Now That's a Diet!
Most supplier executives would do cartwheels if they discovered an affordable way to shave just a pound off their products. Even before gasoline prices started their recent ascent, fuel efficiency was a high priority for automakers, so suppliers have been on constant watch for any opportunity to reduce weight.Supplier Hayes Lemmerz Intl. Inc. has joined with the American Iron and Steel Institute (AISI)
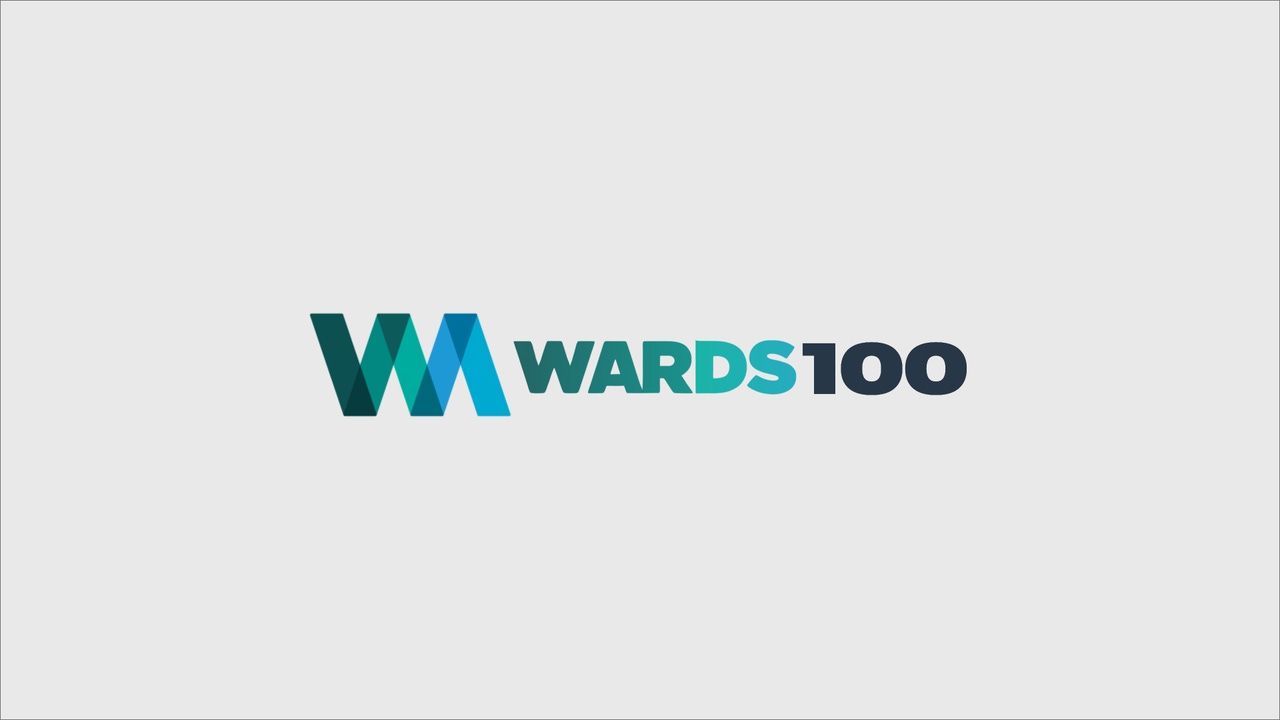
Most supplier executives would do cartwheels if they discovered an affordable way to shave just a pound off their products. Even before gasoline prices started their recent ascent, fuel efficiency was a high priority for automakers, so suppliers have been on constant watch for any opportunity to reduce weight.
Supplier Hayes Lemmerz Intl. Inc. has joined with the American Iron and Steel Institute (AISI) to develop a lightweight "microalloy" steel wheel that promises 25% in weight savings, or a whopping 5 lbs. (2.3 kg) per wheel.
The Northville, MI, supplier and AISI employed ultra high-strength materials and a "spin-thinning" process to vary the thickness of sections of the wheel relative to the strength required.
"Our wheels are going on a diet, like a lot of Americans," Ronald Kolakowski, president of the company's North American Wheels Group, says in introducing the product at the recent Society of Automotive Engineers World Congress in Detroit.He says it will be "a couple years" before the microalloy wheel appears on roads, likely in North America in the sedan market.
Most of the weight savings (4 lbs. [1.8 kg]) per wheel comes in the rim, while the remaining pound is sliced from the disc.
The company is excited about the prospects for the microalloy wheel: The process actually saves money because it requires less labor, and it also moves the industry one step closer to a standardized wheel.
The microalloy wheel allows for different cladding - high-tech mechanically locked hub caps - to be mounted to the wheel face. So an automaker can buy one wheel for an entire family of vehicles and choose appropriate cladding depending on the vehicle - sporty sedan, executive cruiser or functional family hauler.
Using multi-clad microalloy wheels across various platforms can be less expensive than conventional steel wheels if the volumes are high enough because of the significant savings in tooling costs, says John Kinstler, vice president of engineering for fabricated wheels. Aluminum is better for a low-volume run of, say, 50,000 wheels.
Weight savings are critical because as vehicles get bigger, so do wheels. Vehicles that required 14-in. wheels, such as the Ford Ranger pickup, are now using 15-in. wheels, and sport/utility vehicles (SUVs) are using 18-in. wheels. "Now we are quoting wheels at 20 ins.," Mr. Kolakowski says of future business.
Weight savings isn't the only driver behind the microalloy wheel. It's also an attempt to make steel more competitive with aluminum, which has displaced steel as the dominant wheel material. Aluminum makes up about 60% of the North American wheel market, by Mr. Kolakowski's estimates. In Europe, steel still reigns, with about 70% of the wheel market.
Hayes Lemmerz, which got its start producing wooden wheels for Henry Ford in 1895, produces a quarter of the steel wheels worldwide. It manufactures 18 million steel wheels, 9 million cast aluminum wheels and 1 million fabricated aluminum wheels a year in North America.
But Hayes Lemmerz' business is much broader than wheels. Its 1998 acquisition of CMI Intl. gave the company a significant presence in the suspension module market, recently estimated at $60 billion.
Part of that strategy is a new aluminum foundry the company is building in Montague in western Michigan. The $35 million foundry will be completed late this year and will produce aluminum suspension components beginning in 2001. The company estimates that the market for aluminum suspension components in North America will triple from $250 million currently to $750 million over the next five years.
Also at SAE, Hayes Lemmerz introduces two other concepts. The Cool-Running rotor is made of cast iron and has 72 curved cast fins cored into it to reduce brake temperatures by up to 200degreesF (93degreesC) and prolong the life of the rotor.
The Ultra-Q rotor uses a patented finishing process for lower noise, vibration and harshness. It's an estimated eight times quieter than a conventional rotor. The company demonstrated the difference by using a metal hammer to tap a conventional cast iron rotor, causing it to ring and vibrate like a bell. The Ultra-Q rotor, however, did not resonate at all. It was silent.
No one can say that Alan Johnson doesn't like a challenge. Eight months ago, he was one step ahead of the sheriff in bailing out from Federal-Mogul Corp. just before a slew of top executives were broomed out. But Mr. Johnson may have stepped into even more trouble as president and chief operating officer of battery maker Exide Corp., which former Chrysler Corp. vice chairman Robert Lutz has been trying to revive under the nose of criminal investigators. Perhaps the Exide gig wasn't what he expected, as Mr. Johnson returns suddenly to Federal-Mogul, where he worked for 30 years. In his last Federal-Mogul post, Mr. Johnson had been executive vice president-powertrain. His new title is the same, but instead of powertrain, Mr. Johnson, 52, will lord overall original equipment and aftermarket operations in the Americas and Asia. He returns a few weeks after corporate raider Carl Icahn acquires a 5.2% stake in the financially troubled Federal-Mogul. Mr. Icahn is known for turning around foundering operations.
DCT Inc. (formerly Detroit Center Tool) joins the computer giveaway trend by announcing it will make Gateway computers and unlimited AOL Internet access available to all employees. It isn't exactly a giveaway. Employee cost is $16.40 per month. . . . DuPont Automotive performance coatings will cut 900 jobs as part of restructuring following the 1999 acquisition of Herberts. Five plants will be shuttered or partially closed in Germany (Bonn and Cologne), the U.K., France and Austria. DuPont expects savings of about $80 million. . . . BorgWarner Inc. will sell two non-core business units, Fuel Systems and Kysor-Westran HVAC, which were part of the Vehicle Products business of Kuhlman Corp. acquired in 1999. The units generated about $165 million in '99 revenue.
Read more about:
2000About the Author
You May Also Like