2000 Harbour Report
The home team won a big one last month, and local newspapers gave it a lot of play. For the first time, an auto plant run by a Detroit automaker was ranked as the most efficient in the U.S. and Canada by the annual Harbour Report on auto plant labor productivity.But while Ford Motor Co.'s Atlanta Assembly plant grabbed the headlines by winning a high-profile battle with Japanese automakers, the Harbour
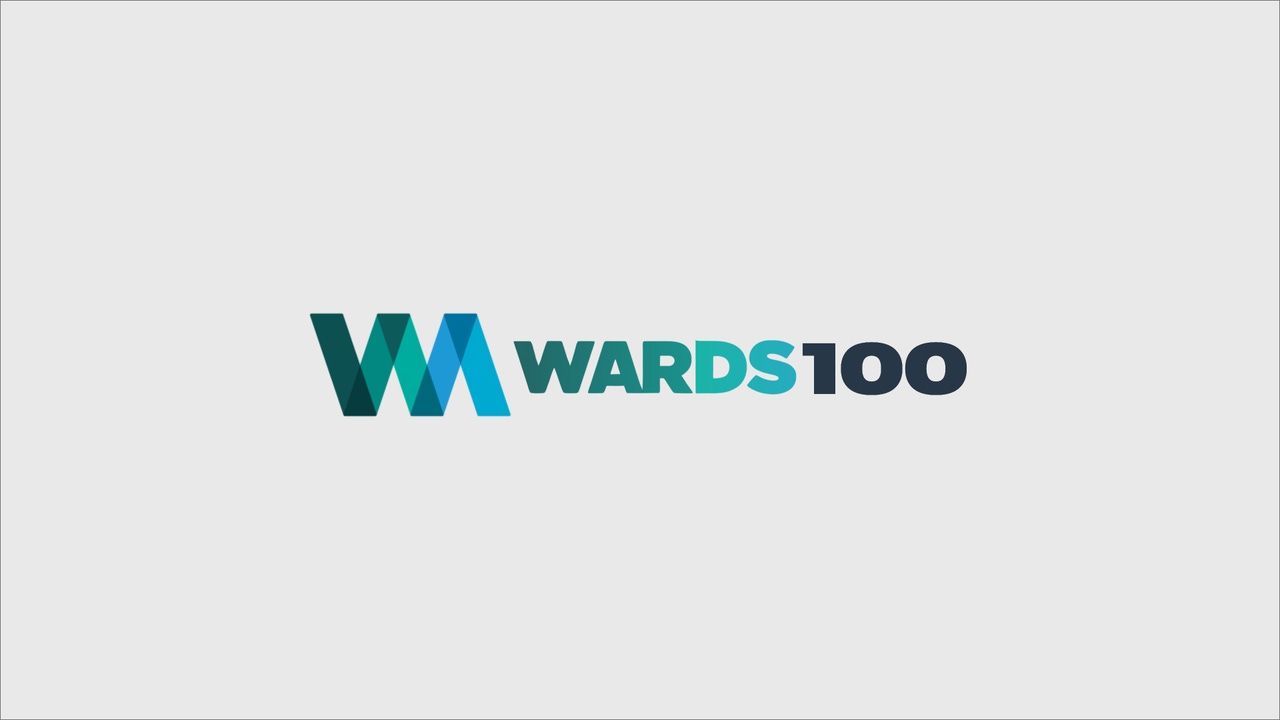
The home team won a big one last month, and local newspapers gave it a lot of play. For the first time, an auto plant run by a Detroit automaker was ranked as the most efficient in the U.S. and Canada by the annual Harbour Report on auto plant labor productivity.
But while Ford Motor Co.'s Atlanta Assembly plant grabbed the headlines by winning a high-profile battle with Japanese automakers, the Harbour Report numbers revealed that General Motors Corp. appears to be winning an even bigger conflict: its war with its own lack of efficiency.
So even though Japanese-owned auto-makers still ranked as the most efficient manufacturers overall in North America, with the leanest assembly, stamping and engine plants, this latest report on automotive productivity by Harbour and Associates Inc. - usually a downer for Detroit's former Big Three - actually was chock full of encouraging news for GM, Ford and DaimlerChrysler's Chrysler Div.
Long criticized for being the least productive manufacturer in North America by a wide margin, GM improved its productivity by almost 9% last year, far more than any other company in the study. Already better than DaimlerChrysler in the total average of labor hours it requires to build a vehicle, in 1999 GM closed its overall productivity gap with Ford by about 40%. It also significantly narrowed its gap with the best of the best: Nissan Motor Mfg. Co., Honda of America Manufacturing Inc., and Toyota Motor Mfg. Inc.
Nowhere is that more apparent than in GM's powertrain operations, where GM passed Ford in overall manhours per engine ratings for the first time ever.
"In engine, much like in stamping, GM Powertrain has stayed with its plan to establish a global manufacturing system to drive competitiveness," Mr. Harbour says. "The results have been apparent over the last few years but never more noticeable than in 1999."
"They are moving away from the pack in the way they are implementing lean manufacturing, and they are making some substantial changes in product and process that are driving this improvement," adds Laurie A. Felax, a Harbour and Associates analyst.
She adds that it is starting to get tough to distinguish the inside of GM's newest manufacturing facilities from those of Toyota.
Ford's efficiency in engine manufacturing is disadvantaged by the fact it has a higher percentage of more complex overhead-cam engines, but Harbour analysts say that doesn't fully explain why GM is pulling ahead. GM is in fact implementing Toyota-like lean manufacturing techniques faster than its domestic competitors, Mr. Harbour says, and it is paying off.
And despite all of the headlines about a Ford plant ranking as No.1, it was the equivalent of a photo finish. The winner squeaked past the next two contenders by less than one man-hour per car, but it was a big moral victory for Ford and Detroit, which have been told for more than two decades that they can't match the Japanese in productivity or quality.
Ford's Atlanta assembly plant, which builds the Taurus and Sable sedans, beat out the usual winners, Nissan's big plant in Smyrna, TN, and Toyota's plant in Cambridge, Ont., Canada.
But Ford's Atlanta plant still overcame significant obstacles to become No.1: It's far older than the other top plants; suppliers aren't located nearby; and it went through a new-product launch last year, which usually murders productivity numbers.
"To maintain 17.5 hours/vehicle in a launch year is a really good performance. It means you planned well in advance for launch, and you successfully executed," says Ms. Felax.
But there was sobering news, too. Ford still is ranked as the best of Detroit's former Big Three automakers, but its overall productivity has plateaued in recent years - despite the stellar performance of its top car and truck plants. Harbour experts say that may be because the automaker is focusing too much on improving manual labor productivity rather than improving the overall efficiency of its manufacturing systems. Ford officials acknowledge they recently have been focusing more on other means of reducing costs, such as inventory reduction.
Meanwhile DCC has something to brag about, too: based on Harbour's calculations, it made the highest profit per vehicle - $1,470 - of any automaker in the study last year, thanks to a production mix very rich in high-profit light trucks.
Honda came in second with a worldwide profit of $1,440 per vehicle. Ford and GM averaged $1,034 and $853 per vehicle, respectively, in profits last year, while highly efficient Nissan lost $17 per car. Clearly, Nissan's profitability problems are not related to manufacturing productivity, Mr. Harbour says.
DCC's stamping operations also logged a 13% improvement in hours per vehicle, although its stamping operations remain the least productive of the major North American manufacturers.
About the Author
You May Also Like