Ford Expects ’10 Models to Achieve Best-Ever Quality
Ford executive Bennie Fowler says Ford’s recent quality improvements and its confidence going forward emanate from a disciplined and standardized product-development process.
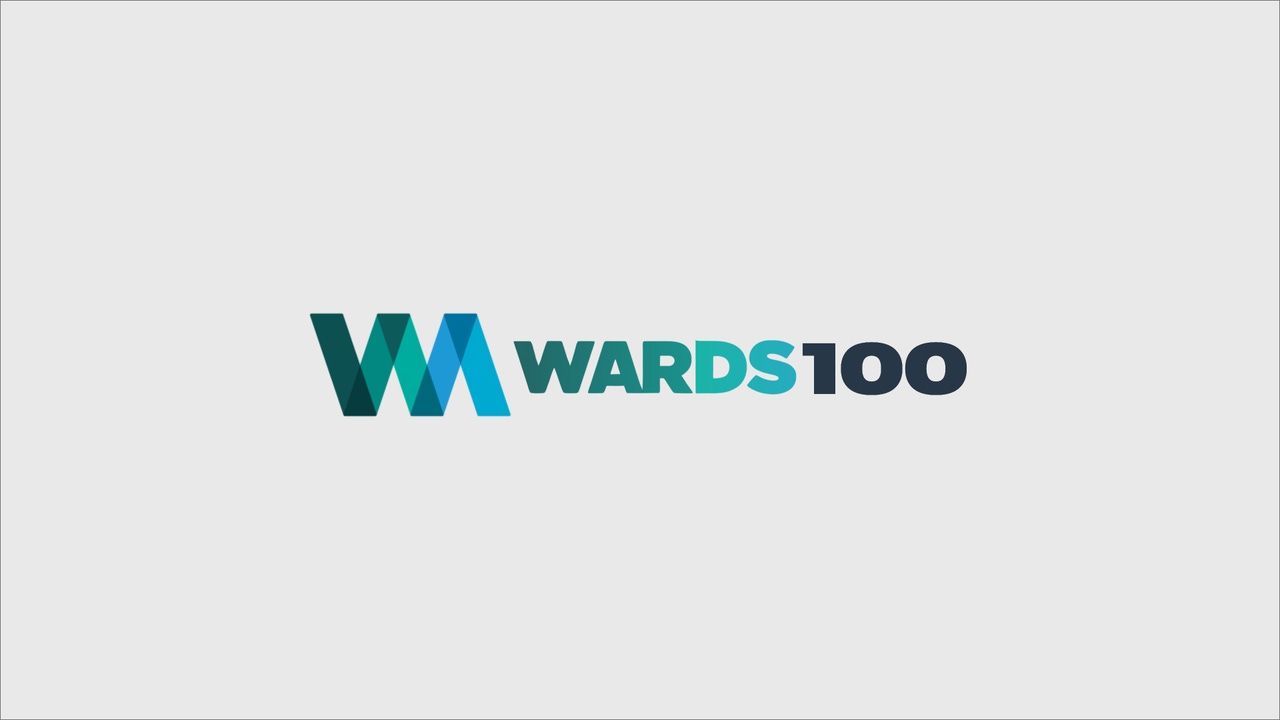
Special Coverage
Management Briefing Seminars

TRAVERSE CITY, MI – Ford Motor Co.’s quality czar says the auto maker will build its most reliable vehicles ever with the ’10 model year, driven by more than a decade’s worth of worldwide process improvements.
“For 12 years, quality has been like a giant rock we’ve been rolling uphill, and finally we’ve reached the summit,” Bennie Fowler, group vice president-global quality, says during an address to the Management Briefing Seminars here today.
“Remaining at the summit won’t be easy, but we know what to do and we know how to do it,” says Fowler, who was appointed to his present role in April after 18 years with the auto maker’s manufacturing group.
Fowler insists Ford’s quality now matches that of longtime industry leaders Toyota Motor Corp. and Honda Motor Co. Ltd., citing recent initial-quality data from J.D. Power and Associates.
The study shows the Ford brand improving year-over-year, pushing it up from the 18th spot to No.14 in the industry ranking. The Mercury nameplate held onto its No.2 place behind Toyota’s Lexus brand and Lincoln drove up to No. 8.
“This follows our own internal data,” says Fowler, who considers initial quality a key predictor of long-term reliability. “We’ve known this for quite some time. Ford, Lincoln and Mercury brands have improved their long-term durability for five straight years.”
Fowler says Ford’s recent quality improvements and its confidence going forward emanate from a disciplined and standardized product-development process the auto maker consolidated over the last 12 months from a region-by-region effort into a global organization.
Bennie Fowler
While Ford’s various regions exercised a sharp focus on the quality processes in previous years, different people in different markets around the world implemented it in different ways.
“And if I’m truly honest, it was followed sporadically,” Fowler says. “Our data shows if we follow the processes with discipline, the quality results are there. As a result, the Ford leadership team has committed to eliminating the variability in our processes around the world.”
Fowler’s group provides technical support to senior leaders of the various functional groups at Ford, who ultimately are responsible for continuous quality improvement within their unit.
For example, Ford begins with quality attributes consumers consider important, such as fuel economy, lower emissions, safety features and craftsmanship. The auto maker designs those attributes into a vehicle at the start of a product program and validates them at Ford laboratories using sophisticated virtual-reality software.
Depending on the model, Fowler says, Ford engineers check upwards of 40,000 design standards before the vehicle moves to its second stage of development. At the manufacturing level, virtual tools confirm the consistency of the design, with the safety of the auto worker in mind.
“As a result of these technologies, we’ve been able to cut the time to market by eight to 14 months, depending on the size of the vehicle program,” he says. “We’ve reduced costly, late engineering changes, and we’re building fewer, but better, physical prototypes.
“And now, we have the lowest worker-injury rate in our company’s history.”
Ford also feeds customer claims from the dealership in near real-time directly back to the assembly plant, where engineer-led teams trained in problem-solving address the claims.
“Sometimes, it’s a matter of changing how a part fits into a workstation, or a design solution may be required,” Fowler says. “But I can assure you we work on every claim, every day, and these teams are responsible for determining our quality standards are met.”
Throughout its international operations, Fowler says Ford boasts 60,000 Six Sigma “green belts,” more than 7,000 “black belts” and 400 master black belts. Six Sigma is a systematic approach to continuous quality improvement.
In the U.S., he adds, the United Auto Workers union continues to “step up to the challenge and assume more responsibility on the quality front as we trim plant personnel.”
And soon the auto maker will launch a new course at Wayne State University in Detroit, where Ford’s quality people will become certified as Six Sigma black belts.
“We’ve reached the point where we can advertise Ford’s quality as second-to-none of any full-line manufacturer,” Fowler says.
Fowler promises the newly aligned process will deliver best-in-class results when the auto maker launches its new Ford Focus in 2010, part of a dramatic production shift that will see the auto maker retool three light-truck plants in North America to build European-designed small vehicles in the region.
“Quality is the ultimate team sport,” Fowler adds. “This time, we’re playing for all the marbles, and we’re playing to win.”
About the Author
You May Also Like