Ford Latest Auto Maker Landed by India’s Gujarat StateFord Latest Auto Maker Landed by India’s Gujarat State
The India plants are a part of the U.S. auto maker’s goal of increasing worldwide sales nearly 50%, to 8 million units, in the next three to four years.
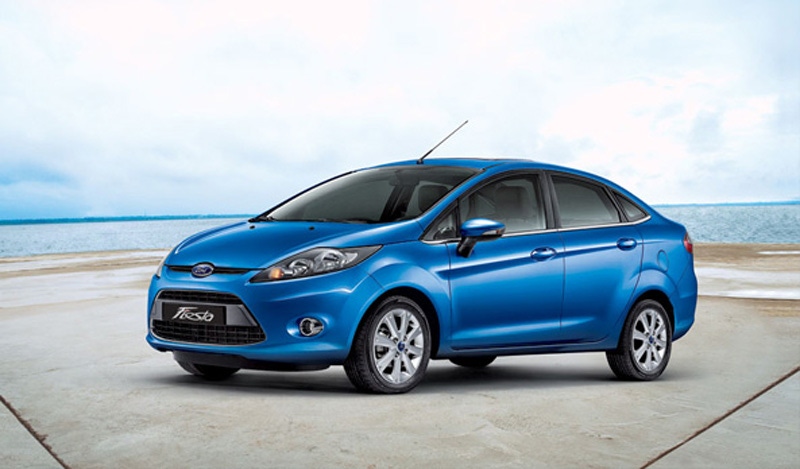
MUMBAI – Ford India launches construction of two state-of-the-art plants at Sanand, one with production capacity of 240,000 vehicles and the other capable of making 270,000 engines annually.
The auto maker initially is investing Rs50.7 billion ($1 billion) in the project as it aims to double production and employment in India over the next three years.
The new plants also are a part of Ford’s strategy of increasing worldwide sales nearly 50%, to 8 million units, in the next three to four years, says Joe Hinrichs, president and CEO-Asia/Pacific and Africa.
“This expansion will allow us to provide technologically advanced and fuel-efficient engines and vehicles,” adds Michael Boneham, president and managing director-Ford India, in a statement.
The auto maker has not specified which vehicles will be built at Sanand when the plants come on line in 2014. Ford introduced the all-new Fiesta subcompact in India in September 2011 and plans to offer seven other models in the country by mid-decade.
The new Sanand factories are another step in Ford India’s transformation into a global manufacturing and export hub. “This is an investment in the future of Ford globally,” Hinrichs says.
The auto maker’s Indian subsidiary already exports its Figo compact car to 34 countries and says it may export its EcoSport SUV to as many as 100 markets worldwide. But Ford India still is trying to gain a foothold in its home market.
Despite investing Rs58.8 billion ($1.16 billion) over the past 17 years in its two Chennai plants in south India, with annual capacity of 200,000 vehicles and 330,000 engines, Ford’s share of the dynamically growing Indian market was just 1.8% at the end of 2010.
Counting exports, however, the auto maker’s share in March was 4.6%, up 155% year-over-year, according to the Society of Indian Automobile Manufacturers.
Ford India has made a valuable and lasting contribution to its U.S. parent’s fortunes. Its innovations in manufacturing technology and shop-floor management have been applied to global Ford plants, saving resources, curtailing costs and contributing to profitability.
Ford India is the first Ford subsidiary to introduce a single flexible production line for manufacturing gasoline and diesel engines and a flexible crankshaft line for the two kinds of engines. Ford has decided to install similar lines at its new plants worldwide.
The Chennai engine factory manufactures five Duratec gasoline-engine variants and one Duratorq diesel powerplant. Two years ago, gas engines comprised 70% and diesels represented 30% of vehicle sales in India. Those proportions are reversed today, but the plant’s flexibility allows it to respond without delay and without requiring new investment.
Most automotive assembly lines are dedicated to run one model at a time, forcing the entire engineering setup to be reset for production of a different model. Ford India coded the parts and used sensors at Chennai to run the six engine types at once on the same line.
This cuts down on clutter on the shop floor and allows simultaneous output of engines for vehicles sold domestically and for export.
Ford India also has incorporated flexibility into its trim and final-assembly operations, allowing it to automatically accommodate 600 variants of vehicles. Its vendors developed coding and software designed to match the right component with the right car without delay.
With specifications matched correctly, over-engineering of standard parts for assembly operations is eliminated, saving money, time and weight. Flexibility also saves expensive shop-floor time and space, plus substantial freight and storage costs.
According to Boneham, innovations in paint technology at Chennai have reduced fuel consumption 30%, water use 50% and emissions 20%.
A third shift is being added at the Chennai facilities. After the Sanand project is completed, Ford India’s workforce will total 15,000 including backroom researchers and information technology specialists.
Says Boneham, “The new facility at Gujarat will complement our world-class facilities and operations in Chennai.”
Ford India selected the Sanand site because of the state of Gujarat’s pro-business environment, developed infrastructure, access to the ports of Mundhra, Kandla and Pipavav within a 150-mile (240-km) radius and a large and growing components industry.
Sending vehicles to Northwest India from Chennai took 10 days; travel time now will be cut to less than half.
Gujarat’s automotive hubs are Sanand, where, in addition to Ford, PSA Peugeot Citroen plans to build a plant and Tata already is building Nano cars. Maruti Suzuki has selected a site in Mehsana and Halol is home to a GM India factory. All are connected with the three ports, whose modern facilities include roll-on/roll-off loading and unloading of cars.
The Gujarat Industrial Development Corp. has a land bank of 5,000 acres (2,000 ha). It will have a surplus available even after allocating 3,500 acres (1,400 ha) to the five auto makers, ensuring there will be no land-acquisition hassles and no disputes with farmers, unlike West Bengal.
Read more about:
2012About the Author
You May Also Like