Profitability in QuestionProfitability in Question
Armin Mueller is explaining ZF Friedrichshafen's 3-pronged approach to modularity for a group of international journalists visiting the supplier's plant in Solihull, U.K., in the Midlands, the hub of the U.K. auto industry. Mueller, vice president-development for ZF's Lemforder chassis and axle group, says modular contracts fall into three categories: Level 1 jobs limit ZF's responsibility to component
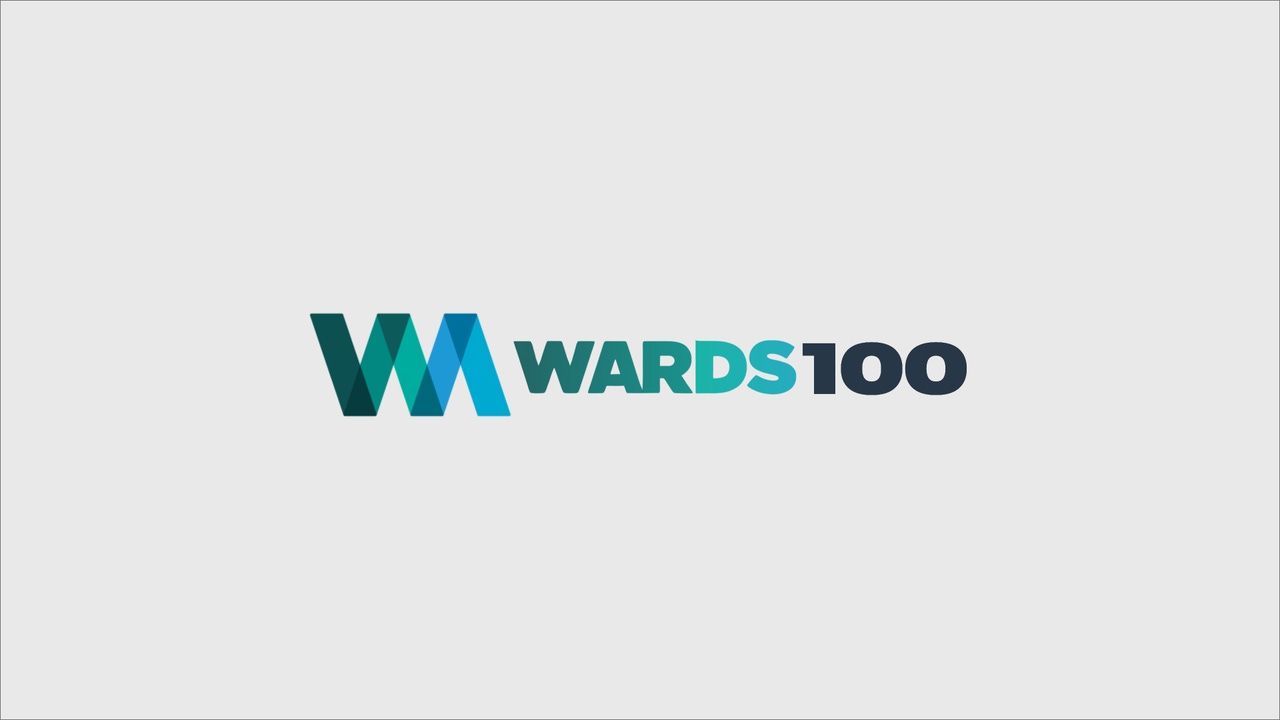
Armin Mueller is explaining ZF Friedrichshafen's 3-pronged approach to modularity for a group of international journalists visiting the supplier's plant in Solihull, U.K., in the Midlands, the hub of the U.K. auto industry.
Mueller, vice president-development for ZF's Lemforder chassis and axle group, says modular contracts fall into three categories: Level 1 jobs limit ZF's responsibility to component logistics, assembly and quality assurance, while Level 2 work gives ZF more supervision of subcontractors and responsibility for cost management.
Level 3 allows the auto maker to specify the product concept but gives ZF primary responsibility for engineering, simulating and testing components within the module.
The promise of this type of work a decade ago made modules attractive to suppliers, whose engineers claim to know their products better than their auto maker customers.
“Adding value” became the supply chain's favorite catch phrase under the theory that component producers could bolster their bottom lines with such work, while saving time and money for auto makers.
But Mueller makes it clear this model has not come to fruition, at least in the corner-module segment, when asked if Level 3 programs are more profitable than Level 2 or Level 1 business.
“No,” Mueller says simply. “They are on the same level. We take on higher risk, but we are not necessarily getting paid better for it.”
So why do it?
“That's a good question,” he says. “We look to the future.” Mueller says his company must continue working diligently to “deliver a functional benefit and a cost benefit” and to reduce complexity for customers.
Despite lean margins, Mueller says his unit remains committed to modular axle and chassis projects of any kind.
“We are competitive if our customers are competitive, and if we are making money. With all Level 3 programs, we learned a lot,” Mueller says. “Maybe we change our way a little bit in order to be really competitive.”
Here in Solihull, ZF Lemforder produces corner modules for Land Rover LR3 and the Range Rover Sport, which are assembled less than a mile away. The plant has two shifts with a total of 60 employees, represented by the General Municipal & Boilermakers labor union.
From the time Land Rover broadcasts its order for corner modules, ZF Lemforder has four hours to ship the units. Assembly takes about 15 minutes per module. The truck holds 30 units.
Logistics are key, as the front corner module comes in 20 varieties, while the rear comes in 18, depending on brake disc size and driveline configuration. Each unit must be shipped in sequence.
Production began in June 2004. Twenty-one component suppliers feed parts to the ZF facility. Brake discs come from a Brembo SpA plant in Poland, while GKN Group supplies axle halfshafts, wheel bearings, the parking-brake assembly and other hardware.
ZF estimates it produces 32% of the content for each corner module, with the remainder coming from other suppliers. For the Land Rover modules, ZF supplies front and rear control arms, stabilizer links, ball-joint assemblies, cross-axis joints and suspension bushings.
Mueller says ZF's goal is to achieve a 50-50 split in terms of content for module contracts, but he concedes the Solihull plant is barely breaking even.
“The plant still has a way to go to be really profitable,” he tells Ward's. “But in the final stage, the plant will be profitable — not a big profit, but it will be a profit which makes sense, in the right balance.”
The Solihull plant falls into ZF's Level 2 category for module contracts, meaning the auto maker led engineering and held more authority over sourcing and content decisions.
Land Rover selected the component suppliers and negotiated prices. ZF integrates and monitors the quality of incoming components and pays the suppliers.
But even with ZF supplying 32% of the content, Mueller is convinced the plant can achieve profitability through better material management and efficiency gains.
Increasing its share of content will not require an expanded product portfolio for ZF, Mueller says.
For instance, brake components make up a significant portion of a corner module, so ZF has a handful of engineers with braking expertise. Yet, ZF has no interest in producing brake components, as the sector already is saturated by major players.
“There is not enough space to grow in that area,” Mueller says. Besides, integrating another supplier's component is simple, he adds.
One key brake producer, Robert Bosch GmbH, has complained in the past that a number of its corner module contracts ended up losing money because Bosch was acting merely as an assembler, rather than adding engineering value.
One ZF insider says Bosch and other brake producers have been declining corner-module contracts with auto makers in recent years because of suspect profitability.
A Bosch spokesman says high steel prices have impacted profitability for all suppliers of corner modules, but that Bosch continues aggressively pursuing corner-module contracts.
ZF is trying to add value to corner modules by leveraging the knowledge of its Lenksysteme steering joint venture (with Bosch) and the Sachs suspension-component division, which ZF acquired in 2001.
Meanwhile, ZF continues cultivating its Solihull plant. The supplier plans to add a second assembly line eventually, but it is not clear when. Negotiations for new business continue with other auto makers, including Land Rover affiliates in Ford Motor Co.'s Premier Automotive Group.
In addition to Land Rover, ZF Lemforder produces front and rear axle systems for vehicles such as the BMW X3, X5 and Z4; Mercedes M-Class and the upcoming R-Class; and Ford Freestyle, Five Hundred and Mercury Montego.
ZF plans to produce axle sets for 1.3 million passenger vehicles this year, up from 85,000 units in 1996, the company's first year of axle production.
About the Author
You May Also Like