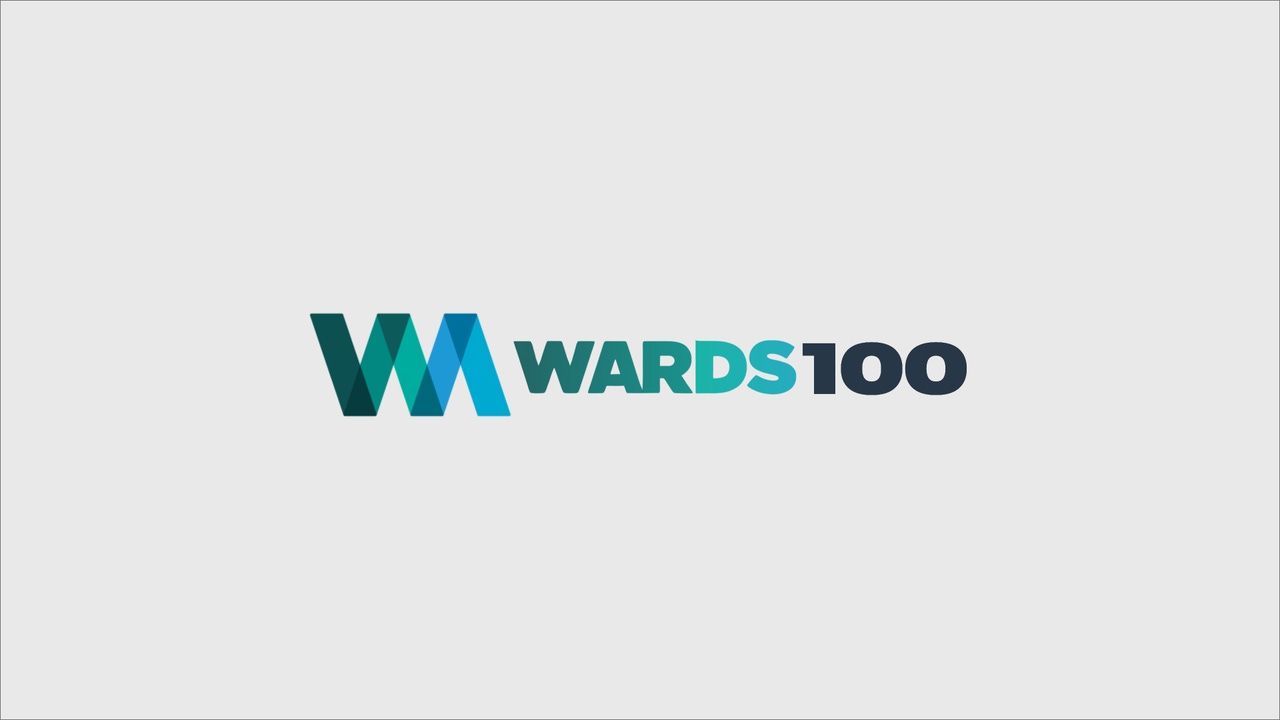
Despite the importance of building lighter vehicles, analysts believe most high-volume cars and trucks 10 years from now will be made with roughly the same material content as today. There is reluctance to forecast materials use farther out than 10 years, but using history as a guide, it's unlikely there will be huge changes in materials use even by 2020 - unless there is a major new fuel shock or environmental initiative.
For instance, in 1979 55% of the weight of a typical North American-built vehicle was steel. In 1999, a typical 2000 model year vehicle is 54% steel.
The primary reason is cost. Steel is far less expensive than lighter weight alternatives, especially in high-volume production. But steel also has been steadily improving over the years. Since the mid 1980s new coatings have made steel bodies more rust-resistant and new alloys of automotive steel have been developed that can be made into thinner, lighter structures.
Steelmakers also are fiddling with steel chemistry and density to make lighter weight steel structures. Very strong and light steel "sandwich" materials that incorporate plastic honeycomb materials also are being developed.
That's not to say other traditional automotive materials haven't taken a big hit over the past several decades. Cast iron, zinc die castings and copper radiators have suffered huge losses to aluminum, plastics and magnesium as automakers have moved to chop weight and improve fuel efficiency. Steel also lost when most car bodies were changed from body-on-frame to unitized body construction in the 1980s as well.
Richard B. Evans, president of the Aluminum Assn. trade group, predicts that in the next 10 or 15 years "steel will represent less than 50% of automotive structures." But few independent observers are inclined to agree.
"Looking at our future product line, I see the balance continuing," says a top General Motors Corp. designer.
The prognosis for aluminum body structures is much more bullish outside the U.S., however. With fuel prices three to five times higher in Europe and Asia, numerous high-mileage aluminum-intensive cars are beginning to dot the horizon.
Plastics proponents say their material is more durable and easier to fix than steel in applications such as pickup truck boxes. Unfortunately for theplastics, magnesium and aluminum industries, steel's affordability remains the t rump card.
"You know how the real estate industry has that saying: location, location, location. Well, in the auto industry it's cost, cost, cost," explains plastics analyst Jim Best of Toledo, OH-based Market Search.
As important a factor as Mr. Best says it is, cost often is forgotten or ignored by forecasters. In a 1979 presentation to Congress on the Automotive Fuel Economy program, U.S. Dept of Transportation Secretary Brock Adams told legislators that by 1985 a car will use about 300 lbs. (130.7 kg) of aluminum. Today, American Metal Market reports the average amount of aluminum in a 2000 model vehicle still falls short of the prediction: it's about 247 lbs. (107.6 kg).
Mr. Brock's forecasts also included major growth for reinforced plastics, rising from 165 lbs. (71.9 kg) per vehicle in 1977 to 350 lbs. (152.5 kg) by 1985. That hasn't happened, either. In fact, the combined pounds per vehicle of all plastics in 1998 was 253 (110.2 kg), according to Market Search.
Magnesium is no different. A 1992 University of Michigan Delphi survey says the light metal "should come on strong."
It is. But from a very small base. The typical North American-built vehicle currently contains less than 7 lbs. (3 kg) of magnesium, says Magnesium Alloy Corp., which is preparing to become a major magnesium producer.
Meanwhile, steel is losing ground - but not nearly at the predicted rate. The 1992 U of M forecast said the average North American passenger car would have 1,560 lbs. (679.5 kg) of steel in 2000. Currently, today's vehicle includes about 1,800 lbs. (784.1 kg). "Steel, which we thought we knew everything there was to know, has turned itself into a moving target for the other materials," points out David Cole, director of the Office for the Study of Automotive Transportation at U of M.
The steel industry's stamina can be attributed to the Auto/Steel Partnership and the development of the Ultra Light Steel Auto Body (ULSAB), a prototype steel body-in-white that is as much as 34% lighter than a conventional BIW.
The components steel has lost have been relatively small. And there has been quite a bit of cannibalization among the alternative materials: plastics replacing plastics, magnesium supplanting aluminum, and so on.
But while forecasts have been wrong about massive change, the next two decades shouldn't be any less competitive. "The pressure for lighter vehicles isn't going to let up," says Tom Sweder, manager, weight engineering and advanced vehicle technology for Ford Motor Co.
Mr. Best foresees plastics winning bumper beam, fascia, clutch pedal and other applications. Aluminum promises to further dominate cast iron under the hood - GM plans to increase production of all-aluminum engines by 300% in the next few years - as well as chassis systems and other major components. Magnesium's future lies with intake manifolds, instrument panel support beams, seat structures, and other applications.
Read more about:
1999About the Author
You May Also Like