Ford/Amcast aluminum differential carrier for new F-150 pickup
A leader in the conversion to aluminum of high-integrity, performance-critical automotive components, Amcast Automotive has developed a new aluminum vehicle component that was formerly made of iron. This critical part is the front differential gear carrier on Ford's hot new F-150 pickup truck.Named "Truck of the Year" at the 1996 North American International Auto Show, the new F-150 features a new,
September 1, 1996
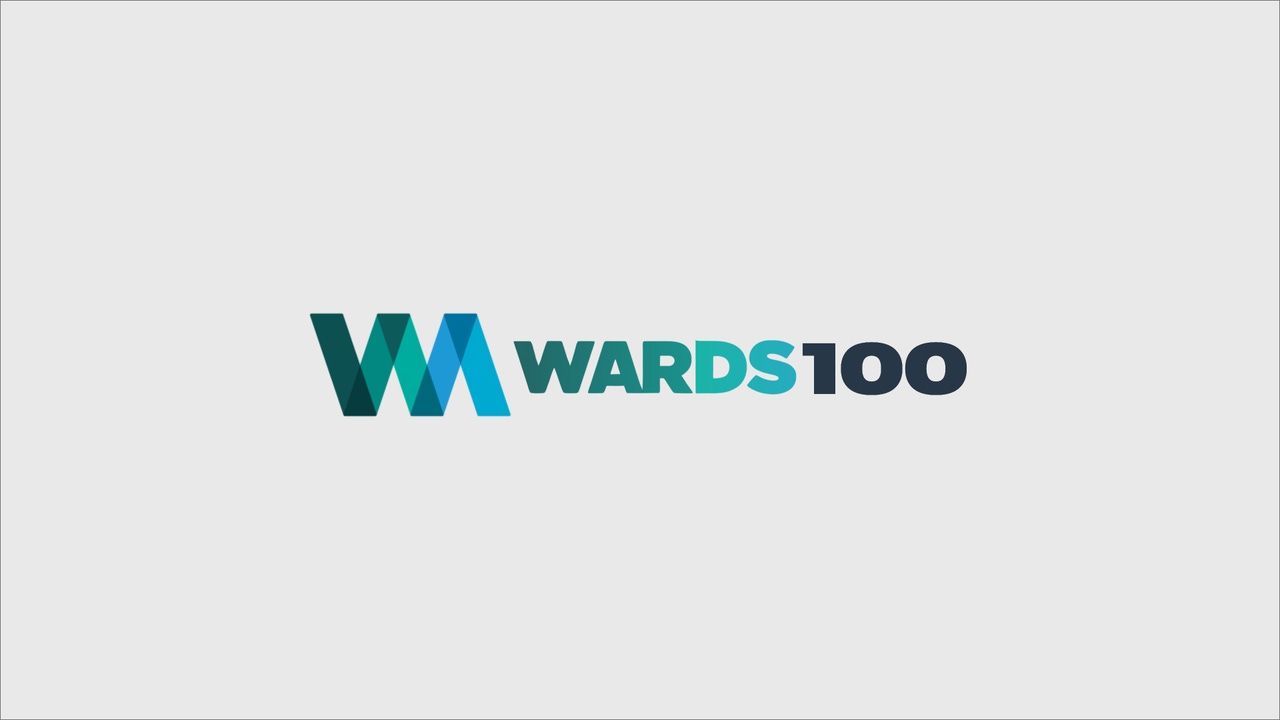
A leader in the conversion to aluminum of high-integrity, performance-critical automotive components, Amcast Automotive has developed a new aluminum vehicle component that was formerly made of iron. This critical part is the front differential gear carrier on Ford's hot new F-150 pickup truck.
Named "Truck of the Year" at the 1996 North American International Auto Show, the new F-150 features a new, lightweight aluminum front differential carrier cast by Amcast Automotive. Traditionally made of cast iron, differential carrier housings weight upwards of 40 pounds. By contrast, the new aluminum housing weighs only 18 pounds, and is specially designed for this critical-performance, high-strength application.
Initially conceived in 1992 by Ford's Axle, Drive Line and Suspension Engineering Group, Amcast Automotive was awarded a contract to cast the housing for the new carrier. One of Ford's goals in the newly designed F-series line was to replace the twin I-beam suspension with a short-long arm (SLA) suspension. This design change allows the carrier to house the gears without having to bear the axle load of the truck, and thus become a prime candidate for weight reduction.
The key design issues in the development of this F-150 differential carrier were weight reduction, stiffness and NVH (noise, vibration and harshness). Working as a team, Ford and Amcast successfully engineered the carrier housing to meet all program goals. Carrier stiffness was vital to ensure the ability of the gears to stay in design position, and to see that torque was internally absorbed so as not to be transmitted to the vehicle body.
According to Ford design team product engineer Mike Carter, "The other concern was strength, but we found that the aluminum carrier was much stronger than we anticipated." Amcast assured this high integrity by employing advanced computer solidification modeling techniques to aid in mold design and process development.
With Ford wanting to maintain the tough image of the truck, the front carrier/axle combination was subjected to a heavy amount of field testing procedures, including applying approximately 100 percent torque to the front axle and performing "snap" starts.
In addition to meeting weight reduction and stiffness targets, Ford engineers were concerned with the possibility of NVH coming from the carrier itself. Carter also noted that they spent an extensive amount of time on NVH work. "Even though 4-wheel drive would be engaged only about 20 percent of the time, we are still spinning the differential gears, and NVH might be a concern. In the end, the carrier passed the NVH requirements with flying colors.
"This aluminum carrier housing has proven itself over and above what we expected," Carter concluded. "With increasing pressure from the government to reduce weight, and with casting technology and products becoming better and stronger, I see a future of great opportunities for more aluminum applications."
You May Also Like