Ford Looks to Expand Virtual DesignFord Looks to Expand Virtual Design
Currently, about 40% of Ford’s testing is done virtually, with about 5%-10% of that conducted without the need of a physical prototype.
April 16, 2007
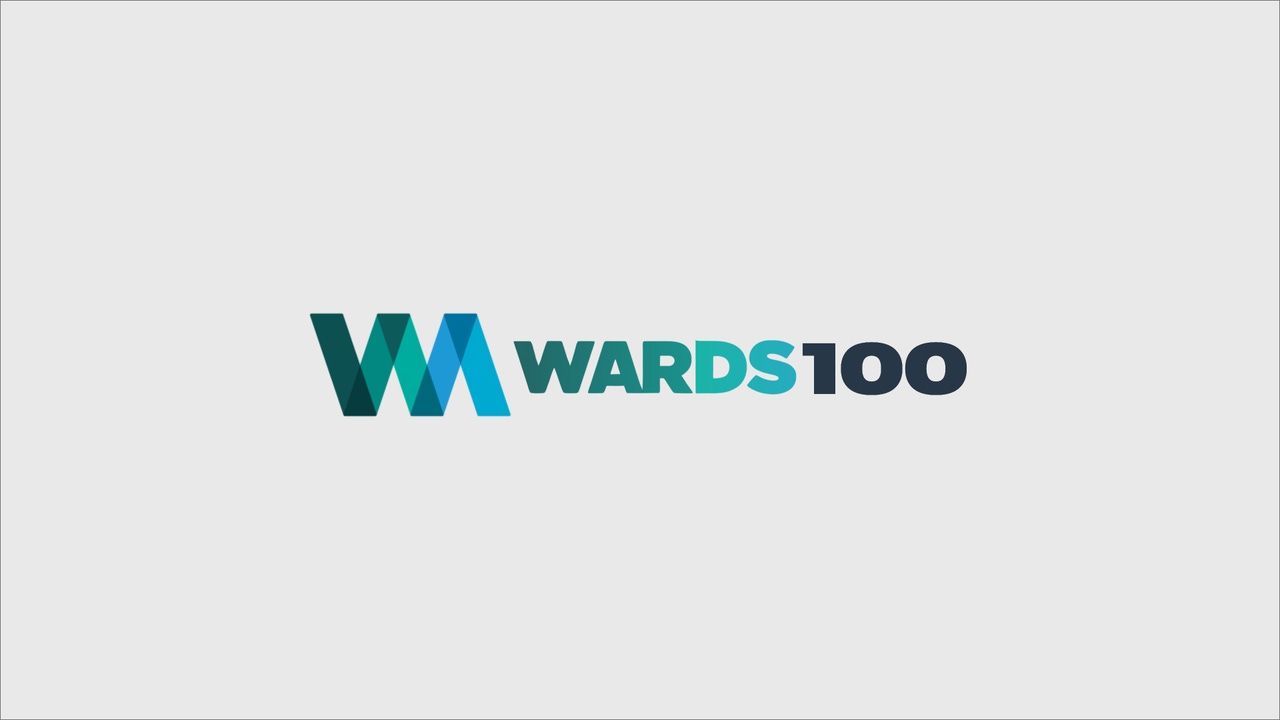
Special Coverage
SAE World Congress

DETROIT – Ford Motor Co. says it has its eye on doubling use of virtual testing and eliminating more of the prototype parts created and physical testing it performs, as it looks to speed product development and cut costs.
The movement is a further refinement of the new Global Product Development System the auto maker first began formulating three years ago.
Speaking as part of a panel on total vehicle integration here at the SAE International World Congress, Paul Mascarenas, vice president-engineering, says Ford currently uses virtual testing for some 40% of its processes.
Flex first from Ford’s new program development process.
About 5%-10% of those tests are conducted without Ford producing a physical prototype to verify results, what Mascarenas refers to as 100% probability testing.
“We would like to move a significant percentage of our assessments to virtual (testing),” Mascarenas says. “Then the real interest is to push up the probability testing.”
He says Ford is targeting 80% of testing to be virtual.
Although he declines to provide a specific timetable, Mascarenas tells Ward’s he expects Ford to be at the 80% level in “three to five years.” But he says the movement to 100% probability testing within that will occur even faster.
“We’re starting to trust the data,” Mascarenas says of the virtual test results.
Key to all this is computer power, industry executives say.
“Virtual testing is limited by processor speeds, not methodology,” says Carsten Saager, general manager-metals, coatings, specific materials for BMW AG and a member of the panel here. “But times are changing and speeds are going up.”
“We’ve got to get capable computers,” Mascarenas agrees.
Ford’s new Flex cross/utility vehicle, which was unveiled at the New York auto show earlier this month and will go on sale in summer 2008 as an ’09 model, is the first vehicle engineered entirely via Ford’s new global development process, Mascarenas says.
Asked how quickly Ford designed the Flex using the new processes, Mascarenas declines to be specific. But he points out the vehicle was rolled out in concept form at the Detroit auto show in 2005, and development now is winding down.
“The Flex has been on the drawing board for a couple of years,” he says. “(Development time) all depends on the scale of the program. But that’s pretty typical of what we’ll be able to do with a carryover platform with a new top hat, a new instrument panel and new seats.”
The Flex shares its platform with the new ’08 Ford Taurus sedan, itself a derivative of the Volvo P2 platform that underpins the Volvo XC70.
Ford’s new product-development process also cuts the number of vehicle prototypes the auto maker needs during vehicle development.
“We used to have three to four prototype phases; now there are just two,” Mascarenas says. Those include an underbody prototype, where the vehicle chassis and powertrain are tested, and a complete vehicle prototype phase.
Read more about:
2007About the Author
You May Also Like