Ford Studies Soy Byproducts
FORD MOTOR CO. HAS MADE SIGNIFICANT progress in using soy oil in place of petroleum in some automotive foam but now faces the dilemma of what to do with the leftover portions of the soybean. When a soybean is crushed, it results in only 18% soy oil, which Ford uses in foams and some sheet-molding-compound material. The remaining 82% is soy meal and soy flour. So when Ford starts implementing the soy
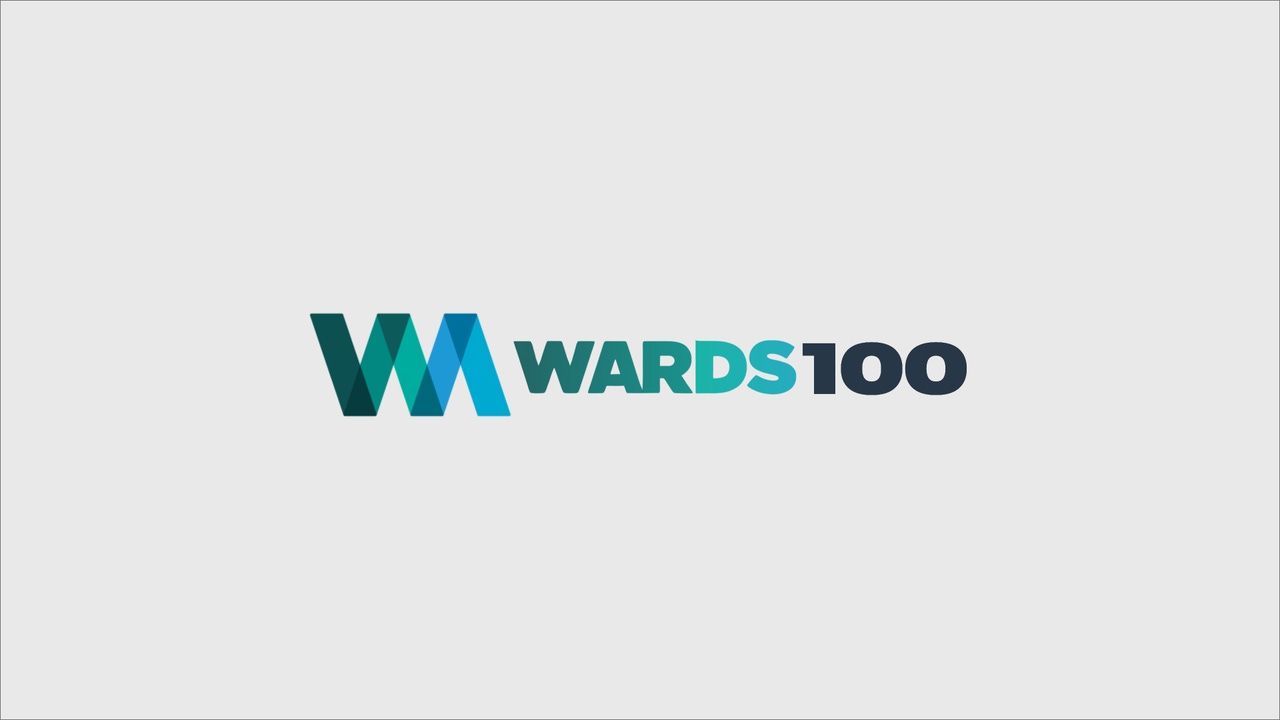
FORD MOTOR CO. HAS MADE SIGNIFICANT progress in using soy oil in place of petroleum in some automotive foam but now faces the dilemma of what to do with the leftover portions of the soybean.
When a soybean is crushed, it results in only 18% soy oil, which Ford uses in foams and some sheet-molding-compound material. The remaining 82% is soy meal and soy flour.
“So when Ford starts implementing the soy foam everywhere, we're going to have a lot of soy meal around,” says Debbie Mielewski, technical leader for Ford's materials research and advanced engineering department.
Mielewski, speaking at the recent Society of Plastics Engineers Automotive Composites Conference in Troy, MI, says Ford is considering employing the soy residue in a “variety of matrices” as filler for automotive plastics.
Some possibilities include using the soy material in place of petroleum in plastic parts such as pillars, bumpers and splash shields.
“With 12%, 18% and even 24% soy meal and soy flour (used in place of petroleum-based reinforcements), you don't lose that much in chemical properties,” Mielewski says. “We're not ready to implement it. But for the first shot at trying, it's not half bad.”
The parts are nearly indistinguishable from their petroleum-based counterparts, she says, but warns higher concentrations of the soy material can lead to a drop-off in mechanical properties.
“We still have a long way to go,” she says.
Ford's use of soybeans to create materials from plant-based sources dates back to the days of founder Henry Ford, who experimented with the alternative material and was determined to team up with farmers and “use things that could be grown,” Mielewski says. He even had a suit made from soybeans.
The auto maker's latest foray into soybean use began nearly nine years ago, when Mielewski's group started working on replacing petroleum with soy oil in seat foam.
Developed in conjunction with supplier Lear Corp., the foam first debuted in the '08 Mustang.
Not all the material used in the seat foam is soy-derived, however. Because of the properties inherent to soy, only 12% of the organic material is used in the foam, which now also is employed in the Ford Expedition and Lincoln Navigator SUVs, Ford F-150 fullsize pickup, Focus small car and Lincoln MKS sedan.
In addition, soy foam is being used in the headliner of the '10 Escape cross/utility vehicle.
“We're utilizing soy foam on over 1 million vehicles per year now,” Mielewski says, noting the replacement of petroleum-based foam results in the reduction of 5.3 million lbs. (2.4 million kg) of carbon dioxide annually, which is the “equivalent of about 10,000 seedlings” growing for 10 years.
“We're reducing the amount of petroleum by about 1 million lbs. (454,000 kg) per year,” she says.
But exceeding the 12% soy oil penetration rate in automotive foam will take further research, especially considering the obstacles that had to be overcome to bring the material to production.
The initial soy foams “smelled a bit like rancid popcorn,” she says. “That odor had to be reduced, removed or covered.”
The foam also was easy to tear and stained easily due to flaws in its microstructure.
To reduce the odor, Mielewski and her team deployed a “thin-film evaporation” method, which removed the low-molecular-weight materials determined to cause the stench.
Addressing the microstructure problem required a more complex solution.
“There are about 15 different components in automotive foam, and (we) had to optimize the blowing and jelling reactions by altering those 15 components,” she says. “But after several years of optimization, it looks identical in microstructure to the petroleum-based foam it replaces.”
Mielewski says her team's research began garnering more attention when gasoline prices eclipsed $4 a gallon last year. Prior to that, “no one invited us to the party.”
“We want to increase the use of renewable feedstock — things we can grow in this country — and reduce dependence on foreign petroleum,” she says. “All the plastics in a vehicle are derived from petroleum ultimately.”
While critics have argued using agricultural feedstocks for plastics and alternative fuels will drive up the price of food, Mielewski says using crops for automotive purposes makes sense.
“If we don't develop alternatives (to petroleum), we're going to be in bigger trouble because we'll be stuck with the petroleum material that is obviously going to run out,” she says. “Everything I've learned for soy can be used for castor oil or any oil. So I think in the long run we'll decide what makes sense and what doesn't.”
Plant-based plastics also are compostable, she says, noting soy-based materials decompose in 90-120 days once buried, while petroleum products linger in landfills for decades.
Mielewski says her vision is for all automotive plastics to contain organic material, although she questions whether “I will live to see that day.”
But her work has inspired others to begin researching the use of plant-based materials, which she sees as a step in the right direction.
“Everybody else is contributing like crazy now,” she says, “so I think the critical mass (of research) will allow us to come up with solutions that are amazing.”
Ford Developing Biodegradable Plant-Based Components
subscribers.wardsauto.com/ar/ford_biodegradable_components
Ford's Soy Seats Say Green, But Don't Save Green
About the Author
You May Also Like