Ford India Workers Emulate Gandhi in Pay ProtestFord India Workers Emulate Gandhi in Pay Protest
Recalling Mahatma Gandhi’s non-cooperation strategy that won independence for India in 1947, the Ford employees are showing up for work but are refusing the company’s offers of a free lunch and free round-trip transportation to and from their homes.
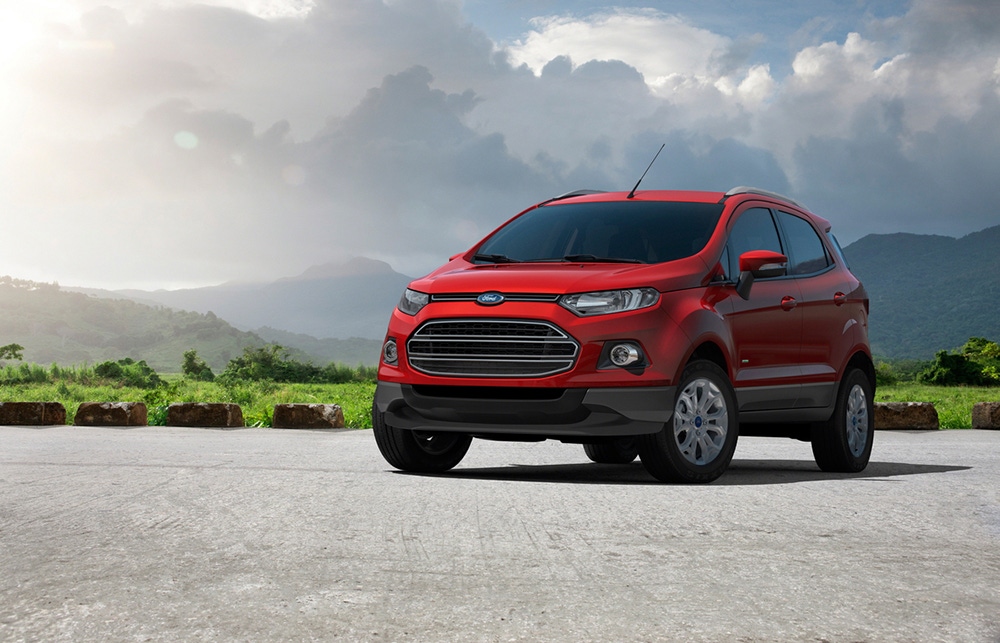
MUMBAI – Unrest among Indian auto workers has become commonplace, but because of one group’s unorthodox tactics the protests do not have commonality.
A more or less typical situation is playing out at Toyota Kirloskar’s Bangalore plant. Workers’ demands for higher pay have been accompanied by a lockout, suspensions, employee sit-ins and production by of a mere 120 vehicles a day, a fraction of the facility’s capacity of 1,000.
Few if any automakers in India have avoided labor trouble. In recent years Maruti Suzuki, Honda India, General Motors India, Hyundai India and local manufacturers Tata and Mahindra & Mahindra have dealt with fractious employees.
The low point arguably came in the summer of 2012, when the Maruti plant in Manesar was shut down for a month by a strike in which a manager was burned to death and more than 100 other supervisors were injured. India’s largest automaker lost at least 35,000 units of production.
At Toyota Kirloskar, workers recently demanded a pay increase of Rs8,000 ($140) per month but said they would accept half that amount. In mid-March employees were locked out and 30 of them were suspended. After the government intervened, the wholly owned Toyota subsidiary agreed to raise salaries Rs3,050 ($50), but only on condition that every employee sign a future ‟good-conduct” pledge, and that the 30 suspended employees not be taken back.
Rejecting the offer, 20 leaders of the Toyota Kirloskar Motor Employees Union late last month began fasting in protest; 10 have been hospitalized with low blood pressure and blood-sugar levels. Other employees have held sit-ins outside the plant gates.
This week the leaders called off their indefinite fast and instead are joining the rank and file in daily morning-to-evening fasts by rotating groups of workers.
Management has not yielded, instead using a skeleton crew of supervisors and temporary contract workers to maintain drastically scaled-back production. That in turn has prompted complaints from union officials that TKM is using untrained apprentices, a charge denied by the automaker. Government inspectors are investigating the conflicting claims.
Ford Protests Follow Peaceful Path
At Ford India’s Chennai plant, workers are protesting a cut in performance bonuses from 26% of their salaries in 2012 to 15.8% last year, even as production increased 15% to 122,000 units in 2013.
Employees, however, are staging neither mass absences nor line slowdowns. Instead, union representatives say the workers are refusing the company’s offers of a free, good-quality lunch and free round-trip transportation to their homes as far as nine miles (15 km) away.
The Ford employees' peaceful protests recall the nonviolent non-cooperation movement pioneered some 85 years ago by Mahatma Gandhi and which won India independence from British rule and occupation in 1947.
The nonviolence perhaps may honor the long tradition of creative teamwork, sensitivity and mutual respect between Ford India and its workers. Prescribed standards and criteria are known to, and observed by, both sides. In this way trust and fellowship are preserved, making management’s cutback in performance bonuses all the more surprising.
The automaker has said performance incentives are determined following discussions and communication with employees, who are encouraged to ask questions of managers. But the key to the current strife is found in a recent Ford India statement that ‟there are multiple dimensions in determining performance metrics, which vary year to year, based on internal and external factors.”
Workers suspect Ford is downgrading productivity as a criterion in determining performance incentives in a year in which it increased 15%. The automaker appears to be risking a long and valuable tradition of mutual trust and industry best practices for the sake of saving some money.
Some behavior analysts say management has failed to see that the new, urban blue-collar worker is not the uneducated rural youth taking any job that comes his way, but rather has education, skills and awareness of his surroundings.
Toyota Kirloskar and Ford India can ill afford labor problems as they expand their production footprint.
TKM has sold 1 million light vehicles during its 16 years in India and has invested Rs40 billion ($670 million) to create capacity for 310,000 units. It plans to spend another Rs60 billion ($1 billion) to raise capacity to 400,000 units and add a contemporary diesel engine plant.
Ford India has invested nearly Rs120 billion ($2 billion) in the Chennai facility and the upcoming Sanand plant in Gujarat state. The Sanand factory directly will employ about 5,000 people when production launches in early 2015. The plants will have combined capacity of 440,000 vehicles and 610,000 engines.
Ford India has received 60,000 bookings for its newly launched EcoSport compact CUV, of which 30,000 still are pending. The automaker plans to increase its sales and service outlets in coming years from the current 304 in 164 Indian cities to about 500 and to export to 50 countries in Asia, Africa and South America.
Read more about:
2014About the Author
You May Also Like