Ford Australia Christens New R&D Center
The R&D center is part of a plan to invest more than A$1.8 billion in projects and facilities over the next decade.
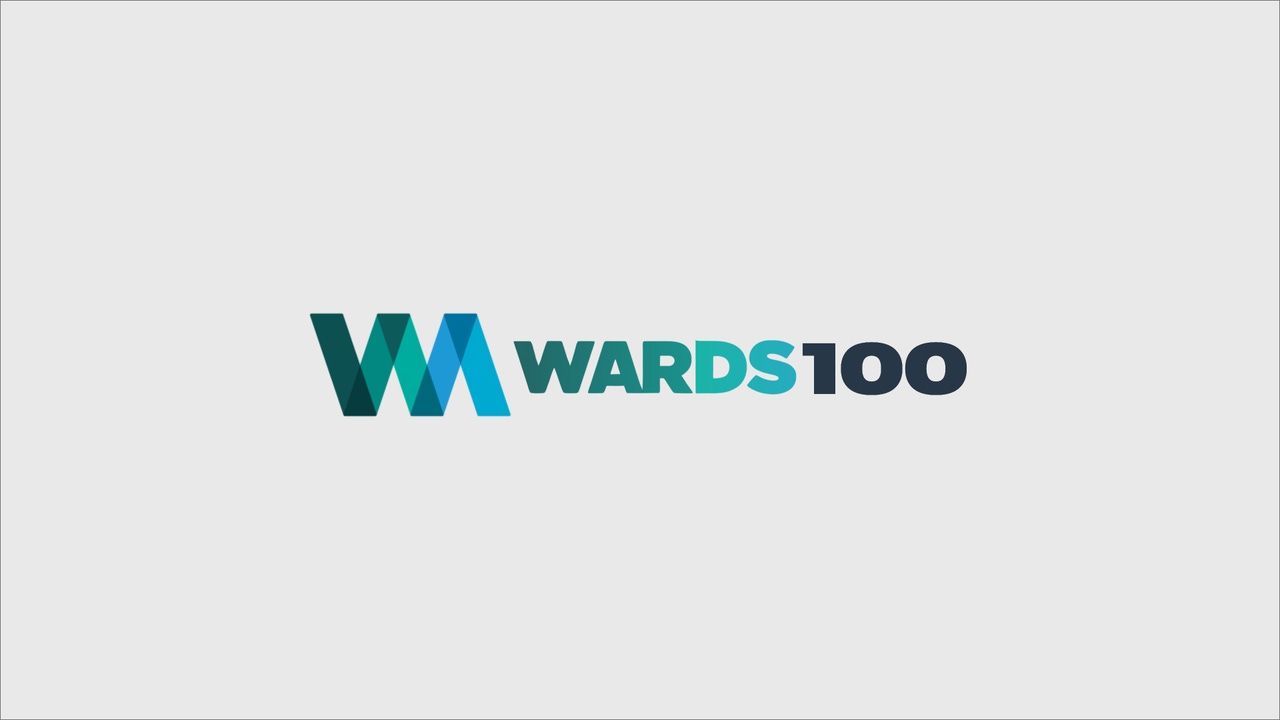
Ford Motor Co. of Australia Ltd. unveils its new research and development center as the first of a number of new facilities that will allow it to continue engineering vehicles for both local and overseas markets.
The center follows a mid-2006 announcement of a new strategic direction for the auto maker, including plans to invest more than A$1.8 billion ($1.6 billion) on new projects and facilities over the next decade.
The new R&D center in Geelong, Victoria, will be completed early next year and will be one of the first facilities to come on line as part of the overall investment program. Money also will be doled out for new equipment and facilities within Ford’s Stamping Operations and at the Ford Australia Proving Ground.
“The new facilities in Geelong and at our proving ground represent some of the most significant facilities investment programs ever undertaken by the company, demonstrating our commitment to technological leadership, as well as helping build Ford’s capability as an innovative and progressive vehicle manufacturer,” Ford Australia President Tom Gorman says.
“The new R&D Center is set to become a centerpiece of our local operation, which will underpin future engineering projects and equip Ford Australia to play an even greater role within the Asia/Pacific region.
“It will enhance Ford Australia’s position as a design and engineering center of excellence within the company’s global product development community, as well as ensuring our local operation can take advantage of strategic global opportunities.”
The A$27 million ($23.7 million) R&D Center is larger and more efficient than the Product Engineering Office (PEO) it replaces, which was built during World War II as a warehouse and then converted to the PEO in the early 1960s to support the early development of the Falcon.
Located adjacent to Ford’s engine and stamping plants at the Geelong Automotive Manufacturing Operations (AMO) site, the center contains two separate buildings connected by an overhead walkway. A 2-story office complex sits across the front of the site, with three large workshop bays extending behind the offices and a smaller, second building positioned at the rear of the facility.
Covering a total area of 107,340 sq.-ft. (9,972 sq.-m), split 40/60 between office and workshop spaces, the new buildings will house about 350 engineers and support staff in the office complex and a further 120 employees across the workshop areas.
The design and layout of the office complex permits a flexible arrangement that allows for alternate work group requirements depending on the various stages of a vehicle development program.
The four adjoining workshop areas include a prototype shop; development garage; mechanical and hydraulic test laboratory; and an engine test and development laboratory.
In the prototype shop a team will craft prototype panels and modify complete vehicles to allow package clinics and dynamic evaluations of future vehicle proposals.
The development garage contains the latest vehicle-lift hoists to suit a wide range of models.
The mechanical and hydraulic test laboratory contains new noise enclosures for completing component and full-vehicle testing with servo-hydraulic road simulators and high-frequency vibration testing equipment.
In most cases, the equipment is mounted on specially designed large seismic masses (huge concrete blocks) sunk into the ground to isolate major rig test facilities from the surrounding building.
The engine test and development laboratory is the last part of the new structure to be completed and is also the most complex part of the construction. The 3-story layout features all the services in the basement and on the first floor, allowing a simple and efficient layout of the engine dynamometers on the ground floor.
The front facade of the center is a modern interpretation of the original brick Ford manufacturing building built in the 1920s.
Over the past three years, substantial investment has transformed Ford’s Stamping Operations in Geelong, with new buildings, new press lines and new press equipment added to the facility in support of the launch of a new, eighth-generation Falcon.
Total investment in the stamping facility of A$55 million ($48.3 million) incorporates a new “wide-body” press line, hydraulic try-out press and new blanking press, along with the accompanying building extension.
The new wide-body Press Line 21 consists of four integrated, state-of-the-art mechanical presses with robot automation, which will produce a single-piece body-side panel – a first for Ford in Australia. The 1-piece technology will be used in producing side panels for the new Falcon beginning in 2008, which Ford says will improve quality and vehicle rigidity and refinement.
Serviced by six robots and five automated guided vehicles, the new press line is capable of producing between 380-520 parts per hour and eventually will press up to 28 unique parts.
The tandem presses also are capable of stamping left- and right-hand side doors simultaneously for every cycle, courtesy of smart tooling design, which both improves productivity and lowers costs.
The new press facility provides Ford’s local manufacturing operation with a number of world-class features, including a world-first in aluminum tooling with an auto tool-change device.
An array of new facilities have been commissioned for Ford Australia’s You Yangs Proving Ground (YYPG) during 2007, as the company takes on an enhanced role as a design and engineering “center of excellence” for the Asia/Pacific and Africa region.
In addition to the new automotive test facilities being developed under the Advanced Center for Automotive Research and Testing banner, Ford’s YYPG has been upgraded with a number of major new facilities, including a vehicle semi-anechoic chamber, a vehicle-dynamics area, a kinematics and compliance (K&C) rig and a high speed test center.
“More than A$29 million ($25.5 million) has been invested in the new facilities, which will contribute significantly to Ford Australia’s leading-edge design and engineering capability,” Gorman says.
System specifications for the Ford Australia K&C rig, including displacement, force and movement ranges, are equivalent to or better than all existing rigs of its kind within Ford Motor Co., Gorman says.
About the Author
You May Also Like