Ford Forges Own Electrified Vehicle Development Path
Ford says by developing core electrified-vehicle expertise in-house and outsourcing in other areas it is able to quickly adopt new technologies.
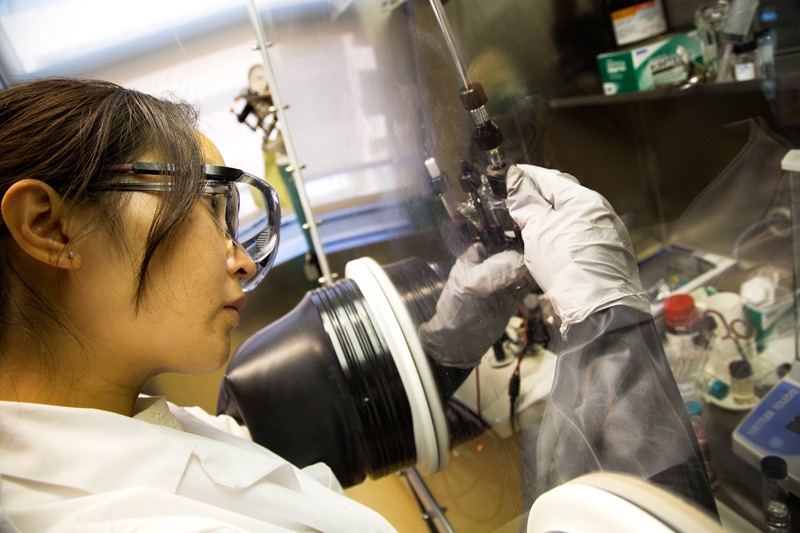
DEARBORN, MI – Ford takes a careful, well-balanced approach with its electrified-vehicle program by partnering with suppliers where it makes sense and bringing work in-house when most beneficial, a top researcher says.
The strategy gives Ford control over areas it considers critical, while depending on suppliers to contribute in their particular areas of expertise. Most importantly, it keeps the automaker one step ahead of its competition, says Anand Sankaran, chief engineer-energy storage and hybrid systems.
“We strongly believe in focusing on things that will differentiate ourselves at the vehicle level,” he says during a media backgrounder here. “We’re not in the business of making silicon or battery cells. We have chosen to do this differently than other OEMs.”
Some automakers are closely tied to a particular technology, because they have invested heavily and can’t afford to pull back, Sankaran says. Ford’s approach allows the automaker to quickly take advantage of technological breakthroughs in areas such as battery chemistries.
“Trying to do everything locks you into very specific technologies,” Sankaran says.
Sankaran points to Ford’s evolution from the first Escape hybrid to the last-generation Fusion hybrid as an example of the automaker’s rapid technology strategy.
“From 2004 to 2009, we changed the cell technology three times because better cells were available every second year and we wanted to bring them in as quickly as we can,” he says. “And we’re doing the same thing (now)."
Another area Ford lets suppliers handle is development of insulated-gate bipolar transistors, devices that rapidly transfer power to the different parts of the electrified powertrain to optimize efficiency.
While critical to the operation of an EV, developing IGBTs is not in Ford’s future, Sankaran says.
“We know how the physics work in IGBTs, so we’re very good at this in terms of the experts and tools we have,” he says. “But we want to be better than everybody else when it comes to applying these technologies in cars so we can get the most out of these cells.”
Ford currently sources IGBTs from a number of suppliers, including Infineon, Hitachi, Renesas and Toshiba.
Sankaran says the automaker’s supply base keeps developing smaller, more-efficient battery cells and IGBTs, and he expects more can be squeezed out of the technologies. However, when it comes to the electric motors used in electrified powertrains, there’s probably not much more room for downsizing because they utilize rare-earth metals.
“You need that much copper,” he says. “You can design it to use less rare-earth metals, but because it’s a lot older technology it’s harder to squeeze costs out.”
In addition to working closely with a number of suppliers on key electrified powertrain technologies, Ford also teams with numerous research universities around the globe, including Rheinisch-Westfälische Technische Hochschule Aachen, in Aachen, Germany.
The latest collaboration is with the University of Michigan, which together with Ford and the U.S. Department of Energy recently opened a new $8 million battery lab. Ford contributed $2.1 million to the new facility, which will allow researchers to develop batteries for future electrified vehicles without the automaker bringing the work in-house.
“It is way too early in the battery race to commit to one type of battery chemistry,” Ted Miller, senior manager-energy storage, materials strategy and research, says. “In the span of 15 years, the industry has gone from lead-acid to nickel-metal-hydride to the lithium-ion batteries used today. Others in the auto industry have placed their bets, but we are convinced a better solution will require input from a multitude of partners.”
The new U-M lab will be a pilot-scale battery-manufacturing facility that will test battery chemistries to determine their future potential for production vehicles, allowing for faster implementation should they prove superior to today’s technology.
Miller says Ford has inked an intellectual-property agreement with U-M, which allows university researchers to tap into the automaker’s knowledge.
“In some cases somebody is experimenting with something proprietary,” he says. “So they’ll enjoy the same protections that Ford has through the intellectual-property agreement.”
The U-M lab, slated to be fully operational next year, is expected to attract battery suppliers who want to work on problems in a neutral setting, Miller adds.
“I think you are going to see a lot of companies in the battery-supply chain come to Michigan to use this facility in a very short order.”
Read more about:
2013About the Author
You May Also Like