Racing Roots Run Deep for '12 Mustang Boss
MANY SPORTY PRODUCTION CARS HAVE roots in racing, but the '12 Mustang Boss 302 is one of few that can boast such lineage on both sides of its family tree. The OEM branch is represented by racing legend Parnelli Jones' historic 1970 Trans-Am championship a milestone event in Ford history. However, the supplier side of the Boss program can be tied to track icon Bruce McLaren. Linamar, a global producer
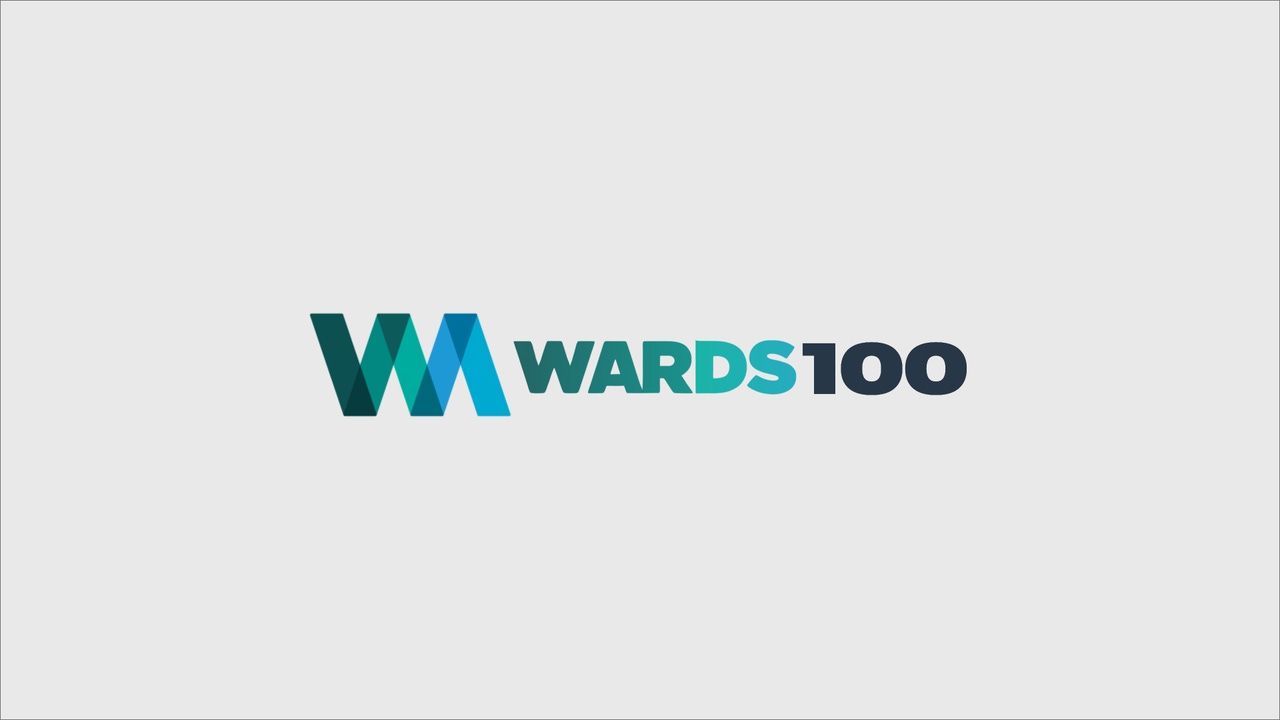
MANY SPORTY PRODUCTION CARS HAVE roots in racing, but the '12 Mustang Boss 302 is one of few that can boast such lineage on both sides of its family tree.
The OEM branch is represented by racing legend Parnelli Jones' historic 1970 Trans-Am championship — a milestone event in Ford history. However, the supplier side of the Boss program can be tied to track icon Bruce McLaren.
Linamar, a global producer of powertrain components based in Ontario, Canada, machined the intake and exhaust ports of the car's 5.0L V-8, as well as the 444-hp engine's combustion chambers.
“We also did some flow analysis on it,” says Mark Stoddart, Linamar's chief technology officer and executive vice president-marketing. “But the big thing is really the process. The process was originally developed by our McLaren Performance Technology group.”
In 2003, Linamar acquired the late racing star's engineering house, “which does all of our product and process development,” Stoddart tells Ward's.
The fusion of McLaren's engineering talent and Linamar's manufacturing expertise enabled the supplier to deliver a highly technical component in niche volumes at mass-production speed and cost, he says.
In keeping with the original Boss Mustang, Ford designed a high-performance, naturally aspirated powerplant based on its all-new “Coyote” 5.0L V-8, one of Ward's 10 Best Engines for 2011.
But the auto maker's Boss ambitions went well beyond nostalgia and mere specifications.
“The scope of the project was not to build a '69 or '70 Boss,” says Jim Farley, Ford group vice president-global marketing. “We want to get noticed in the U.S. for world-class dynamics and powertrains.”
World-class, yes. But without the expense usually associated with that distinction, says Mike Harrison, Ford's V-8 engine programs manager.
“We really wanted to keep it within the Essex Engine Plant (so) the labor cost of building the engine was the same as the base 5.0L,” Harrison says, referring to Ford's production site in Windsor, ON, Canada.
The auto maker's powertrain and process engineers huddled and “got every single bit of content we wanted,” he tells Ward's. Certain features of the V-8's design, such as increased air flow, required casting revisions.
“We actually added some material back into the ports so they could be machined out in the geometry that we needed,” Harrison says.
But the complexity and precision required to deliver that geometry proved problematic for the production process at Essex.
Enter Linamar. “Traditionally, they would have to do one operation, tear the part down and put it into another fixture,” Stoddart says. “We do it with one fixture.”
This process was conceived when McLaren engineers pondered the prospects of expanding 5-axis machining capability.
“They introduced this to (Linamar's) manufacturing group and said, ‘How can we bring this into a production environment and make it cost-effective?’” Stoddart says.
Machining intake and exhaust ports to boost engine performance is nothing new, he concedes.
“But to be able to do it in a cost-effective manner and in (series) production is what we've done. And we've actually done it for a couple of other customers. We can do it right in a 5-axis machining center, and we don't have to re-fixture the part.
“With one fixture we're able to attack all three — the intake, the exhaust ports and the complete combustion chamber,” Stoddart says.
Read more about:
2011About the Author
You May Also Like