Power Stroke Triumphs With Technology
The minimal-lag turbocharger and reverse-flow cylinder heads help explain why the Ford engine’s power delivery felt and sounded more linear and effortless during our tests.
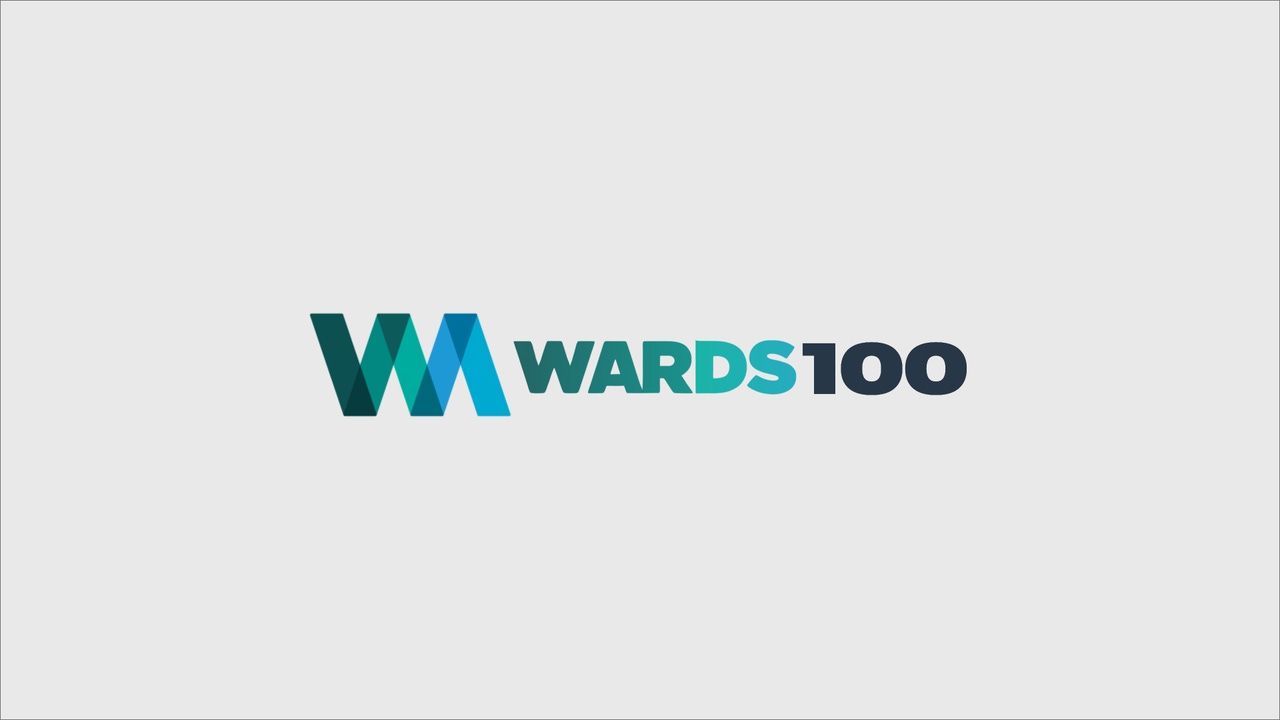
Special Coverage
Diesel Shootout

All three entries in our Best Engines Diesel Shootout boast jaw-dropping torque and surprisingly pristine emissions, but the innovative architecture, advanced materials and excellent noise, vibration and harshness characteristics of Ford Motor Co.’s Power Stroke stand out.
At the core of the Power Stroke’s advanced design is its compacted graphite iron block. CGI’s unique metallurgical structure makes it about twice as strong as the conventional cast iron used for the General Motors Co. and Chrysler Group LLC engine blocks.
That allowed Ford’s block to be designed with thinner walls and sections, making it lighter and smaller but still able to handle the tremendous forces created within a heavy- duty diesel.
The lightweight block contributes significantly to the Power Stroke’s compact design and weight advantage compared with its competitors.
CGI has a reputation for being difficult to machine, and this is the first CGI block in North America that is not used in a big Class 8 commercial truck.
However, Adam Gryglak, lead 6.7L diesel engineering manager, says Ford has extensive experience manufacturing CGI blocks in high volume in Europe. The auto maker temporarily relocated some key manufacturing personnel and resources from Europe to ensure a smooth production launch in the U.S., Gryglak says.
Another key technical advantage is the engine’s reverse-flow induction and exhaust. The cylinder heads essentially are flipped around in comparison with previous V-8 architectures, and the turbocharger is situated in the valley between the two cylinder banks, rather than on the outboard side of the banks.
Power Stroke’s innovative architecture features CGI block and reverse-flow induction/exhaust.
This new layout shortens the path hot exhaust gases follow from the time they leave the cylinder exhaust port to the time they start spinning the turbocharger vanes. That causes the turbocharger to spool up faster, resulting in quicker throttle response and less turbo lag.
This new architecture puts the Power Stroke in the vanguard of new engine design. BMW AG’s spectacular new turbocharged 4.4L gasoline V-8 features a similar layout that produces huge torque at very low rpm thanks to reverse-flow engineering.
GM has a marvelous 4.4L light-duty diesel with a similar reverse-flow design. Unfortunately, it currently sits on the shelf because of the auto maker’s limited finances and the uncertain outlook for light-duty diesels in the U.S.
Mounting the turbocharger directly to the block provides several NVH improvements, as well.
“When the turbocharger vibrates a lot, the exhaust system vibrates, too, and that is disturbing to the customer. Bolting the turbocharger directly to the block eliminates that concern, says Scott DeRaad, Ford engine NVH engineer.
DeRaad also says Ford’s turbocharger design, coupled with two resonators in the intake system as well as a third near the air cleaner, eliminates unpleasant air-handling and induction noises such as whooshes and whistles.
The minimal-lag turbo and NVH engineering help explain why the engine’s power delivery felt and sounded more linear and effortless during our driving tests.
The Duramax actually had more power and was turning in slightly faster acceleration times, but it sounded like it was working a lot harder just to stay a step or two ahead of the Power Stroke.
It’s good to hear something working hard, but if we had to spend 60 hours a week driving one of these trucks, we’d prefer the one that paces itself a little better and does not get quite so winded.
That’s a big reason why the Power Stroke won. Technology triumphed over brute force.
About the Author
You May Also Like