Materials: Boxed InMaterials: Boxed In
NORTH BALTIMORE, OH - It's five hours from this small town south of Toledo to Louisville, KY, and the big trucks are loaded and ready.Each truck will transport 33 sheet-molded composite (SMC) pickup boxes for the new Ford Explorer Sport Trac, a sport/utility vehicle (SUV) hybrid reaching dealerships this month, which is assembled at Ford's Louisville truck plant.The boxes are molded at the Budd Co.'s
March 1, 2000
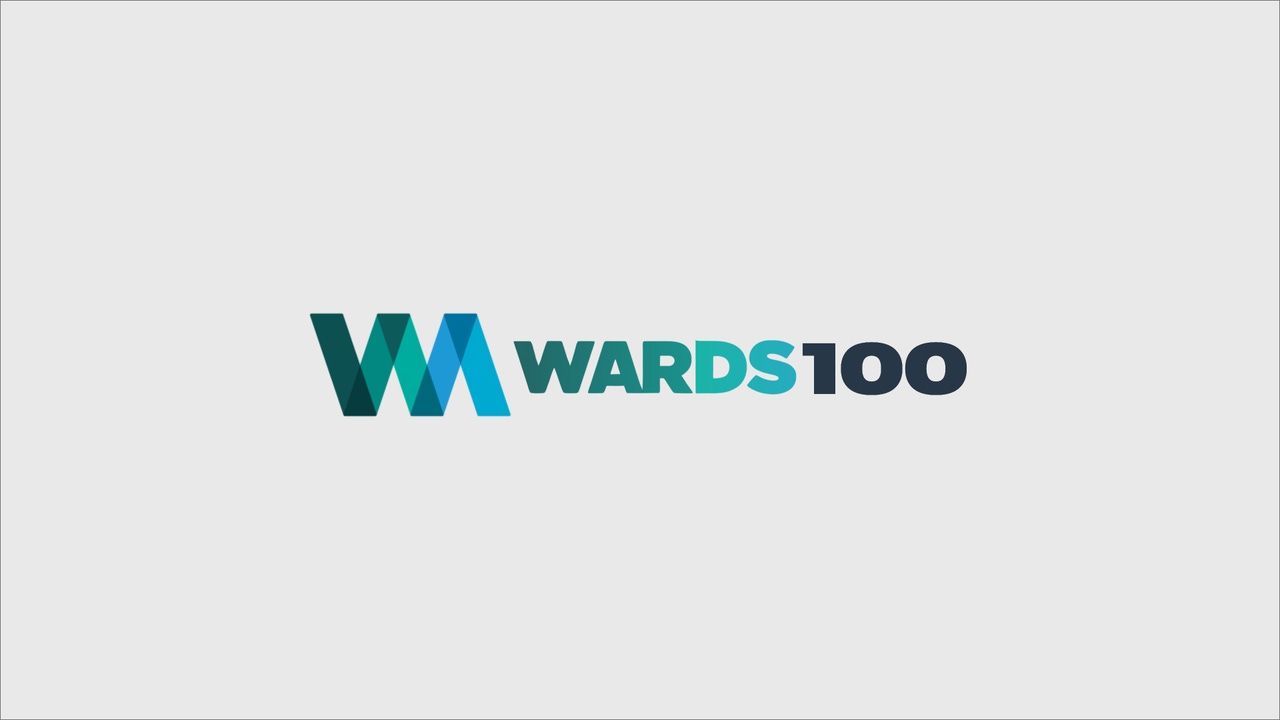
NORTH BALTIMORE, OH - It's five hours from this small town south of Toledo to Louisville, KY, and the big trucks are loaded and ready.
Each truck will transport 33 sheet-molded composite (SMC) pickup boxes for the new Ford Explorer Sport Trac, a sport/utility vehicle (SUV) hybrid reaching dealerships this month, which is assembled at Ford's Louisville truck plant.
The boxes are molded at the Budd Co.'s vintage-1973 plant here using technology developed by Ford, Budd and Owens-Corning Corp. The SMC base material is compounded at Budd's Van Wert, OH, facility of a thermoset resin, O-C glass fiber reinforcement and filler, then shipped here in rolls for molding.
Sport Trac is the first vehicle to offer a plastic "open-cargo" box, and it's the largest automotive SMC component ever designed. It contains 50% glass fiber, and is said to weigh 20% less than steel. Sport Trac will be priced at around $23,050 for the 4x2 version, $25,802 for the 4x4.
Next fall General Motors Corp. will offer an even larger plastic box as an option on its full-size Chevrolet Silverado extended-cab pickups. The SMC inner box and tailgate will be fabricated by Cambridge Industries as one-piece molded components in Huntington, IN, using a new glass fiber supplied by Owens-Corning. Budd will make the flexible outer panels for the box and tailgate here using a flexible RIM (reaction injected molding) composite.
In July, Budd will begin making the fenders, tailgate and wheelhouses for the heavy duty versions of the '01 Silverado HD/Sierra.
Ford, GM and numerous suppliers have been working on plastic pickup boxes for more than 20 years, all seeking the same chief advantages: Lighter weight, freedom from rust, parts consolidation and greater design freedom.
That design flexibility is one reason Ford's upcoming Thunderbird, due out in late 2001 as an '02 model, is expected to use large amounts of SMC. Sources say T-Bird's interior door trim panels, front fenders, hood (complete with air scoop), and trunk lid, will be made of plastic. So too will the front and rear fascias. These parts are expected to be made by Budd, likely at the company's Kendallville plant in Indiana.
A recent tour of O-C's Toledo headquarters and Budd's facility here focused on Sport Trac, which Ford forecasts will generate 65,000 sales annually - relatively low volume that best suits the SMC process.
Think of Sport Trac as an Explorer chopped off behind the rear doors with a cargo box measuring 51 ins. (130 cm) in length added on the back, providing 29.6 cu. ft. (838.2 L) of cargo space.
Ford retains the steel tailgate from its F-150 large pickup, but the gate's inner panel is made of SMC to match the floor of the box. Both the inner box and gate liner are painted black and designed to withstand pounding, so a separate liner is not needed. The outer SMC box panels go down the same paint line as the vehicle's steel body.
For longer or larger loads, Ford developed a U-shaped stainless steel "Cargo Cage" that slips over the lowered tailgate, stretching the overall cargo area to more than 6 ft. (1.8 m).
The SMC box features several other innovations, including an SMC divider that splits the box's usable space for varying cargo requirements. It also contains 10 cargo hooks - each capable of holding 700 lbs. (320 kg) - to tie down cargo; a 12-volt power point to operate tools and outdoor equipment; and even a hook that can be used to open bottles, bringing a new dimension to football "tailgate" parties.
Budd also molds an optional Sport Trac tonneau cover using an SMC composite containing 28% glass to withstand harsh punishment. The tonneau is made in two pieces mated via a piano hinge, and can be locked using the vehicle's door key. It's also waterproof.
Aftermarket suppliers typically produce tonneaus, but Ford opted to engineer the component itself to match Sport Trac's sporty appeal and to provide ample security.
The trail from concept to production has been a long one for Pete Miskech, technical specialist in Ford's Body Structure Systems Technology unit.
"We started out early in 1986 as a pilot program to demonstrate that SMC would work as a structural substrate in light truck boxes," he recalls. "We also wanted to reduce SMC (component development) cycle times.
"We took it to Louisville and showed that it could go through the paint lines and that it could be assembled on the same equipment (used for steel) and with the same people."
But a long road lay ahead. Ford ultimately built 400 trucks with SMC boxes. "We used them for research and sold some to 'unsuspecting' customers; we were selling $50,000 pickups (Ford's cost)" at regular retail prices. Later, when Ford sought to pull back the pickups for research, "we couldn't retrieve a single one," he says, implying the "unsuspecting" customers liked what they purchased.
Over the years Ford kept some of the experimental trucks stored in chambers ranging from -40degreesF to +160degreesF (-40degreesC to +71degreesC). "At -40degrees it's much stronger than steel and at +160degrees it retains 80% of its strength," says Mr. Miskech.
One advantage of the long gestation: Ford tested the material for ultraviolet damage over a nine-year period. "There was no chalking or other deterioration," he reports.
Ford engineers also demonstrated that they could go from SMC pickup box design to production in 24 months, one of their primary original goals, and otherwise tested the material for structural integrity. It was tortured in such devious tests as the "hammer drop," "rake and grind," "shovel slide" and "drum drop," escaping virtually unscathed. In all, Ford rolled up the equivalent of 450,000 miles (720,000 km) of testing. Budd added 150,000 miles (240,000) of its own testing.
Parts consolidation was a primary motive, says the Ford engineer. The SMC inner box would've required 33 separate parts in steel. "Normally (in steel) it costs for separate tools for each part - plus the costs of putting them together. We figure we have a five-to-one advantage in investment costs" by selecting SMC over steel, he adds.
Then why did it take so long? "We can make an 8-ft. (2.4-m) box today, but in 1986 we could only make small (SMC) parts," says Mr. Miskech.
Michael F. Dorney, Budd Plastics Div. vice president-sales and marketing, says Budd could produce 80,000 to 100,000 Sport Trac boxes annually - and possibly even more - if demand rises that high. North Baltimore employs 250 workers represented by the United Auto Workers union on three shifts, five days a week, producing 90 million lbs. (41 million kg) of SMC components yearly.
About the Author
You May Also Like