Ford Flat Rock Plant Gearing Up for Fusion, Worker Training Under Way
The auto maker has invested $555 million in a fully flexible body shop capable of producing multiple vehicles and also installed a new paint shop.
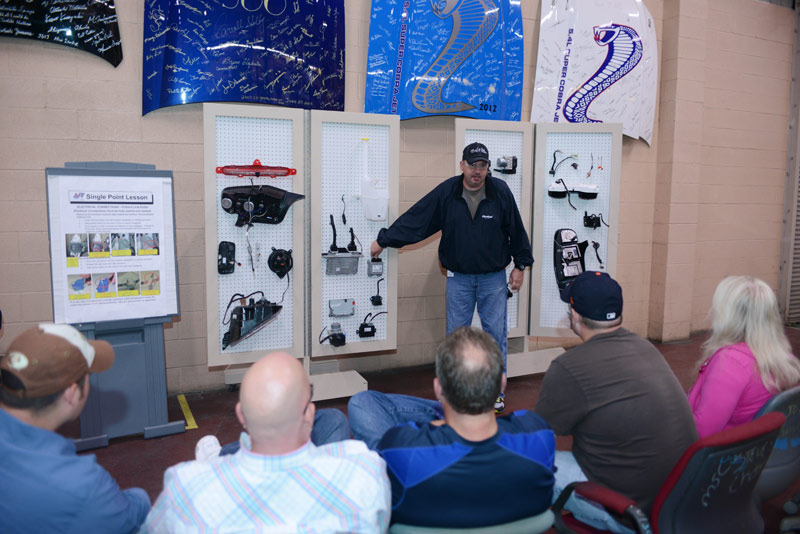
FLAT ROCK, MI – Ford is training 1,400 newly hired workers using simulated hands-on experience at a center within its auto plant here to prepare for assembly of the Fusion midsize sedan later this year.
The auto maker announced the new hires last fall following a decision to add Fusion assembly at the facility. The sedan currently is built at Ford’s Hermosillo, Mexico, plant.
Some employees undergoing training have been working part time or were displaced from other Ford plants, but about two-thirds are new hires who will receive an entry-level wage outlined in the auto maker’s agreement with the United Auto Workers union.
The training center allows workers to perfect tasks in simulation before they join the line, ranging from tightening nuts and bolts to more complicated assignments such as connecting brake lines or fitting weather stripping.
Before the training facility was established, workers went directly from the classroom to the assembly line.
“They were very nervous about what they were doing for the first time,” Tim Young, Flat Rock plant manager, tells reporters here. “Now they’ll…have some experience under their belt.”
Ford established the first training center at its Louisville, KY, plant prior to the launch of the ’13 Escape cross/utility vehicle, and is setting up a center its Kansas City, MO, factory, which is adding a new shift to increase F-150 pickup production.
The Fusion will account for roughly 50% of Flat Rock’s output once it launches this fall. The Ford Mustang has been the sole vehicle built here since the plant’s co-owner Mazda pulled production of its Mazda6 sedan last August. The factory presently is running at about 41% of capacity, WardsAuto data shows.
With the addition of the new workers, the plant will run on a 2-shift, 2-crew basis, but still not build to capacity, opening the door for a rumored new product to be added.
“Many of our plants are on a 3-crew operation, so there’s room for us to grow on this site,” Young says, while declining to confirm a new product.
To accommodate Fusion production, Ford invested $555 million in Flat Rock to build a fully flexible body shop capable of building multiple vehicles and to install a new paint shop.
The paint shop will utilizes Ford’s 3-Wet process, which allows three layers of paint to be applied one after another while still wet, resulting in a superior finish created with fewer pollutants and less expense, the auto maker says.
Young says infrastructure upgrades will allow the Fusion and Mustang to be built on the same line. “It’s extremely flexible when you look at the two vehicles. The Mustang is a rear-wheel-drive, 2-door car and the Fusion is a front-wheel-drive, 4-door vehicle.”
The fact that many of the workers at Flat Rock built the FWD Mazda6 sedan for years will help in the transition to the Fusion, he says. To gear up for Fusion production, Young, product planners, launch engineers and product specialists all have visited the Hermosillo plant to study assembly operations.
Because of the number of quality glitches with recent Ford models, including the Escape and Lincoln MKZ, greater attention will be paid to early Fusion production models at Flat Rock.
“If we do the early work at a very high quality level, it’s going to show in the final product,” Young says. “I think we’re seeing more focus up front.”
Read more about:
2013About the Author
You May Also Like