U.S. Auto Market Hits Skids in 2006; GM, Ford, Chrysler SufferU.S. Auto Market Hits Skids in 2006; GM, Ford, Chrysler Suffer
Economic difficulties and higher energy costs prompted a slowdown in the U.S. auto market in 2006.
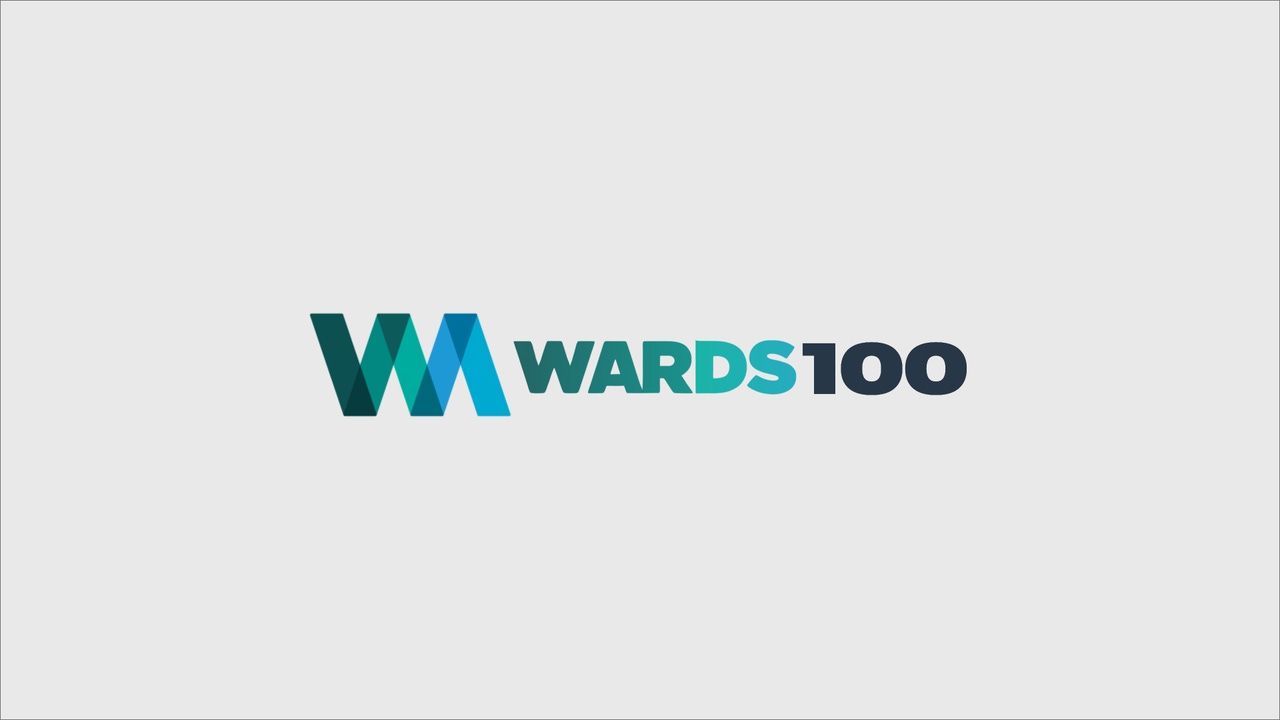
Special Report
2006 Year in Review

A volatile economy, rising fuel prices and a slowdown in job creation were not what U.S. auto makers needed in 2006.
But that’s what they got.
It was particularly bad news for the homegrown Big Three, which continued struggling to regain their financial footings under the weight of weak sales of their cash-cow large pickups and SUVs, and rising costs – even as foreign competitors siphoned away more market share and profits.
Neither did long-suffering domestic suppliers find much economic relief in 2006 as the OEMs focused ever more intently on the parts makers as a place to cut costs, while demanding they shoulder more of the burden of component design and development, as well as recall costs when those parts failed.
The prime motivating factor behind the lackluster year was the country’s economic performance stemming from the double whammy of rising interest rates and spiking energy costs that pushed gasoline, fuel oil and natural gas prices higher.
Although the economy grew at a higher-than-expected rate of 3.4% in 2006, much of that was due to a robust first-quarter in which the gross domestic product moved ahead at a 5.2% pace. Then came sharply lower rates of 2.0% and 2.5% in the second and third quarters, respectively, before the economy rebounded to 3.5% growth in the final quarter.
Rising consumer debt and gasoline prices averaging $2.05 per gallon – excluding state and local taxes, up from $1.75 per gallon in 2005, with spikes well above $3.00 per gallon in major markets during the summer driving season – put a damper on consumers’ ardor for new vehicles, especially the larger, thirstier models built mainly by Detroit’s Big Three.
While U.S. dealers nevertheless managed to retail a robust 17,048,981 new vehicles in 2006, that was down 395,348 units, or 2.3%, from the prior year and a 3-year low since 16,967,442 units were sold in 2003.
What’s more, included in the 2006 tally were record sales of medium- and heavy-duty trucks to commercial users anxious to avoid purchase- and operating-cost penalties expected from the January 2007 implementation of more stringent emissions rules for diesel engines. Buyers took possession of 544,581 medium and heavy trucks in 2006, a 9.7% increase from 2005’s 496,575, and 4.5% higher than the prior record of 521,190 posted in 1999.
Sales of light trucks, on the other hand, fell to a 4-year low of 8,723,641in 2006. Thus ended a run of sales above 9.0 million units that began with 9,028,572 trucks in 2003 and closed at 9,280,688 in 2005.
At the same time, car sales increased by 113,693 or 1.5% in 2006, to 7,780,759 units, the highest level since 2002, when sales reached 8,103,229.
But, the still relatively strong market was of little benefit to the Detroit automakers.
Based on total vehicle sales, including medium and heavy trucks, General Motors Corp., Ford Motor Co. (including their European brands) and DaimlerChrysler AG’s Chrysler Group posted an 8.1% decline to 9,170,073 from 9,974,932 in 2005. It was the Big Three’s poorest showing since 1991 –when their dealers delivered 8,868,372 cars and trucks – and netted an all-time low 53.8% market share compared with 57.2% in 2005 and 1991’s 70.6%.
In comparison, the industry’s record year of 2000 saw the Big Three account for 65.6% of 17,811,673 retail deliveries.
Meanwhile, Asian makers sold a record 6,543,341 light- and medium-duty trucks and cars in 2006, a 5.1% increase over the prior record of 6,225,649 set just a year earlier.
It was in fact the Asians’ 10th consecutive annual sales record and gave them an unprecedented 38.4% market share in 2006, compared with 35.7% the prior year and just 24.2% in 1997, when the string of sales records began.
European makers (excluding the Ford-owned Jaguar, Land Rover and Volvo brands and GM-owned Saab) accounted for 6.7% of U.S. sales in 2006, up from 6.2% in 2005, with sales of 1,137,241 light, medium and heavy vehicles compared with the prior year’s 1,076,097 deliveries.
Not surprisingly, the Big Three accounted for only 63.9% of the 11,260,277 vehicles built in U.S. plants in 2006, down from 67.2% in 2005 and 70.7% in 2004.
The Asian transplant producers, whose production share increased to a record 30.4% in 2006 from 28.2% on 2005, took up much of that output slack. It marked a 5.3 percentage-point gain in just two years, from 25.2% in 2004.
The European transplants’ share rose to 4.2% in 2006, representing a 1.1 point gain from 3.1% in 2004.
Nor was there much prospect of GM, Ford or Chrysler recovering lost ground any time, soon, according to a Ward’s production forecast through the year 2012.
Although U.S. vehicle output was projected to climb from just over 11.0 million units in 2007 to a high of 11.9 million-plus in 2011, before easing to just under 11.2 million in 2012, the Big Three were seen continuing to lose share. They were forecast to drop from 61.3% in 2007 to a low of 54.3% five years later.
According to Ward’s, Asian transplants would account for a steadily increasing share of U.S. output, climbing from a forecast 33.6% in 2007 to 36.3% in 2008, on up to 40.1% in 2012.
New plants and expansion of existing facilities would enable the Asians to reach those higher levels. Those included a new plant brought on-stream late in 2006 by Toyota Motor Engineering & Mfg. North America Inc. in San Antonio to build an all-new, larger version of the Tundra fullsize pickup aimed squarely at the heart of one of Detroit’s last profit centers.
Other new plants confirmed in 2006 included a Honda of America Mfg. Inc. facility launching in Greensberg, IN, in 2008; a Kia Motors Corp. plant slated to begin production in West Point, GA, in 2009; and one to build Toyota cross/utility vehicles opening in Tupelo, MS, in 2010.
Europeans were seen reaching a peak of 5.0% in 2009, but generally remained in the 4.1% to 4.7% range in 2007-2012.
Dedicated independent U.S.-based medium- and heavy-truck builders were forecast at between 1.0% and 1.2% through the period, peaking at 1.5% in 2009.
All of this ongoing production shift played havoc with Big Three financials in 2006.
Despite its biggest reorganization in company history – calling for the closing of 14 manufacturing and assembly plants – Ford lost a whopping $12.6 billion for the year, down from a $1.4 billion profit in 2005. As a result of Ford’s declining market share, some long-time Ford and Lincoln-Mercury dealers closed their doors in 2006, with plans by the company to pared more outlets in coming years.
Chrysler also saw its cash position plummet in 2006, despite the introduction of some hot new models. Although parent company DaimlerChrysler tallied a net profit of nearly $4.3 billion in 2006, Chrysler, due in part to its heavy dependence on the stalled light-truck market, posted a $1.4 billion loss for the year. That prompted DC management at year end to launch a quest to revamp and/or sell its U.S. manufacturing arm to quell mounting criticism from the company’s German shareholders.
Although a big improvement over the $10.4 billion loss posted in 2006, GM likewise ran in the red to the tune of just under $2.0 billion in 2006, due in part to extraordinary restructuring costs including an early retirement program for its bankrupt former parts operation, Delphi Corp.
About the Author
You May Also Like