Back to the Well
For nearly a decade, General Motors Corp. has embraced tubular hydroforming as an alternative to the tried-and-true stamping and welding of structural components such as vehicle frames. With the launch of its new GMT 360 midsize sport/utility vehicles (SUVs), GM claims yet another hydroforming milestone: It's the first time that this liquid magic has been used to shape the full-length side rails for
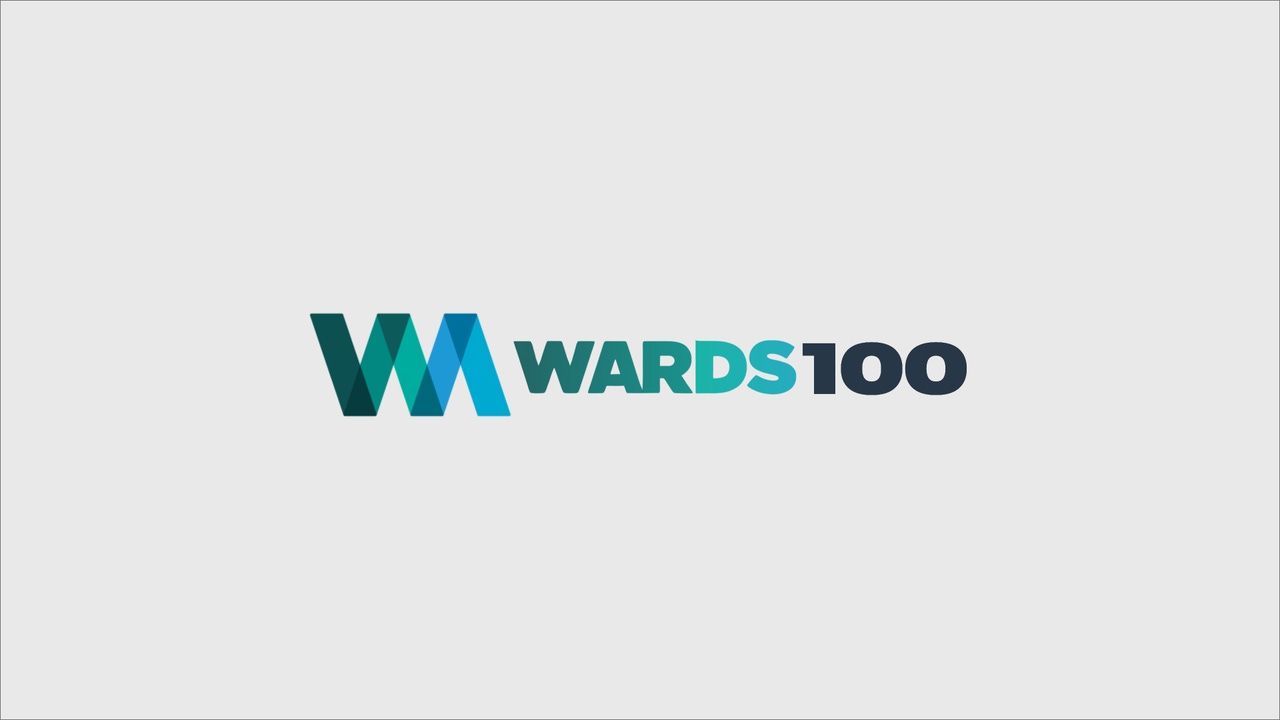
For nearly a decade, General Motors Corp. has embraced tubular hydroforming as an alternative to the tried-and-true stamping and welding of structural components such as vehicle frames.
With the launch of its new GMT 360 midsize sport/utility vehicles (SUVs), GM claims yet another hydroforming milestone: It's the first time that this liquid magic has been used to shape the full-length side rails for a truck.
It costs more money to hydroform, and cycle times are slower, but the advantages are numerous: reduced scrap, lower tooling costs due to fewer parts, more uniform wall thickness, consistent high tensile strength and rigidity and optimized weight. Welding is eliminated (or at least minimized), which makes for better dimensional control because all of the heat from welding can affect a component's geometry.
On the plant floor, the mind-numbing thunder of a conventional stamping press is replaced by a whisper-quiet hydraulic press that draws its power much like Hoover Dam — from water. Actually, it's a mixture of water and oil that is pumped under such extreme pressure that it bends thick steel as if it were a piece of paper.
GM vouches for the benefits of hydroforming, having earned 25 patents related to the technology. In February, the No. 1 automaker got a package from Washington, DC, granting a patent for the side frame rails on the GMT 360, better known as the 2002 Chevrolet TrailBlazer, Oldsmobile Bravada and GMC Envoy.
Getting their names on the patent were engineers Chi-Mou Ni, GM's resident hydroforming expert, and Ferdous Ghazi, who was design release engineer for the new frame.
With hydroforming, the engineers managed to design one frame for all current GMT 360 variants, including 4-wheel-drive, 2-wheel-drive, right- and left-drive versions. The previous-generation vehicle required eight different frames, partly because the SUVs and pickups were on the same platform, Mr. Ghazi says. The GMT 360 marks the separation of the SUVs from the small pickups. A second, larger frame will be necessary when the 7-passenger version arrives in early ’02.
The old frame rails were stamped in C-shaped pieces that required welding along the entire length of the rail and in the middle where the pieces were joined. The new frame requires only one weld in the middle where the front and rear lengths are mated.
In this crucial midsection, the mission was to make the frame stronger and larger but with reduced mass. A conventionally produced frame would require more metal. With the “magic” of hydroforming, the center section of the frame is stretched vertically by 20%, like a rubber band, reducing the thickness of the tube but increasing rigidity, Mr. Ni says.
GM's testing found that the frame performs well against the benchmark Lexus LX 470. Compared to the previous-generation frame, the GMT 360 offers a 270% improvement in torsional stiffness, Mr. Ni says.
Cycle time for one piece of the rail is 35 seconds, which the engineers say is good enough to compete with stamping. Once in the final die, fluid is pumped through the frame rails at an astounding 25,000 psi. The process will save an estimated 6.3 million lbs. of steel scrap per year.
The three-model SUV family was just launched, but GM already is convinced the hydroformed frame will contribute mightily to its success. Last month, the automaker proudly displayed a frame after 300,000 miles of hard testing. The body was removed to reveal a frame that looked like new, but just needed a little cleaning.
At a recent Automotive Press Assn. speech in Detroit, Tom Wallace, vehicle line executive for the SUVs, gave credit to the Budd Co., which acquired six Schuler presses for two assembly lines to produce the frames at Budd's plant in Kitchener, Ont.
Budd also applies a corrosion-resistant electro-coat before shipping the frame to GM's assembly plant in Moraine, OH. The Chevrolet SSR roadster, slated for production for 2003, also will receive a version of the frame, GM says.
The vehicle launch has had a few glitches (for instance, a parts shortage halted production for a day), but no bottlenecks have been attributed to Budd's hydroforming, the GM engineers say.
8 Years of Hydroforming
Here's a sampling of GM's hydroforming applications
’94 W-car IP beam
’95 G-car engine cradle
’97 Corvette lower frame rails, IP bar, roof bow
’98 Seville roof rail inner, engine cradle
’99 GMT800 chassis frame front, cross bar
’00 Bonneville, LeSabre, Aurora engine cradle
’01 DeVille roof rail inner, engine cradle