Ford Adds Hybrid Transmission to New Flexible Assembly LineFord Adds Hybrid Transmission to New Flexible Assembly Line
Making disparate transmissions on the same line is taking flexibility to a whole new level for the auto maker, but it is seen as a sound business move by top brass, says James Tetreault, vice president-North America Manufacturing.
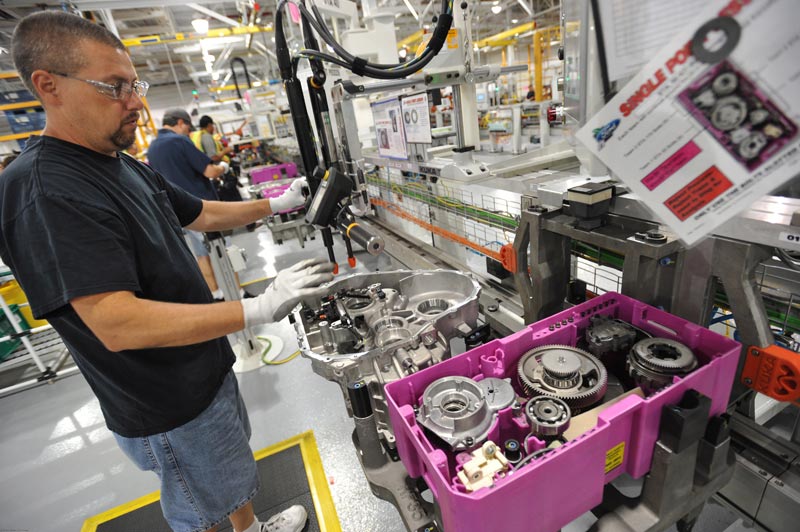
STERLING HEIGHTS, MI – Ford’s decision to add production of a new hybrid transmission at its Van Dyke Transmission plant here was based on a desire to avoid things like “in the old days,” a top executive says.
The transmission, dubbed the HF35, will be used in the upcoming C-Max hybrid and plug-in hybrid models, as well as the Fusion hybrid and PHEV and Lincoln MKZ hybrid.
It will be built on the same line as the auto maker’s standard 6-speed transmission, used in a wide range of Ford products worldwide.
Making disparate transmissions on the same line is taking flexibility to a whole new level for Ford, but it is seen as a sound business move by top brass, says James Tetreault, vice president-North America manufacturing.
Having separate lines for each transmission likely would have led to many of the same issues Ford has faced in the past.
“We don’t want to be in a position where we have overcapacity on one or are under capacity on the other,” he tells WardsAuto. “Then we have wasted capital and wasted labor. Our strategy with putting flexibility in our plants is being able to respond to whatever the market decides it wants.”
The Sterling Heights plant has annual capacity for 1.5 million transmissions. But Tetreault says there’s no way to determine how many of the hybrid gearboxes will be built, because the auto maker is unsure of demand for its electrified-vehicle lineup, especially with the ongoing fluctuation in U.S. fuel prices.
“We didn’t want to build a dedicated transmission line, because if we did that we would have gotten the capacity wrong,” he says. “It was important to figure out how to do this on a flexible system.”
Although the 6-speed is a traditional step gearbox and the HF35 is a modified continuously variable transmission, the Ford engineers who developed the hybrid transmission used similar parts where possible to simplify the assembly process.
Even so, there are different steps in assembly of the the HF35 that had to be taught to the plant’s 1,350 workers, Tetreault says.
“The goal was working with the design team to get the bill of design and process compatible as much as we could. But there are unique operations like energizing the magnets on the motors that had to be integrated into the line.”
Prior Ford hybrids used a transmission sourced from Japanese supplier Aisin. Tetreault says the decision to develop a new transmission and bring its production in-house saves the auto maker the cost of freight, labor and components, as well as protecting it from fluctuating currency rates.
The new HF35 is superior to the Aisin transmission, as well, Tetreault says, noting its lighter, more fuel-efficient and able to handle greater loads.
Ford hired 130 additional workers to man the new flexible assembly line, which recently launched Job One. It invested $220 million to add tooling and renovate 200,000 sq.-ft. (18,580 sq.-m) of previously unused floor space.
The investment is part of a $632 million commitment Ford and its suppliers are making to increase capacity and flexibility in three North American transmission facilities by 2015.
About the Author
You May Also Like