You heard it here first; SPE serves up a banquet of innovative plastic partsYou heard it here first; SPE serves up a banquet of innovative plastic parts
`Many experts believe it's the most significant piece of plastic or composite material on the '96 models," I wrote back in September (see WAW). Well, now it's official: The Society of Plastics Engineers (SPE) Automotive Div. gave the radiator support on Ford Motor Co.'s new Taurus/sable the top prize at its 25th annual Automotive Awards Banquet in November.The SPE Automotive Div. Awards is the largest
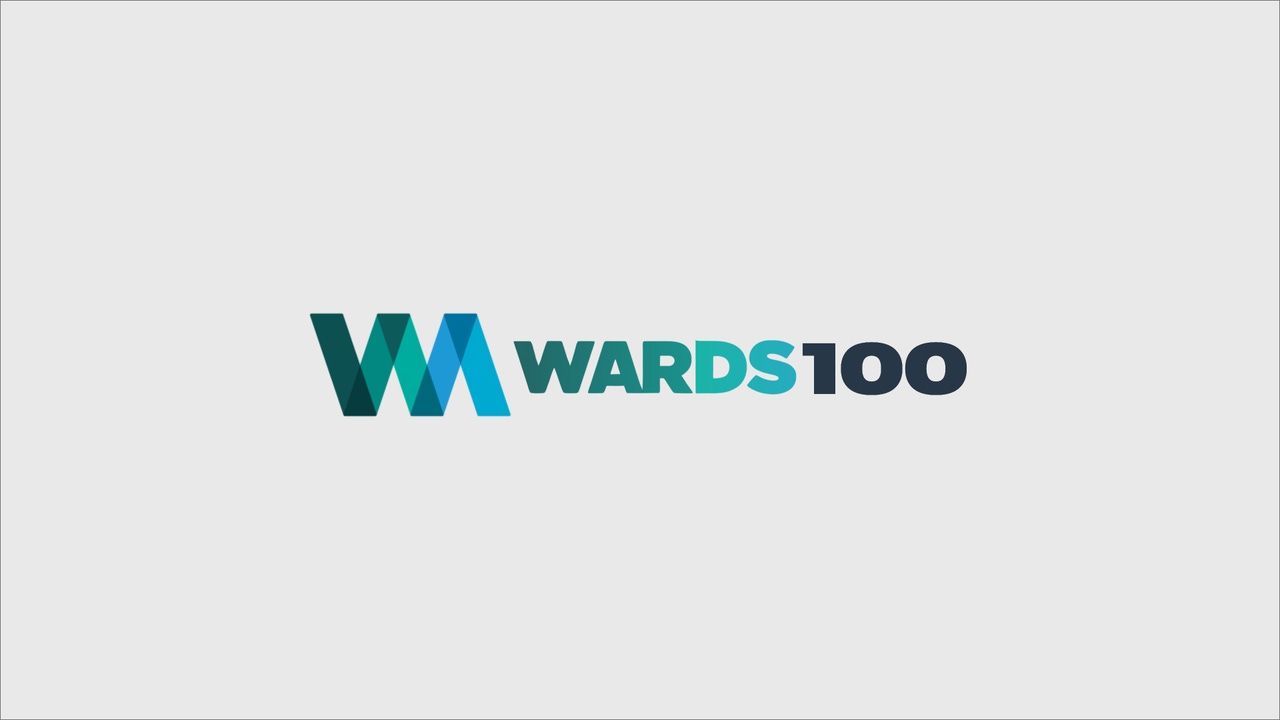
`Many experts believe it's the most significant piece of plastic or composite material on the '96 models," I wrote back in September (see WAW). Well, now it's official: The Society of Plastics Engineers (SPE) Automotive Div. gave the radiator support on Ford Motor Co.'s new Taurus/sable the top prize at its 25th annual Automotive Awards Banquet in November.
The SPE Automotive Div. Awards is the largest competition of its kind in the world and is a very big deal in Detroit's automotive plastics community. Scores of plastics industry executives donate their time to the competition throughout the year. For several months at least, picking the most innovative plastic auto parts becomes a full-time job for about a dozen volunteers. Nearly 100 entries are scrutinized each year. I have been a member of the judging panel for almost 10 years, and just picking the category winners from a small pool of finalists sometimes takes the better part of a workday. Finalists get 10 minutes to explain to 12 judges why their part should win, and it's clear some spend hours practicing their pitch. Last year a group even put on a skit to make their point. That's pretty radical for engineers.
The competition culminates at the annual awards banquet, where 1,000 or so engineers pay $60 each to eat a generic dinner and learn the results.
Unfortunately the true "innovativeness" of the parts has been weak in the past several years, due mainly to severe cost-cutting initiatives at the Big Three. But this year a number of entries broke new ground. The sheet molding composite (SMC) Taurus radiator support, or integrated front end system (IFES) as it is officially called, beat out 80 other entries competing for the prestigious Grand Award. It also won the chassis/ hardware category.
The IFES does far more than what you would expect from a plastic part. The result of a joint development effort by Ford Motor Co., The Budd Co. and Autodie International Tooling Tech Center, it saves weight, reduces the component count from 22 parts to three, eliminates 27 fasteners and cuts costs 14% compared with a traditional front-end design.
But it also plays important structural and manufacturing roles. During vehicle assembly, the upper part of the radiator support is bolted to the front fenders and body structure. It positions the lamps, hood latch, hood slam bumpers, fenders and bumper fascia. The lower part of the IFES serves as the support for a modular assembly incorporating the radiator, transmission fluid cooler, air conditioner condenser, cooling fans and other components and is built up off site at a Ford Climate Control Div. plant.
Then it's shipped to Taurus/Sable assembly plants in Atlanta and Chicago. Once there, both pieces of the IFES are bolted together and incorporate the structure for the hood latch, while contributing to the overall stiffness of the vehicle front end. Those are two big steps for a plastic part. But together, they represent a giant leap for the plastics industry.
Additional awards are presented for innovation in interior, exterior, powertrain, process, environment and materials categories. Here's a quick rundown:
* Body Interior. A blow-molded knee bolster developed by Dow Chemical Co., GM's North American Truck Group and the LCF Div. of ABC Group for the '96 Astro and Safari vans is the first blow-molded part used in a structural application. It replaces a multi-piece steel and plastic panel. Crash safety standards are met by adjusting the wall thickness of impact ribs and through tooling.
* Body exterior. The single-sided encapsulated glazing process for the '96 Chrysler minivans provides a flush look, aerodynamic appearance and no visible hardware. It was a combined effort of Dow Automotive Materials & Services Group, Chrysler and Donnelly Corp.
* Process. Two entrants tied in this category. One is the exterior door handle and bezel assembly for the '96 Chrysler minivans and the other is the interior trim package for the '96 GMC Savana and Chevy Express full-size vans. The door handle assembly, developed by Allied Signal Plastics, Chrysler minivan engineering and Siegel-Robert Inc., is the first use of a multiple cavity air-assist molding process. It opens new fields for plastics in applications previously limited to metal. The other winner, a joint effort between Venture Industries, Monsanto Corp., GM and several other suppliers, uses a new "hot runner" molding system that allows the production of large pigmented ABS plastic parts, eliminating the need for painting and significantly reducing costs.
* Powertrain. The transmission accumulator piston for the '96 GM 4L60E and 4T40E transmission is an innovation in design featuring tight tolerances, low weight and low cost. Developed by Hoechst Celanese Corp., GM and Webster Plastics, it is the first thermoplastic part used internally in the transmission in a load-bearing, dimensionally critical application.
* Environmental. The co-extruded fuel tank on the '96 Chrysler Jeep Grand Cherokee is the first plastic fuel tank in the industry that meets the latest California Air Resources Board (CARB) hydrocarbon emission laws for all fuels. Developed by BASF Corp., Chrysler and Kautex Corp., the exterior wall of the tank also uses 50% post-process regrind material.
* Materials. In a new and unusual use of plastic first reported 18 months ago (see WAW -- June '94, p. 30), Raychem Corp.'s Polyswitch polymeric resettable fuse is made of a carbon-filled cross-linked polyethylene that conducts electric current. If too much current flows through the device, it beats up and expands, pulling the conductive particles embedded in the plastic away from each other and breaking the circuit. When the plastic cools, it contracts and resets the circuit. This concept eliminates the need to replace fuses -- and the need for complex wiring schemes to locate them in an easily accessed fuse box. Developed by Raychem and Chrysler and used on the '96 Chrysler minivans, the new plastic fuses trip faster than conventional devices, save space and cut costs.
Aluminum industry focuses on autos
Imagine what would happen if the Russians dumped 6 million ultra-cheap cars on the U.S. market in one year.
That in essence is the equivalent of what happened not long ago to the western world's aluminum industry when the former Soviet Union exported 2.5 tons (2.3 million t) of aluminum on western markets in one 12-month period, says Jacques Bougie, president of Alcan Aluminum Ltd., the world's second largest aluminum company.
Although the western world now has absorbed all the aluminum placed on global markets by the former Soviet Union, it has forced the industry into major downsizing moves over the past four years Mr. Bougie says.
Speaking at the 16th annual Automotive Aluminum Design and Fabrication Seminar recently, Mr. Bougie says Alcan has chopped its global employment from 60,000 to 38,000 without reducing production capacity. It now is focusing on new products, new technologies and new partnerships, especially with the auto industry.
Alcan has invested $140 million in the development of materials and enabling technology for aluminum-intensive vehicles and other end uses for aluminum in automobiles. He declared that automotive bodies and parts are the "next frontier" for the aluminum industry, and took a few swipes at the steel industry's new light-weight steel body concept. "Steel, even a lightweight steel design, cannot achieve the performance standards of aluminum," he says.
Although a typical 1995 family vehicle built in North America contains only about 5.8% aluminum, compared with 67.5% for iron and steel and 7.7% plastics, Mr. Bougie says aluminum content should grow by an annual rate of 3.5% to 4% through the year 2000. "No other metal is expected to equal the growth rate predicted for aluminum to the end of the century," he says.
About the Author
You May Also Like