Ford Focus Features Hybrid Front End
Steel, aluminum and plastic seem so often to be locked into a life-and-death struggle for the hearts and minds of engineers, it's easy to overlook the fact they can in fact be used together.A good example is the hybrid plastic/metal design of the front-end module of the new subcompact Ford Focus, introduced in Europe last spring and due in the U.S. this fall.Designed by Ford, suppliers Dynamit Nobel
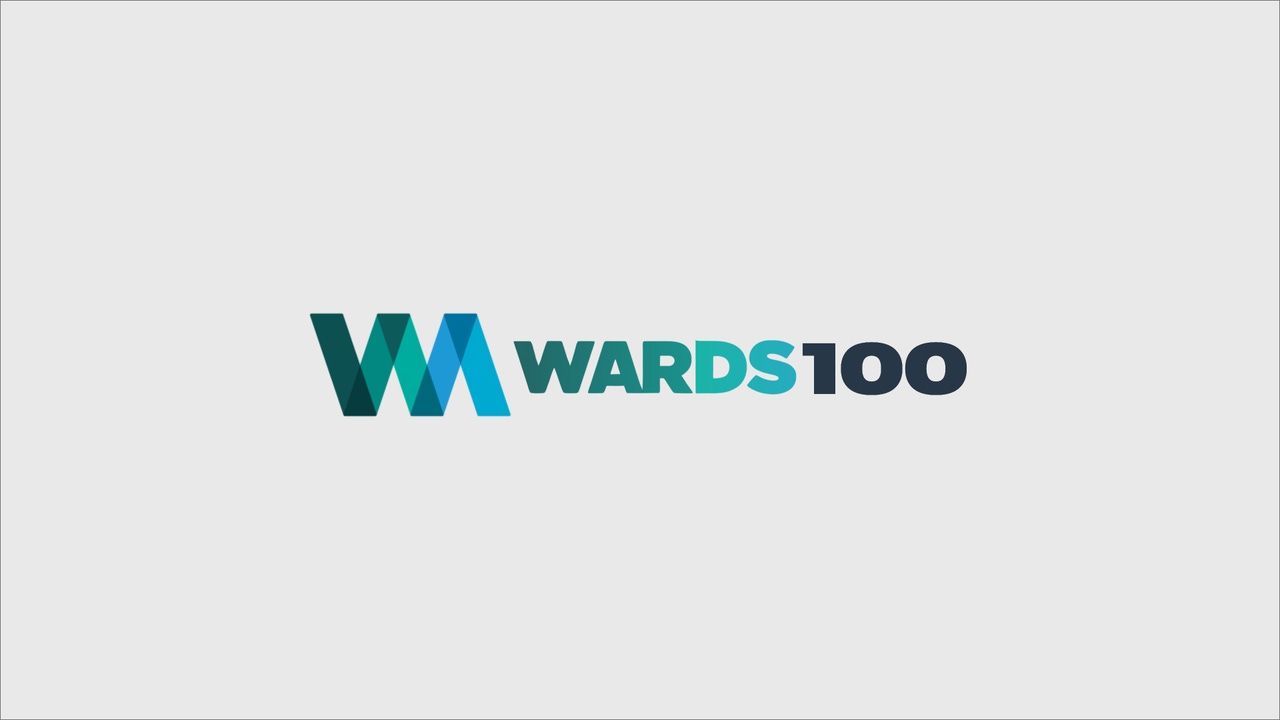
Steel, aluminum and plastic seem so often to be locked into a life-and-death struggle for the hearts and minds of engineers, it's easy to overlook the fact they can in fact be used together.
A good example is the hybrid plastic/metal design of the front-end module of the new subcompact Ford Focus, introduced in Europe last spring and due in the U.S. this fall.
Designed by Ford, suppliers Dynamit Nobel and mold makers Misslebeck used patented technology developed by Bayer AG for the front-end module. It combines the benefits of steel and plastic, yielding a hybrid part that is reportedly 40% lighter than if it were made completely of steel.
Compared with a pure plastic structure, it's more dimensionally stable and far less affected by factors such as material shrinkage, temperature and climate. Compared with a purely steel design, it eliminates the need for numerous high-tolerance jointing operations - and the costs they entail.
The front-end module incorporates brackets for components such as the radiator, condenser, headlamps, intercooler and headlamp washer nozzles, as well as anchoring elements like clips for attaching the bumper shell, hoses, lock cylinder, hood lock and a housing to protect the lock area.
It is assembled as the body is being manufactured, which means the plastic has to be able to withstand the high heat of cathodic dip coating and drying operations. The plastic is a glass-fiber-reinforced polyamide material.
The part is made by inserting a deep-drawn perforated steel sheet into a typical injection mold. During the injection cycle, the molten plastic flows into and around the perforations in the metal, forming a series of "rivet heads" between the mold wall and the metal. In this way, a high strength composite structure is created between the plastic and the metal, which is interlocked. No adhesion promoter is required.
Furthermore, the finished component is easily recyclable, Ford and supplier sources say. A conventional hammer mill can be used to break the part into small pieces, after which the two materials can be separated with close to 100% efficiency by means of a screen and a magnetic separator. Test specimens manufactured from the recycled plastic display properties almost equal to virgin material, Bayer says.
About the Author
You May Also Like