Ford to Expand Use of 3-Wet Paint Technology; 2-Wet Process to Debut on CVs
First launched in 2007 at Ford’s Avon Lake, OH, assembly plant, the technology allows solvent-borne paint coatings to be applied wet, instead of heating and drying each layer individually with energy-consuming ovens.
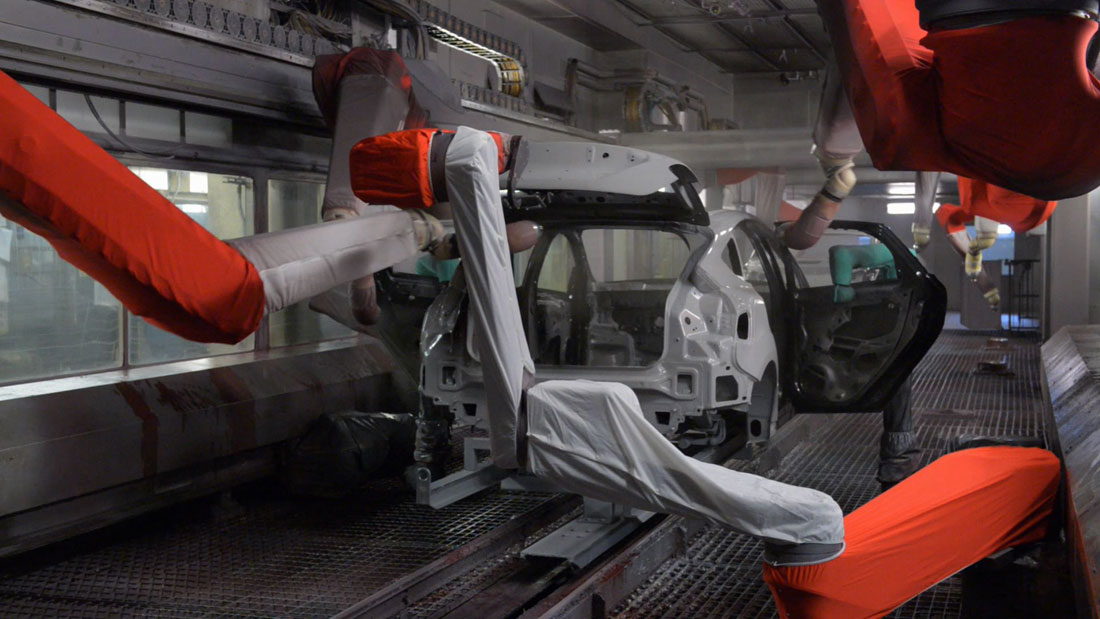
Ford says it’s expanding the use of its innovative 3-wet paint process 50% and is preparing an even more efficient version of the technology.
First launched in 2007 at the auto maker’s Avon Lake, OH, assembly plant, the 3-wet process allows solvent-borne paint coatings to be applied wet, instead of heating and drying each layer individually with energy-consuming ovens. A simple integrated booth replaces multiple stages in the paint shop.
Ford says the process can reduce paint shop carbon-dioxide emissions 15%-25% and volatile-organic compounds 10%, compared with conventional paint processes.
Because of the smaller paint booth, less electricity is required for the blowers that circulate massive volumes of air, and less natural gas is needed to heat the air and ovens.
The result of the 3-wet process is a high-quality, durable finish, says Mike Boss, chief engineer for global paint. “We spend a lot of time with paint and material suppliers looking at initial quality and long-term durability, and this is superior to prior procedures.”
The technology has exceeded Ford’s expectations for CO2 and VOC reduction because vehicles typically only need to be painted once, compared with the earlier process that required touch-ups.
“Traditionally, we’d have a first run of 95%, where 5% required touch-up or adjustment,” he says. “This (3-wet paint system) has a 99% first run, which goes back to quality and efficiency for the environment. We only paint them on time and paint them correctly.”
Ford’s 3-wet paint technology is used in four North American assembly facilities, three in Asia-Pacific and one in Europe. This year, the process will be implemented at an additional four plants, located in Michigan, Missouri, China and Spain.
“We have a global road map that’s tied to a cycle plan, and our intent is to have this at every site,” Boss says. “We have been aggressive to spread it through the world.”
Ford is reducing the cost of installing the 3-wet paint process by adding it at facilities that are scheduled to receive upgrades for new products, or are new plants in emerging markets such as China and India.
The next step in streamlining Ford’s paint process is 2-wet technology, which will debut on the Transit fullsize commercial van to be built in 2014 at the auto maker’s Kansas City, MO, assembly plant.
Bruce Hettle, Ford executive director-global manufacturing engineering, says the technology further streamlines the paint process by applying just primer and a top coat and eliminating the clear coat.
Plans call for 2-wet to first be used for commercial vehicles, Hettle says, noting the process has resulted in a superior paint appearance, with competitive “scratch and chip” attributes.
“We’ve seen no differences (from 3-wet) and long-term durability is great as well,’ he says. “From a material composition and durability standpoint it’s better than prior coating surfaces, and that’s what our external and internal data tells us.”
Hettle declines to say whether 2-wet will be used on Ford’s non-commercial, retail vehicles, but doesn’t rule out the possibility.
“When we started…this, we continued to pull innovation levers and made our investment and environmental footprint less,” he says. “So I don’t think we’re done, but I don’t know what the next steps are.”
About the Author
You May Also Like