Report Card Time Ford shows big gains in annual 'productivity' gaugeReport Card Time Ford shows big gains in annual 'productivity' gauge
Call it the paradox of profitability.In the 1998 Harbour Report, the annual industry report card on factory floor efficiency, Ford Motor Co. blew way past its domestic rivals, virtually caught up with the Japanese competition and overtook Chrysler Corp. as the most profitable automaker in North America on a profit-per-vehicle basis.Then there is the industry's perennial valedictorian, Nissan Motor
August 1, 1998
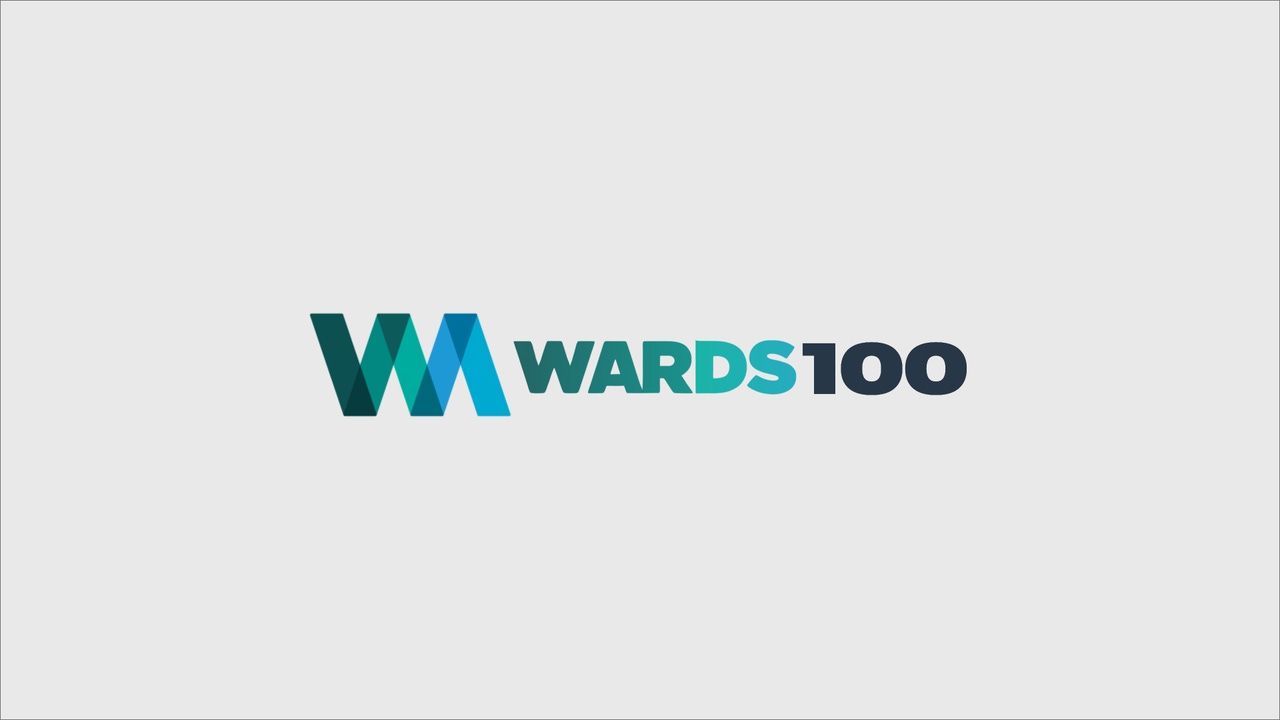
Call it the paradox of profitability.
In the 1998 Harbour Report, the annual industry report card on factory floor efficiency, Ford Motor Co. blew way past its domestic rivals, virtually caught up with the Japanese competition and overtook Chrysler Corp. as the most profitable automaker in North America on a profit-per-vehicle basis.
Then there is the industry's perennial valedictorian, Nissan Motor Co., whose Smyrna, TN, plant workers build its Sentra, Altima and the new Frontier compact pickup with an enviably lean 17 hours of labor per vehicle. Yet its U.S. sales are down more than 26% through the first half of the year. In the year ending March 31, Nissan's U.S. sales and marketing subsidiary lost $787 million.
"No matter how good you are at manufacturing, if you aren't competitive from a product and marketing viewpoint you're not going to be successful in this business," says Ronald Harbour, president of Harbour and Associates Inc., the Troy, MI, consulting company that compiles the industry's most highly regarded efficiency evaluation.
The study tends to put too much emphasis on labor costs, which account on average for 15% to 20% of the cost of building a car or truck.
But, make no mistake, productivity matters. Ford's improvement from an average of 3.09 workers per vehicle in 1996 to 2.97 last year is a major reason its return on sales from North American automotive operations were 6. 2% for the first half of this year, up from 5.5% in 1997.
To put the workers-per-vehicle score in context, Nissan scored 2.29; Honda, 2.45; Toyota, 2.55; Chrysler, 3.17; and General Motors Corp. 3.37.
But Harbour researchers also presented each company's assembly productivity in terms of hours of labor required per vehicle.
Mr. Harbour says that indicator more accurately reflects the effectiveness of overtime work. For example, some companies may run an assembly plant to make up for regularly scheduled production it couldn't achieve in a regular eight-hour shift. Others may use overtime only to meet unanticipated demand.
On that scale, Ford's performance stood out more prominently. For example, it required an average of 22.85 hours of labor per vehicle. That was less efficient than Nissan's industry-leading 17.07, but it was virtually even with Toyota's 21.3 and Honda's 22.77 hours/vehicle.
In contrast, GM needed an average of 30.32 labor hours for each car or truck, while Chrysler required 32.15 hours.
"Ford's right in the thick of it with the Japanese," says Mr. Harbour. "The surprises to us were the higher numbers for Chrysler and GM."
Chrysler officials point out that Chrysler had three assembly plants in various stages of new-model launches during the fourth-quarter when Harbour staffers collected their data. Those were Bramalea, Ont., where the '99 Chrysler Concorde, Dodge Intrepid and Chrysler 300M are built; Newark DE, where Chrysler assembles the Dodge Durango; and a plant in Windsor, Ont., that builds the Dodge Ram van.
"We also tend to run less automation than most of our competitors, which also reduces our capital investment," says Chrysler's David Barnas.
Nearly all auto-makers have tried to emulate Toyota's lean production system, but Ford appears to have made measurable strides. Four of the most efficient car assembly plants and eight of the leanest truck plants were Ford's.
The company's Atlanta and Chicago assembly plants that build the Ford Taurus and Mercury Sable were the most efficient midsize car plants on the continent, requiring less labor per vehicle than either Toyota's Georgetown, KY, or Honda's Marysville, OH, plants.
The secret: less down-time, less inventory and more flexibility from union workers who don't see greater productivity as a threat.
"Just count the number of trucks in the yard," says Robert H. Transou, group vice-president for manufacturing. "You walk down the line and you have line of sight visibility all the way down the line."
GM's average of 30.32 hours per vehicle represents a 6% improvement from 1996, says a spokesman, but there is more than a 7-hour-per-vehicle gap between GM and Ford.
Mr. Harbour commends the productivity gains GM has made in its stamping plants. A major issue in the two-month-old walkout at the Flint stamping plant is a practice known as "pegged rate" production targets. These allow some workers, particularly in the area of the plant that makes engine cradles, to meet their daily quotas in less than six hours. The company wants to either raise those rates or have the union guarantee that workers will produce for a full eight-hour shift.
While GM's stamping productivity has improved by 17% (from 6.56 hours per vehicle to 5.46 hours per vehicle) between 1994 and 1997, it still lags far behind every other major North American manufacturer.
More modern transfer presses and quicker die changes are helping, but the number of workers in each plant is not being reduced significantly, Mr. Harbour says.
For example, the number of hits per hour, the number of times the press goes up and down to stamp out a metal panel, increased from 310 to 409 within GM's stamping plants. That's below industry leader CAMI Automotive Inc., GM's joint venture with Suzuki in Ingersoll, Ont. (484 hits per hour), but well above Ford, Chrysler and Honda, all of which were below 400 hits per hour.
But when the number of hits per hour is divided by the number of workers, GM came in at the bottom of the pack with 125 hits per worker, less than a third of Toyota's industry-leading 382 hits in Georgetown, KY.
It all flows down to the bottom line.
Ford leapfrogged Chrysler in profitability per vehicle. On a pre-tax basis, Ford earned an average of $1,520 for each vehicle it produced in North America during 1997, a 91% increase from 1996. During the same period, Chrysler's fell from $1,836 to $1,336.
GM, meanwhile, earned about $415 per vehicle in North America last year, up from $234 in 1996.
Corresponding numbers for the major Japanese companies building vehicles in the U.S., Canada or Mexico were: Honda: $1,040 per vehicle, up 471% from 1996; Toyota: $1,239 per vehicle, up 29% from 1996; Nissan: $301 per vehicle, up from a loss of $287 per vehicle in 1996.
About the Author
You May Also Like