AAS Looks at New MarketsAAS Looks at New Markets
Roof-rack producer eyes `powered' running boards Advanced Accessory Systems LLC, best known as a supplier of sport/utility vehicle (SUV) and minivan roof racks, is taking a run at two new markets: plastic body panels and retractable running boards for high-riding vehicles such as SUVs, vans and pickups.The privately owned company, formed in 1995 by former General Motors Corp. Executive Vice President
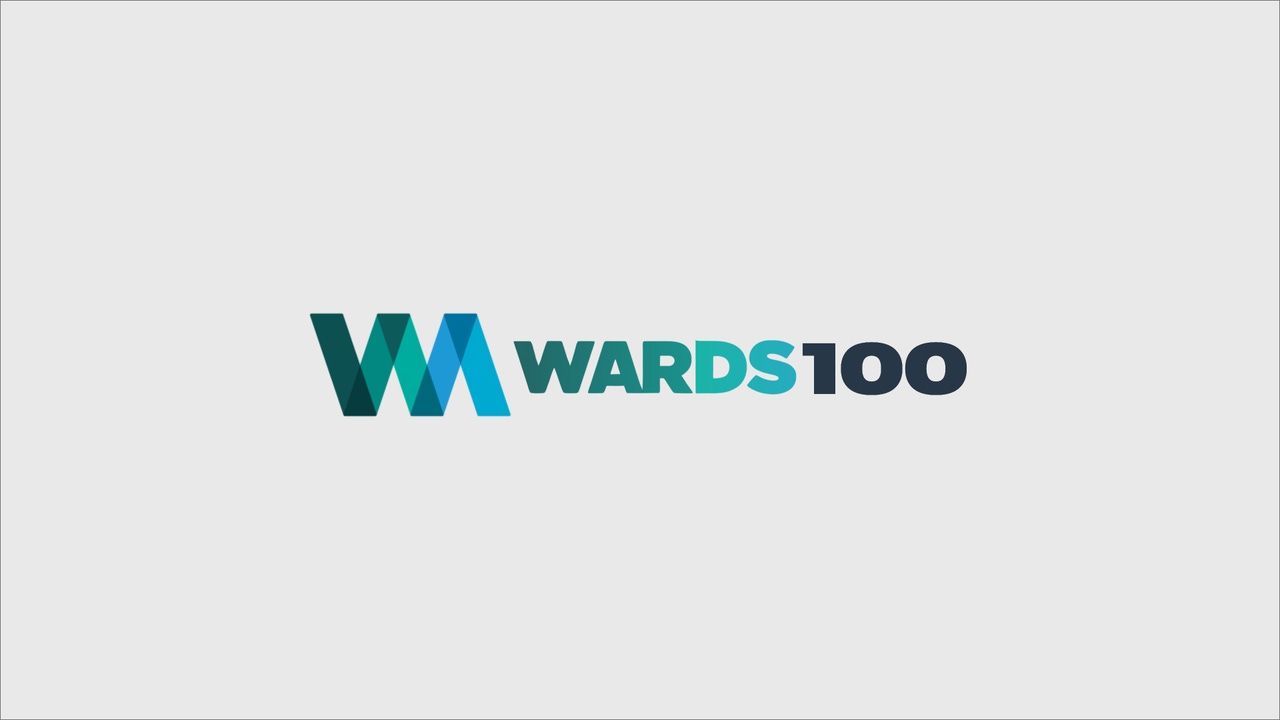
Roof-rack producer eyes `powered' running boards Advanced Accessory Systems LLC, best known as a supplier of sport/utility vehicle (SUV) and minivan roof racks, is taking a run at two new markets: plastic body panels and retractable running boards for high-riding vehicles such as SUVs, vans and pickups.
The privately owned company, formed in 1995 by former General Motors Corp. Executive Vice President F. Alan Smith and Chase Capital Partners, now spans 24 locations with 2,200 employees in 15 countries. Mr. Smith is chairman. Revenues this year are expected to reach around $320 million, up from $300 million in 1999.
Based in Sterling Heights, MI, the bulk of AAS' volume is roof racks and other add-ons such as top carriers, ski racks and bicycle racks. It also has a substantial position in tow bars (trailer hitches) and related components in both the aftermarket and as factory installed equipment.
Richard E. Borghi, chief operating officer and president of AAS' original equipment business unit, says the company is protected against a potential downturn in U.S. SUV sales by the growing variety of hybrid niche-vehicle spinoffs, most equipped with roof racks, plus emergence of 4-door pickups and three-seat SUVs and hybrids. "As these vehicles get bigger, they need more room outside to carry stuff like bikes, skis, canoes and kayaks. These racks also add to styling appeal. Everyone is trying to customize their vehicles."
It also helps that AAS recently qualified as an OE supplier to Ford Motor Co., and that the potential for expansion abroad is growing, he says.
"Overseas is now 10% to 15% of our (roof rack) business, so there's a growth opportunity there," he tells WAW. "It's mostly station wagons in Europe, but we've developed a good base there over the last few years. And we have close to 40% to 50% of the European tow-bar market."
Besides Ford, AAS now counts numerous automakers as customers for roof racks and tow-bar systems under its "SportRack" brand including DaimlerChrysler AG, General Motors Corp. (and its Opel subsidiary), Honda Motor Co. Ltd., Kia Motors Corp., Volkswagen AG, Nissan Motor Co. Ltd. Mitsubishi Motors Corp., and Subaru (Fuji Heavy Industries Ltd.).
Many of AAS' recent contracts are with Tier 1 suppliers that have responsibility for exterior components and systems, he points out. "That has expanded our need for engineering and follow-up working with their specs," he says. AAS has an advantage because its components already have met automakers' requirements regarding safety and durability, Mr. Borghi explains.
Now AAS is looking for growth in the exterior component market with new ideas that, Mr. Borghi concedes, may well turn out to be long shots.
Still in the testing stage is a new process for producing colored body panels with a Class A finish that doesn't require painting.
Developed by the company's ValTek unit, reportedly in close collaboration with DaimlerChrysler, the process involves inserting a film containing the desired color and/or design into a die. Plastic - possibly reinforced nylon or other engineered plastics - is extruded over the film under relatively low pressure. "The parts are extremely rigid; we've taken a sledge to them with no damage," he says. "They're also lighter than metal parts."
Two automakers are testing the material in prototype hoods, and if it proves feasible, AAS is eyeing deck lids, roof panels and tonneau covers.
Among advantages he cites are much lower cycle times and less than a third of the space required to make components from fiberglass. "It's also cheaper (than other plastics) because it eliminates the painting step," says Mr. Borghi.
Separately, a prominent automotive plastics engineer tells WAW that the process still has numerous wrinkles. He doubts the finish can match competitive materials, and says stability - read that "flutter" - will be tough to conquer in on-road conditions.
Mr. Borghi says AAS will take a run at producing hoods in 2001, but he's nothing if not realistic. "It could be worth a billion ... or nothing," he admits.
Perhaps more promising, at least near term, is AAS' development of retractable, "powered" running boards. "The problem (with higher-riding vehicles) is that it's relatively easy to get in, but tough to get out," he observes. "On today's vehicles men get their pants dirty and women have a tough time with high heels when they get in and out. We've got 25 or 30 concepts, all prototypes so far, to address that problem."
The most adventurous is a running board that tucks away from the elements under the vehicle and swings out automatically with the touch of a key fob. AAS showed this innovation at the recent SEMA show in Las Vegas.
Unlike fixed running boards, the AAS concepts can be made wider and still not exceed overall vehicle width set by regulation at 88 ins. (224 cm), he says.
But because they require sensors and additional circuitry, more current will be necessary - a notion that automotive electrical engineers likely will frown upon, at least until forthcoming 42-volt systems arrive, Mr. Borghi acknowledges.
He won't be nailed down on how such units might be priced, but allows that a premium of $200 to $300 per vehicle may be in the ball park.
Read more about:
2000About the Author
You May Also Like